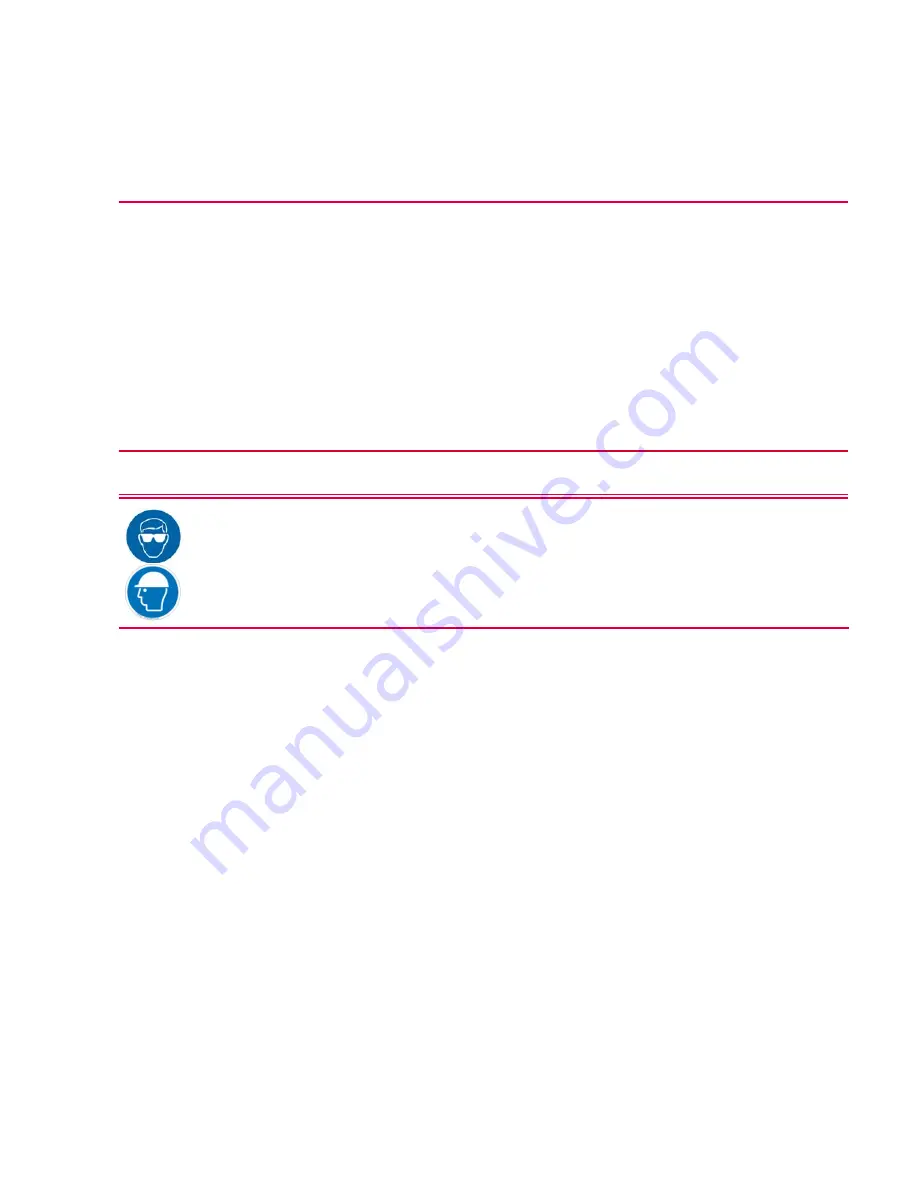
51
Chapter 4
Maintenance
•
•
•
•
•
•
•
•
•
•
Warning
General maintenance recommendations
Only the maintenance procedures outlined in these instructions should be performed by the customer or
their representative. All other maintenance and repairs should be performed by Instron Service
personnel only.
Always wear appropriate personal protective equipment when preparing, operating and
maintaining this equipment. Personal protective equipment should include, but is not
limited to, eye protection and head protection. Other types of personal protective
equipment may also be needed. You must perform your own risk assessment and take
appropriate measures to protect yourself from harm.