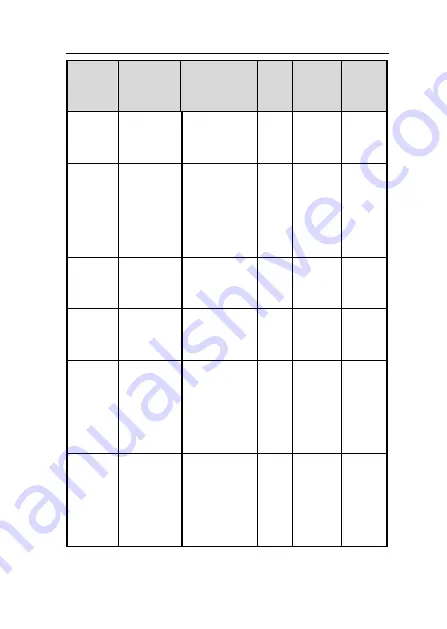
MD021 Plastic Wire Drawing Machine User Manual
Function
Code
Name
Range
Min.
Unit
Default Property
F0-02
Maximum
frequency
50.00 Hz to
200.00 Hz
0.01
Hz
100.00
Hz
★
F0-03
Preset
frequency
0.00 Hz to
maximum
frequency
(F0-02)
0.01
Hz
50.00
Hz
☆
F0-04
Acceleratio
n time
0.00s
to
300.00s
0.1s
1.00s
☆
F0-05
Deceleratio
n time
0.00s
to
300.00s
0.1s
0.00s
☆
F0-06
Motor rated
power
0.1
kW
to
1000.0 kW
0.1
kW
Depend
on the
motor
power
★
F0-07
Motor rated
voltage
0 V to 480 V
1 V
Depend
on the
motor
power
★