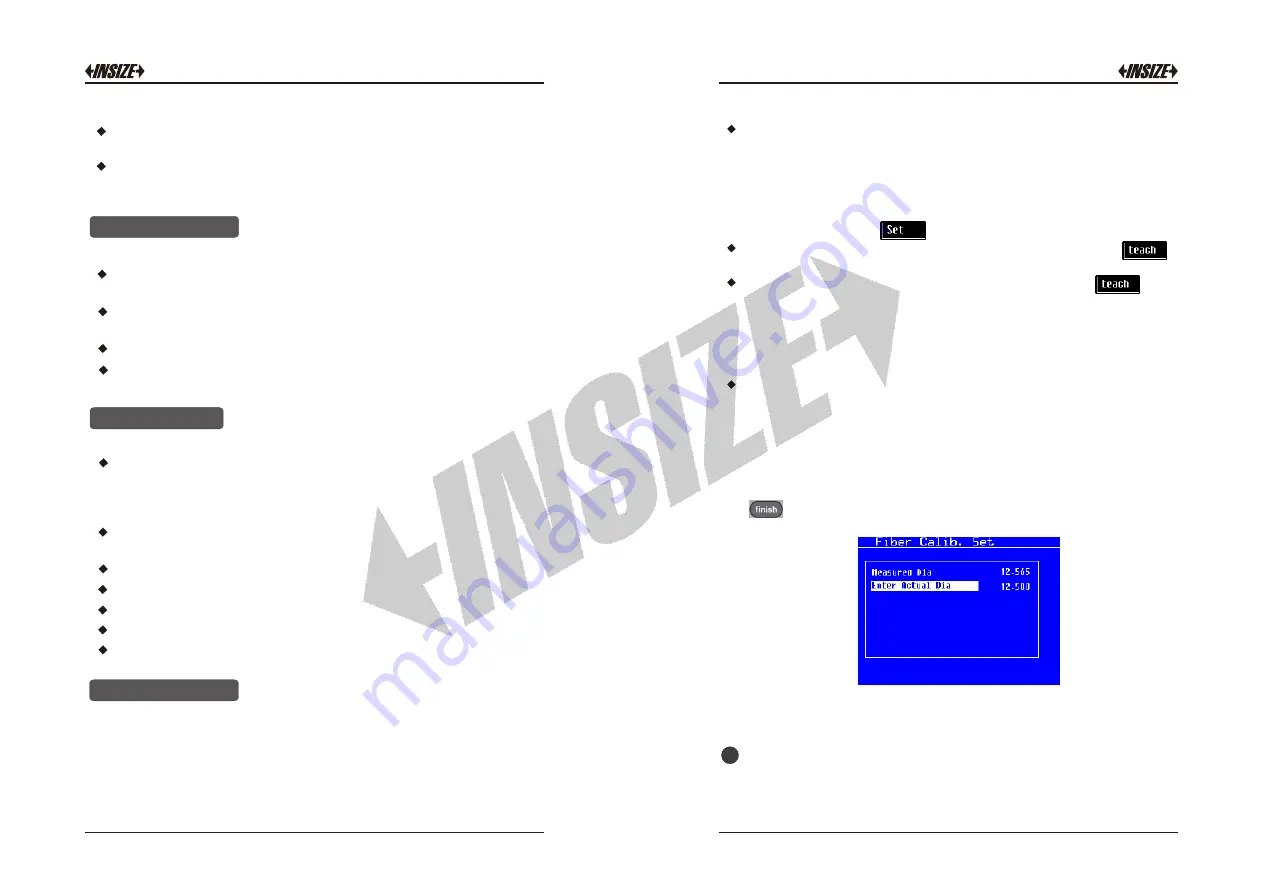
5
Set Factory Settings: All the engineering settings are set to
factory default parameters.
Configure Footswitch: Enables the user to assign any key from
keyboard to footswitch 1 and 2.
X, Y Liner Setup
Scale Resolution: Sets the scale (encoder) resolution
(
0.1, 0.2,
0.5, 1, 2, 5, 10, 20, 50µm
).
Display Resolution: Sets the display resolution
(
0.1, 0.2, 0.5, 1, 2,
5, 10, 20, 50µm
).
Axis
Direction: Sets encoder counting direction.
Machine
ref: Sets machine reference for the axis.
Count per Revoln (CPR): In case of auto, the DRO calculates the
counts between the two index marks and calculates the CPR
automatically. In case of manual selection the user needs to enter
the CPR value.
Resolution (Deg): Selects the display resolution for the angular
axis
(
0.5, 0.2, 0.1, 0.05, 0.01, 0.005, 0.001, 0.0005°
)
.
Axis
Direction: Sets encoder counting direction
(
CW or CCW
)
.
Machine
Ref: Sets machine reference for the axis.
Count Mode: Selects the counting mode
(
Rollover or Continues
)
.
Display Mode: Selects the display units: DDMMSS or DDDEC
.
Axis Lock: Enables / Disables the angular axis position settings.
Z Angular Axis
Axis calibration is required to compensate for errors arising due to
wear and tear in machine, encoder misalignment etc. Each axis can
be calibrated for Linear Errors or Segmented errors as applicable.
Axis Calibration
22
Screen Gain (<10000) – This sets the gain of the amplifier. The
gain depends on the magnification and the light source. Adjust
this such that the Screen intensity on light region displays counts
above 3000 counts to 4000. In case of higher magnifications
where the counts doesn't reach the required value even if the gain
is set to 100, then minimum of 2000 counts should be ensured for
good results. Press { }key to set the gain value.
Now bring the screen sensor in the light region and press { }
key.
Now move the screen sensor in to dark region. Press { } k ey
to teach dark to the DRO. Here note that the counts in the dark
region are less than that in the light region.
NOTE: Every time the light intensity changes it is recommended
to te a ch l i g h t a n d d a rk re g i o n to th e D R O fo r p ro p e r
measurements. No need to change the gain of the system.
Now perform Edge calibration. In this mode the selection is
provided for bore or shaft measurements. If the user wants to
check bore jobs he has to perform bore calibration using F.O.
Edge detection prior to measurements.
NOTE: It is mandatory to calibrate the type of job either bore or
shaft prior to measurements using F.O. Edge detection.
Now probe the circle as per procedure explained earlier. Press
[ ] key to complete the measurement. Following screen is
displayed.
Now enter the standard diameter of the circle. The DRO will
calculate the calibration factor and apply it during the
measurements by Edge detector.
Cross
Calibration
:
The cross calibration function eliminates the difference between
2