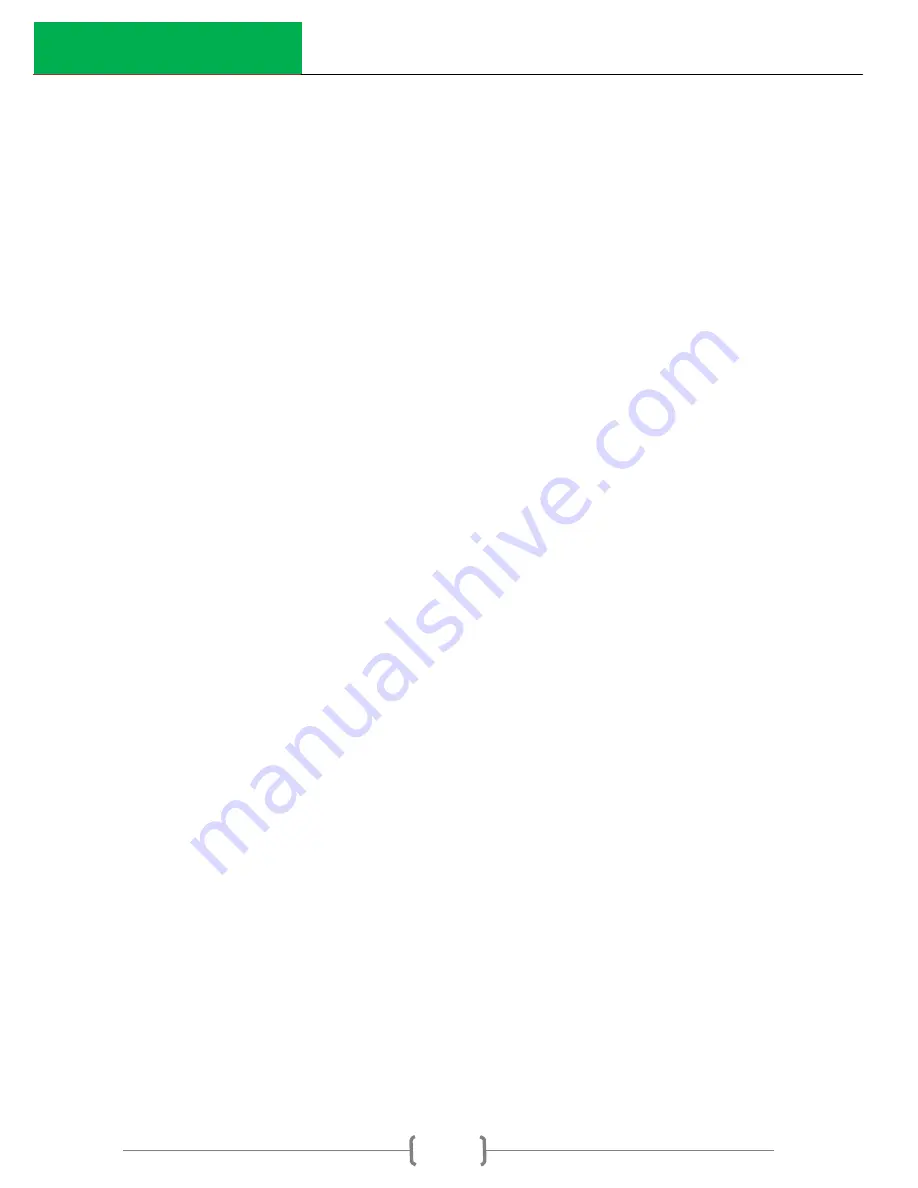
InstroTek
4
Law, which would indicate a vacuum pump requirement capable of 29.7 in.
Hg (30-0.3 in. Hg) of vacuum.
P
1
V
1
= P
2
V
2
Where, P
2
is the pressure on the bag during the sealing process, V
2
is the void
volume not occupied by the plastic bag after sealing and V
1
is the total air
volume of the bag not occupied by the core.
The vacuum performance of the unit should be checked on a yearly basis, or
as needed, by using an absolute vacuum gauge that can be placed directly
inside the chamber. This will ensure the integrity of the pump, vacuum hoses
and the seals.
2.
Testing time after sealing.
The CoreLok plastic bags are designed with multi-
composition layers of plastic. The requirement for the plastic is to be flexible
to conform to the sample and to provide enough strength to resist punctures
from asphalt samples. To accomplish this specification the molecular
structure of the bag is designed to hold vacuum levels produced by the
CoreLok for approximately one hour. The water displacement test should be
conducted within 2 minutes after the sealing process. Samples can be
tested after this time but two items have to be looked at prior to testing. First,
a major leak can occur in the bag by mishandling of the bag before or after
the sealing process. This could easily be seen within a few seconds of
sealing. With careful handling, most of these leaks can be avoided. Second,
due to excessive stretching of the plastic around sharp points, “micro” leaks
can occur. This can be defined as thinning of the plastic, which will allow air
into the bag over a very long time (hours). This does not affect the results if
the sample is tested within the first 30 minutes of the sealing process. The
surface tension on the bag is sufficient to keep water out of the bag.
For best results, the bag should be checked prior to testing to ensure tight fit
around the sample. Presence of a major leak is obvious in this process with
immediate loosening of the bag.
3.
Sample temperature prior to sealing.
Introduction of air into the chamber
after heat- sealing the bag is done in a controlled manner to avoid artificial
compaction of the sample in the chamber. The bag conforms to the sample
in a slow and methodical way. Tests with the CoreLok indicate that