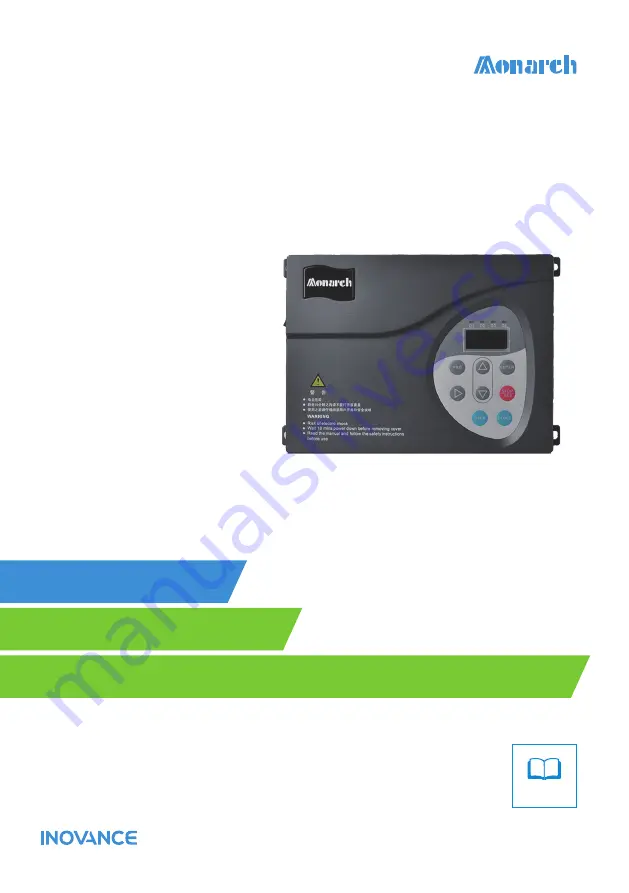
User Guide
NICE900 Series
Integrated Door Operator Controller
Suzhou Inovance Technology Co., Ltd.
Add.: No. 16 Youxiang Road, Yuexi Town, Wuzhong District, Suzhou 215104, P.R. China
Tel: +86-512-6637 6666
Fax: +86-512-6285 6720
Service Hotline: 400-777-1260
http: //www.inovance.com
Shenzhen Inovance Technology Co., Ltd.
Add.: Building E, Hongwei Industry Park, Liuxian Road, Baocheng No. 70 Zone, Bao
’
an District, Shenzhen
Tel: +86-755-2979 9595
Fax: +86-755-2961 9897
Service Hotline: 400-777-1260
http: //www.inovance.com
NICE900 Series Int
egr
ated Door Oper
ator Contr
oller User Guide
Copyright Shenzhen Inovance Technology Co., Ltd.
A02
Data code 19010269
User Guide
Summary of Contents for NICE-D-A-S0P2
Page 6: ...1 Safety Information and Precautions...
Page 12: ...2 Product Information...
Page 16: ...3 Mechanical and Electrical Installation...
Page 23: ...Chapter 3 Mechanical and Electrical Installation 22...
Page 24: ...4 Operation and Trial Running...
Page 41: ...Chapter 4 Operation and Trial Running 40...
Page 42: ...5 Function Code Table...
Page 54: ...6 Description of Function Codes...
Page 89: ...Chapter 6 Description of Function Codes 88...