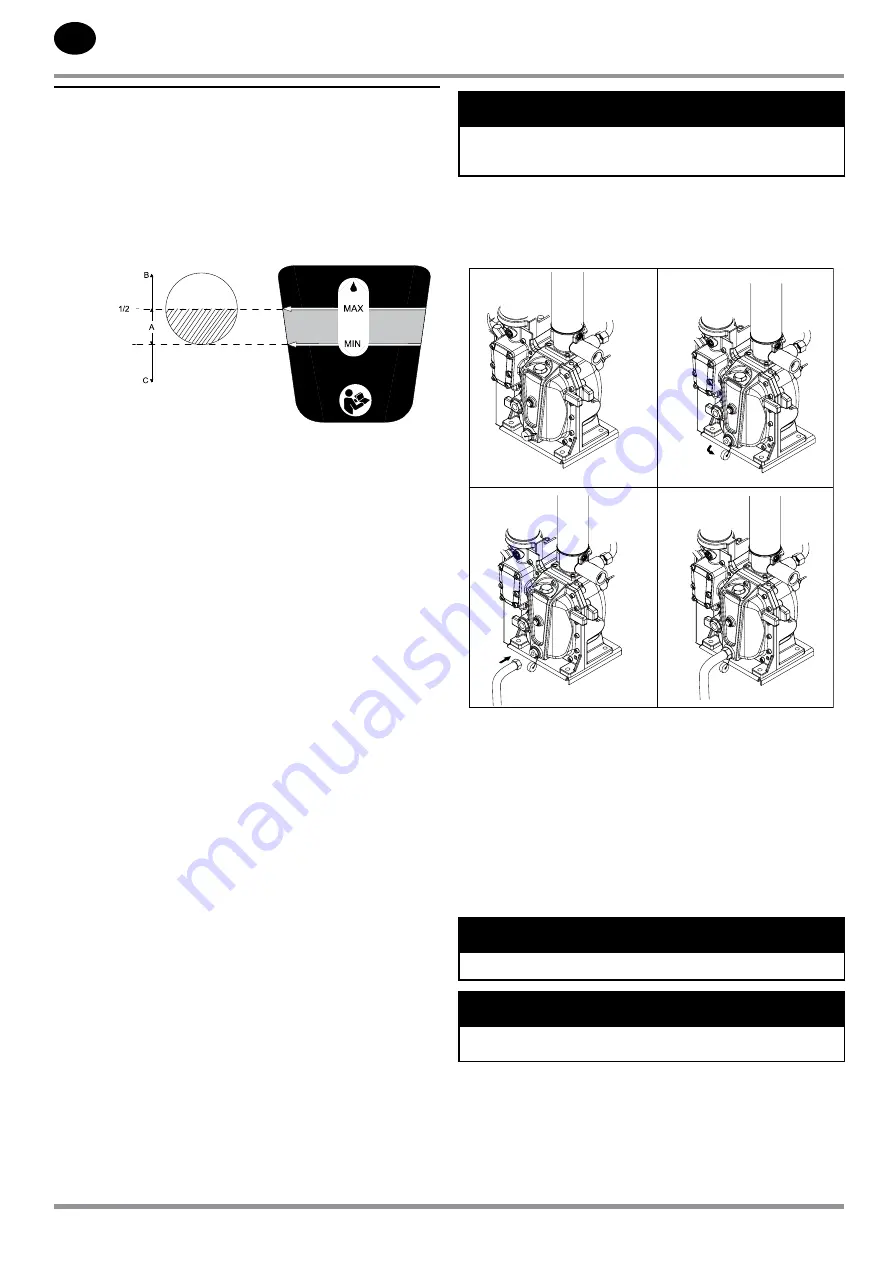
EN
EN-4
80448517 Rev A
Routine Maintenance
This section refers to the various components which require periodic
maintenance and replacement.
Refer to safety information and maintenance procedures prior to carrying out
any of the maintenance in the following sections.
Checking Coolant Level
A.
Correct at operating temperature
B.
Too much
C.
Too little
Figure 1: Coolant Level in Sight Glass
See Figure 1.
The coolant level should be checked daily. A coolant level sight glass is
located on the front of the sump. While the compressor is running loaded
at operating temperature (ten minutes running loaded), coolant should fill
the sight glass half-way (See Figure 1). Do not allow the coolant levels to go
beyond the centerline of the sight glass or increased carryover may occur. The
compressor includes a coolant level decal which shows the proper coolant
level range appropriate for operation. When the coolant level is visible in the
sight glass at the level indicated by the green area on the decal, then the
compressor has the proper quantity of coolant. If the coolant level is in the
red area above the green, then the compressor is over filled. If the coolant
level is in the red area below the green, the compressor is under filled.
When the unit is shut down, coolant will usually fill up the sight glass. Do not
adjust level based on level at shutdown. Proper level is always set for running
unit at operating temperature.
Adding Coolant
If it is determined that coolant must be added, follow the steps below:
1. Stop the compressor.
2. Isolate the compressor from the external air system.
3. Press the emergency stop to vent the separator tank and airend.
Fixed speed compressors can take more than two minutes to fully
de-pressurize once stopped.
4. Ensure the main power disconnect is locked off and tagged.
5. Slowly unscrew the coolant fill plug to verify all pressure has been
released.
6. Add coolant.
7. Replace the coolant fill plug and restart the compressor.
8. Recheck the coolant level.
9. Repeat the above steps until the coolant level is visible within the
specified range, as explained above.
NOTICE
Do not add coolant through the intake of the compressor, as this can
result in overfilling, saturation of the separator filter element, and
coolant carry-over downstream .
Draining Coolant
It is recommended to drain the coolant immediately after the compressor has
been operating as the coolant will drain faster and any contaminant will still
be in suspension.
1
2
3
4
Figure 2: Coolant Drain location
See Figure 2.
1. Slowly unscrew the coolant drain cap.
2. Screw drain hose (24096984) onto the drain valve. As you do so,
the drain valve will open, causing coolant to drain out through the
hose.
3. Allow the coolant to flow into a suitable container.
4. After drainage, remove the drain hose and replace drain valve cap.
5. Dispose of waste coolant in accordance with local and governmental
regulations.
NOTICE
Coolant should be drained from the cooler and coolant scavenge tube .
NOTICE
Shorter coolant change intervals may be necessary if the compressor
is operated in adverse conditions .
RELEASED 16/Dec/2014 10:49:53 GMT
Summary of Contents for R4-11 kW
Page 19: ...RELEASED 16 Dec 2014 10 49 53 GMT...
Page 20: ...ingersollrandproducts com 2014 Ingersoll Rand RELEASED 16 Dec 2014 10 49 53 GMT...
Page 39: ...RELEASED 16 Dec 2014 10 49 53 GMT...
Page 40: ...ingersollrandproducts com 2014 Ingersoll Rand RELEASED 16 Dec 2014 10 49 53 GMT...
Page 60: ...ingersollrandproducts com 2014 Ingersoll Rand RELEASED 16 Dec 2014 10 49 53 GMT...
Page 80: ...ingersollrandproducts com 2014 Ingersoll Rand RELEASED 16 Dec 2014 10 49 53 GMT...