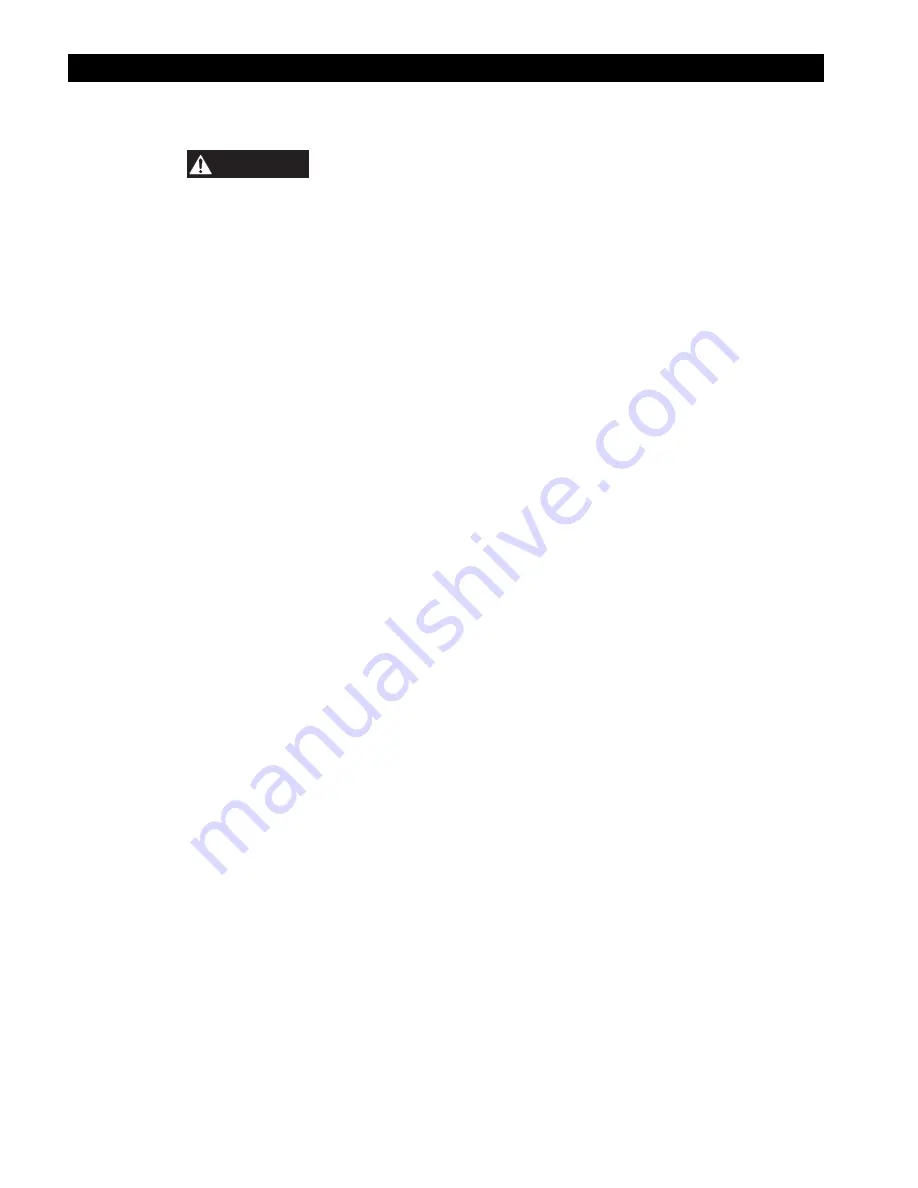
20
3.
ELECTRICAL SYSTEM. Visually inspect all connections
and components for indication of damage or loose
connections. Shut off and disconnect power prior to
removing inspection covers, repairing any damage or
tightening connections.
4.
SUSPENSION PARTS. All statically loaded parts are
known as suspension parts. Refer to Table 4 Nut Torque in
“INSTALLATION” section.
Periodic Inspection
Frequency of periodic inspection depends on the severity of
usage:
NORMAL
HEAVY
SEVERE
yearly
semiannually
quarterly
Disassembly may be required for HEAVY or SEVERE usage.
Keep accumulative written records of periodic inspections to
provide a basis for continuing evaluation.
Inspect all the items in “Frequent Inspection”. Also inspect the
following:
1.
FASTENERS. Check all rivets, split pins, capscrews and
nuts. Replace if missing or tighten if loose.
2.
ALL COMPONENTS. Inspect for wear, damage,
distortion, deformation and cleanliness. If external evidence
indicates the need, disassemble. Check shafts, wheels, side
plates, bearings, and covers. Replace worn or damaged
parts. Clean, lubricate and reassemble.
3.
SUPPORTING STRUCTURE. Check for distortion, wear
and continued ability to support load. A visual inspection of
connecting bolts should be done periodically depending on
frequency of use.
4.
TROLLEY. Check that the trolley wheels track the beam
properly. Refer to “INSTALLATION” section. Check that
wheels are not excessively worn and inspect side plates for
spreading due to bending. Ensure trolley wheels and beam
are clean. Remove any oil, grease or buildup to avoid
slipping and ensure unobstructed trolley operation. Do not
operate the trolley until problems have been determined
and corrected.
5.
LABELS AND TAGS. Check for presence and legibility.
Replace if necessary. Refer to “WARNING LABELS” and
“PARTS LIST” sections for label requirements.
Trolleys Not in Regular Use
1.
A trolley which has been idle for a period of one month or
more, but less than one year, should be given an inspection
conforming with the requirements of “Frequent Inspection”
prior to being placed into service.
2.
A trolley which has been idle for a period of more than one
year should be given an inspection conforming with the
requirements of “Periodic Inspection” prior to being placed
into service.
3.
Standby trolleys should be inspected at least semiannually
in accordance with the requirements of “Frequent
Inspection”. In abnormal operating conditions trolleys
should be inspected at shorter intervals.
Inspection information is based in part on American National
Standards Institute Safety Codes (ASME B30.16).
WARNING
• All new, altered or modified equipment should be inspected
and tested by personnel instructed in safety, operation and
maintenance of this equipment to ensure safe operation at
rated specifications before placing equipment in service.
• Never use trolley that inspection indicates is damaged.
Frequent and periodic inspections should be performed on
equipment in regular service. Frequent inspections are visual
examinations performed by operators or service personnel and
include observations made during routine equipment operation.
Periodic inspections are thorough inspections conducted by
personnel trained in the safety, operation and maintenance of
this equipment. ASME B30.16 states inspection intervals depend
upon the nature of the critical components of the equipment and
the severity of usage.
The inspection intervals recommended in this manual are based
on intermittent operation of the trolley eight hours each day, five
days per week, in an environment relatively free of dust,
moisture, and corrosive fumes. If the trolley is operated almost
continuously or more than the eight hours each day, more
frequent inspections will be required.
Careful inspection on a regular basis will reveal potentially
dangerous conditions while still in the early stages, allowing
corrective action to be taken before the condition becomes
dangerous.
Deficiencies revealed through inspection, or noted during
operation, must be reported to designated personnel instructed in
safety, operation and maintenance of this equipment. A
determination as to whether a condition constitutes a safety
hazard must be decided, and the correction of noted safety
hazards accomplished and documented by written report before
placing the equipment in service.
Records and Reports
Inspection records, listing all points requiring periodic
inspection should be maintained for all load bearing equipment.
Written reports, based on severity of service, should be made on
the condition of critical parts as a method of documenting
periodic inspections. These reports should be dated, signed by
the person who performed the inspection, and kept on file where
they are readily available for authorized review.
Frequent Inspection
On trolleys in continuous service, frequent inspection should be
made by operators at the beginning of each shift. In addition,
visual inspections should be conducted during regular operation
for indications of damage or evidence of malfunction.
1.
OPERATION. Check for visual signs or abnormal noises
(grinding etc.) which could indicate a potential problem. Do
not operate the trolley until all problems have been
corrected.
2.
CONTROLS. During operation of trolley, verify response
to pendant is quick and smooth. Ensure that the Up/Down
and Left/Right controls return to neutral when released. If
trolley responds slowly or movement is unsatisfactory, do
not operate trolley until all problems have been corrected.
INSPECTION