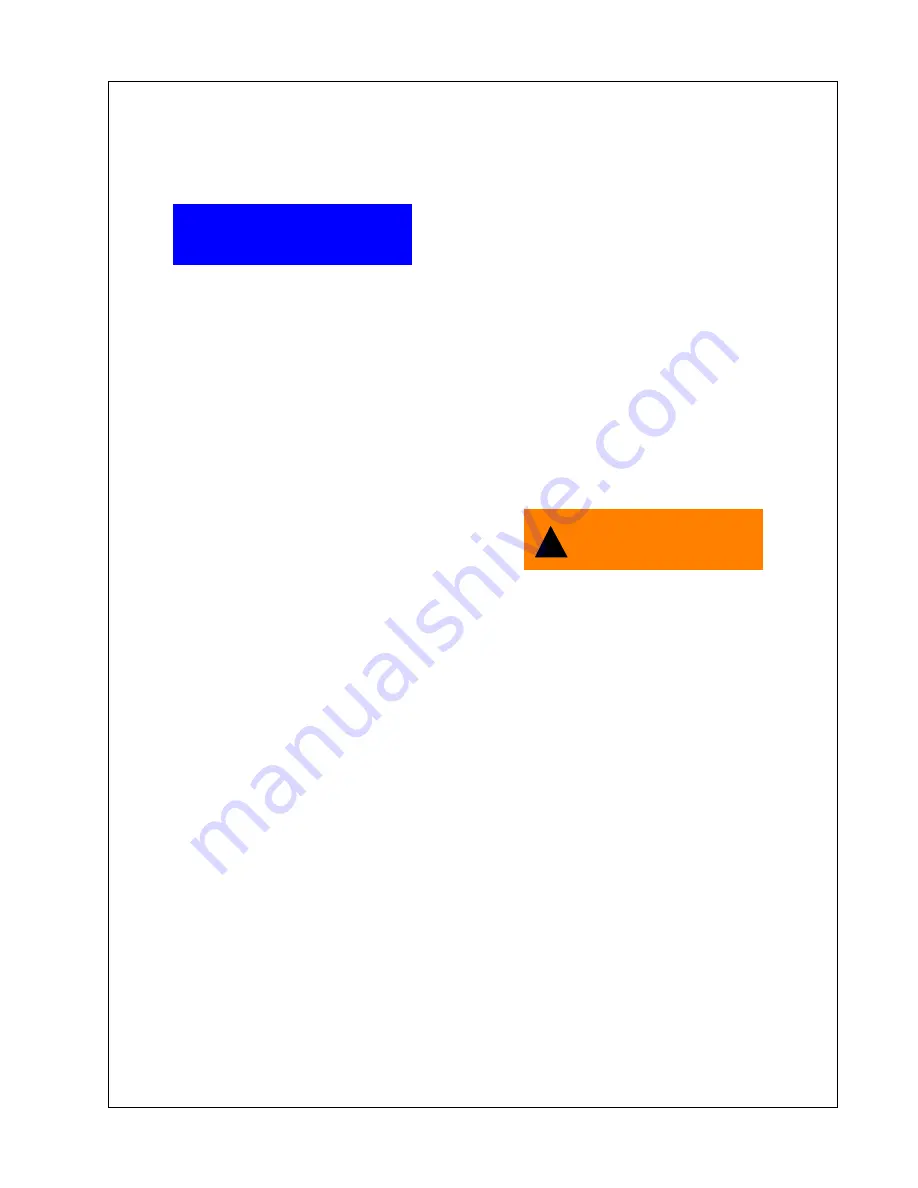
MAINTENANCE
Operating & Maintenance Manual
51
3. Inspect the oil filter head to be sure the
gasket was removed with the oil filter
element. Clean the gasket seal area on
the oil filter head.
NOTICE
Installing a new oil filter element when
the old gasket remains on the filter
head, will cause an oil leak and can
cause property damage.
4. Lubricate the new filter gasket
with the same oil being used
in the machine.
5. Install new filter by turning the
element clockwise until
gasket makes initial contact.
Tighten an additional 1/2 to 3/
4 turn.
6. Start unit and allow to build up
to rated pressure. Check for
leaks before placing unit back
into service.
Compressor Oil Cooler
The compressor lubricating and cooling oil is
cooled by means of the fin and tube-type oil
cooler, located beside the radiator. The
lubricating and cooling oil, flowing internally
through the core section, is cooled by the air
stream from the cooling fan flowing past the
core section. When grease, oil and dirt
accumulate on the exterior surfaces of the oil
cooler, its efficiency is impaired.
Each month it is recommended that the oil
cooler be cleaned by directing compressed
air which contains a nonflammable, non-
caustic safety solvent through the core of the
oil cooler. This should remove the
accumulation of grease, oil and dirt from the
exterior surfaces of the oil cooler core so that
the entire cooling area can transmit the heat
of the lubricating and cooling oil to air stream.
In the event foreign deposits, such as sludge
and lacquer, accumulate in the oil cooler to
the extent that its cooling efficiency is
impaired, a resulting high discharge air
temperature is likely to occur, causing shut
down of the unit. To correct this situation it
will be necessary to clean it using a cleaning
compound in accordance with the
manufacturer’s recommendations.
Compressor Oil
The lubricating and cooling oil must be
replaced every 500 hours of operation or six
(6) months, whichever comes first. Refer to
warranty section about extended warranty.
Receiver-Separator Systems
WARNING
!
High pressure air can cause severe
injury or death from hot oil and flying
parts. Always relieve pressure before
removing caps, plugs, covers or other
parts from pressurized air system.
• Open service valve at end of machine.
• Ensure pressure is relieved, with BOTH:
— Discharge air pressure gauge reads
zero (0).
— No air discharging from service valve.
Remove plug in bottom of separator tank to
drain compressor oil.
When adding oil, remove and replace (make
tight) plug on side of separator tank.
In the compressor lubricating and cooling
system, separation of the oil from the
compressed air takes place in the receiver-
separator tank. As the compressed air enters
the tank, the change in velocity and direction
drop out most of the oil from the air.
Summary of Contents for P105WJD
Page 5: ...1 Foreword ...
Page 7: ...Foreword 3 ...
Page 8: ...Foreword 4 ...
Page 9: ...1 Drawbar Notice ...
Page 11: ...3 Section 1 Safety ...
Page 15: ...Safety Operating Maintenance Manual 7 ...
Page 16: ...Operating Maintenance Manual Safety 8 ...
Page 18: ...Operating Maintenance Manual Safety 10 ...
Page 19: ...Safety Operating Maintenance Manual 11 ...
Page 21: ...13 Section 2 WARRANTY ...
Page 26: ...Operating Maintenance Manual WARRANTY 18 ...
Page 28: ...Operating Maintenance Manual WARRANTY 20 ...
Page 29: ...29 Section 3 Noise Emission ...
Page 34: ...Operating Maintenance Manual Noise Emission 34 ...
Page 35: ...35 Section 4 General Data ...
Page 38: ...Operating Maintenance Manual General Data 38 ...
Page 39: ...39 SECTION 5 OPERATION ...
Page 47: ...SECTION 5 OPERATION Operating Maintenance Manual 47 ...
Page 48: ...Operating Maintenance Manual SECTION 5 OPERATION 48 ...
Page 49: ...47 Section 6 MAINTENANCE ...
Page 57: ...55 Section 7 LUBRICATION ...
Page 59: ...LUBRICATION Operating Maintenance Manual 57 ...
Page 60: ...Operating Maintenance Manual LUBRICATION 58 ...
Page 61: ...57 Section 1 Trouble Shooting ...
Page 70: ...WORD INDEX 9 2 Manual Name ...