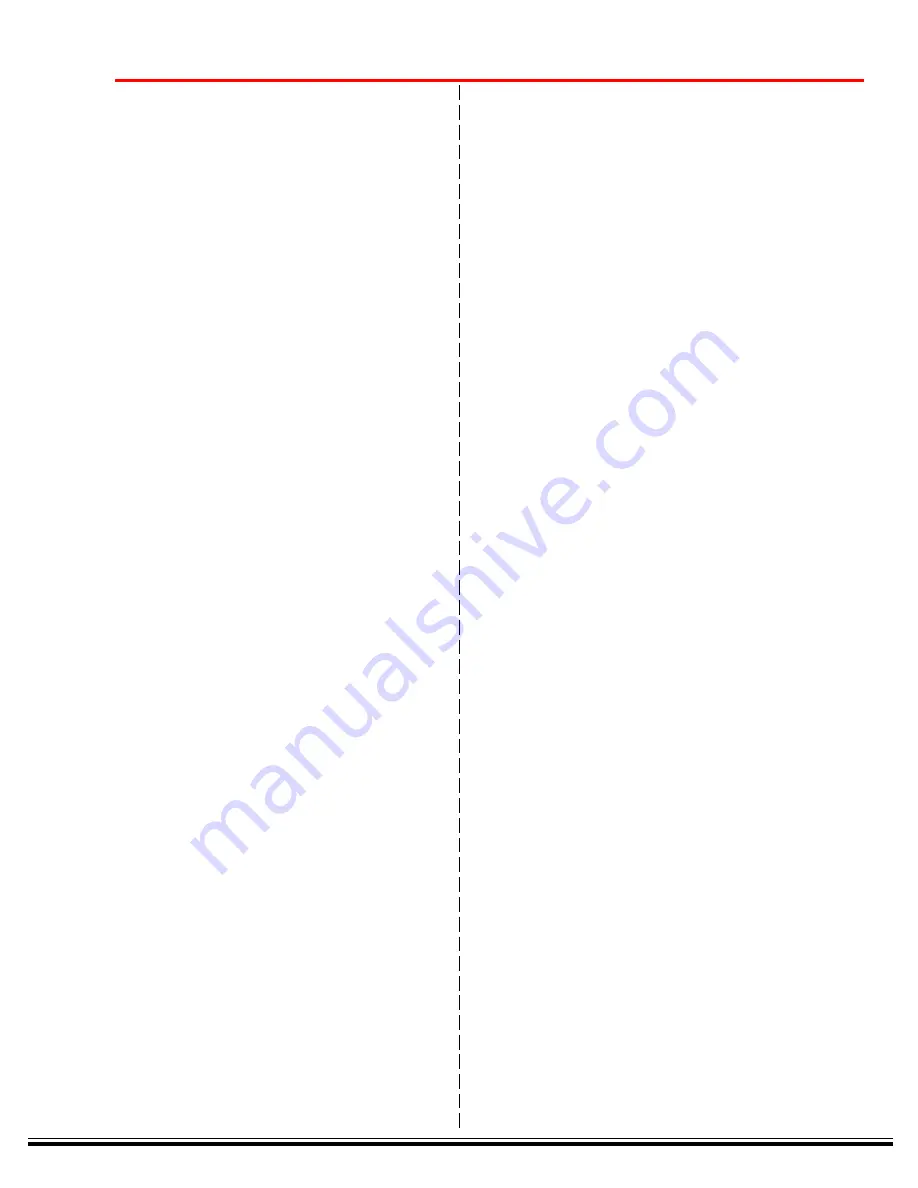
15
•
Freight Damage – Freight damage is not covered
under warranty. Should your dryer incur freight
damage, file a claim with the carrier immediately. At
the option of the claimant, you may contact a local
contractor to do a thorough investigation and repair the
damaged dryer. You may also return the dryer to IR,
freight prepaid. The factory will perform the repairs
chargeable to the original consignee. The customer
would then include these costs on their claim.
•
Dryer Alteration by Distributor or End User – This
warranty does not cover alteration of the dryer or failure
of dryer components caused by such alterations.
•
Economic Loss – This warranty does not cover any
economic loss, extra expense including payment for
the loss of time, pay, inconvenience, storage, loss of
dryer use, dryer rental expense, lodging, meals, or
other travel costs.
•
Maintenance – Performing normal maintenance
services as detailed in the maintenance schedule are
not covered and are at the customers expense includ-
ing cleaning condenser, drains and filters.
Chargeable Service Calls
IR reserves the right to decline any warranty claim, with or
without proper authorization, in which non-warrantable
condition was found. In the event this occurs, the cus-
tomer should be billed for the call as standard service.
Warranty Registration
Each dryer comes with a service manual. In the last
pages of this manual there will be a warranty registration
card. The card must be filled out and returned to us within
30 days of start-up, to receive warranty.
International Warranty
Our policies cover equipment within the United States and
Canada. Any units shipped to or sold outside of the United
States or Canada will carry a two year, parts only warranty.
The IR Disclaimer
IR makes no other warranty of any kind whatsoever,
expressed or implied and all warranties of merchantability
and fitness for a particular purpose are hereby disclaimed
by IR. IR shall in no case be subject to any obligation or
liability whatsoever with respect to product or services
manufactured or furnished by IR or any acts of omission
relating thereto. The remedy provided under this warranty
shall be the sole, exclusive, and only remedy provided
available to the purchaser. Under no circumstances shall
IR be liable for any special, indirect, incidental or conse-
quential damage, losses or delays however caused.
IR reserves the right to make changes in dryers built and/
or sold by them at any time without incurring any obliga-
tion to make the same or similar changes on dryers
previously built and/or sold by them.
In Conclusion
Our philosophy is clear. We will stand behind it and uphold
the most professional and expedient service to our distribu-
tors and ultimately our customers. We are always review-
ing our warranty policy. We feel our policy is as good as
any in the industry. If you feel another manufacturers
warranty policy, as a whole, is better, submit the manufac-
turers literature and we will consider its qualities in our next
policy review.
Thank you for choosing an IR product !!
Summary of Contents for R Series
Page 6: ......
Page 7: ......
Page 8: ......
Page 9: ......
Page 16: ...16 CONTROLPANEL ...
Page 18: ...18 MANUAL Optional Electronic Panel ...
Page 37: ......
Page 38: ......
Page 39: ......
Page 40: ......
Page 41: ......
Page 42: ......
Page 43: ......
Page 44: ......
Page 45: ......
Page 46: ......
Page 47: ......
Page 48: ......
Page 49: ......
Page 50: ......
Page 51: ......
Page 52: ......
Page 53: ......
Page 54: ......
Page 55: ......
Page 56: ......
Page 57: ......
Page 58: ......
Page 59: ......
Page 60: ......
Page 61: ......
Page 62: ......
Page 63: ......
Page 64: ......
Page 65: ......
Page 66: ......
Page 67: ......
Page 68: ......
Page 69: ......
Page 70: ......
Page 71: ......
Page 72: ......
Page 73: ......
Page 74: ......
Page 75: ......
Page 77: ......