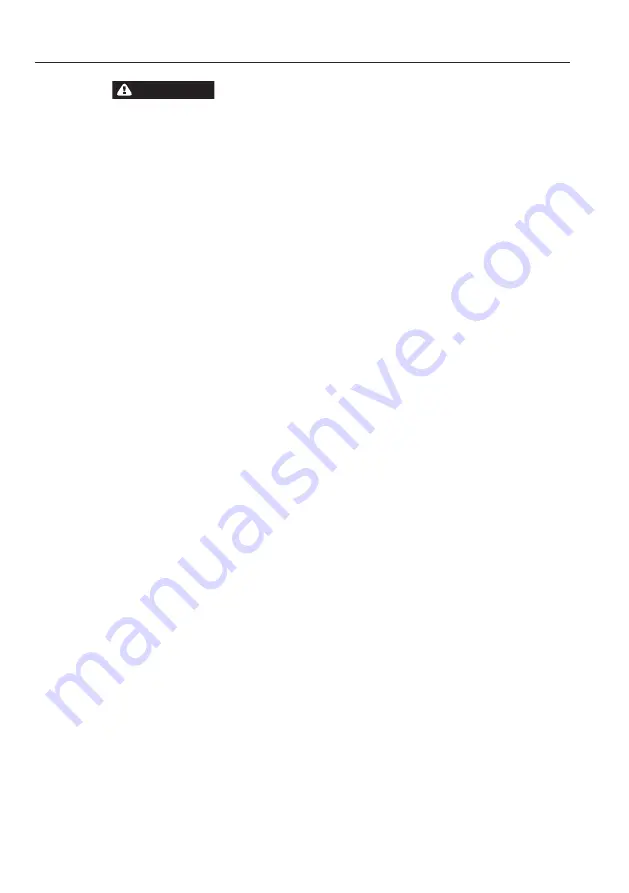
10
03523545_ed15
Maintenance Section
WARNING
Always use protective eyewear when performing maintenance
on a motor or operating a motor.
Always turn off the air supply and disconnect the air supply line
before installing, removing or adjusting any accessory on this
motor, or before performing maintenance on this motor. Failure
to do so could result in injury.
Disassembly
General Instructions
1. Do not disassemble the motor any further than necessary to
replace or repair damaged parts.
2. Do not remove any part which is a press fit in or on a
subassembly unless the removal of that part is necessary for
repairs or replacement.
3. Whenever grasping a motor or part in a vise, always use leather-
covered or copper-covered vise jaws to protect the surface of the
part or motor and help prevent distortion. This is particularly true
of threaded members and housings.
4. When removing the Planet Gear Shafts 33, 39, 40 or 47), support
the motor end of the assembly and press the Shafts out toward
the motor end. The shaft holes through the web are slightly
tapered so that the Shafts have a tighter fit in the front web.
5. Do not press any needle bearing from a part unless you have a
new needle bearing on hand for installation. Needle bearings are
always damaged during the removal process.
Disassembly of the Motor
1. Unscrew and remove one Air Strainer (1) for non-reversible
models and two Air Strainers for reversible models from the
Backhead (2).
2. Using a 3/16” hex wrench, unscrew and remove the three
Backhead Cap Screws (11), Lock Washers (12) and separate the
Backhead from the Motor Housing (10). Remove the Backhead
Gasket (3).
3. For Standard Exhaust models, slide the Exhaust Deflector (4)
with the Muffler (8) off the Motor Housing. For Piped-Away
Exhaust Models, slide the Exhaust Deflector (5) and Muffler (8)
off the Motor Housing and remove the Exhaust Deflector Front
Seal (6) and Exhaust Deflector Rear Seal (7) from the grooves
inside the Exhaust Deflector.
4. Using a 3/16” hex wrench unscrew and remove the three Gear
Case Cap Screws (11) and Lock Washers (12).
5. Separate the assembled Gear Case (59) from the Motor Housing
and set the assembled Gear Case aside.
6. For D, K, M or N ratio motors, remove the Motor Spacer (30) and
two Motor Retaining Washers (22).
For all other models, remove the two Motor Retaining Washers
(22).
7. Grasp the pinion of the Rotor (17) and pull the assembled motor
out of the Motor Housing. It may be necessary to gently tap
the face of the Motor Housing with a plastic hammer to jar the
assembly free.
8. Grasp the Cylinder (19) in one hand and using a plastic hammer,
sharply rap the spline on the end of the Rotor to remove the
Front End Plate (20) and Front Rotor Bearing (21) which will free
the Cylinder and Vanes (18). Remove the Cylinder Dowel (16).
9. Jar the Front Rotor Bearing out of the Front End Plate by bumping
the End Plate on a wooden block.
10. Using snap ring pliers, remove the Rear Rotor Bearing Retainer
(13) from the hub of the Rotor and remove the Rear Rotor
Bearing (14) and Rear End Plate (15).
Disassembly of the Gearing
1. For P, Q, S or U ratio, grasp the Gear Head Bearing (56) and pull
the assembled Gear Head (51) out of the Gear Case (59).
2. For P, Q, S or U ratio, using a bearing puller, pull the Gear Head
Bearing off the rear hub of the Gear Head.
3. For P, Q, S or U ratio, support the short hub end of the Gear Head
on the table of an arbor press and press the Gear Head Planet
Gear Shafts (54) from the Gear Head. Make certain the Shafts are
pressed out toward the short hub because the holes in the Gear
Head are tapered smaller toward the front of the Gear Head.
4. For P, Q, S or U ratio, remove the Gear Head Planet Gears (52)
from the Gear Head.
5. For P ratio, remove the Rotor Pinion (55).
6. For P, Q, S or U ratio, if the Gear Head Planet Gear Bearings (53)
must be replaced, press them from the Planet Gears.
7. Holding the Gear Case, push the output end of the Spindle (31,
37 or 45) to move the Spindle Assembly out the motor end of the
Gear Case.
8. Using a bearing puller, pull the Spindle Rear Bearing (36, 44 or 50)
off the rear hub of the Spindle.
9. Using a bearing puller, pull the Spindle Front Bearing (32, 38 or
46) off the front hub of the Spindle.
10. For D ratio, support the short hub end of the Spindle on the
table of an arbor press and press the Spindle Drive Plate Shafts
(40) from the Spindle, Make certain the Shafts are pressed out
toward the short hub because the holes in the gear frame of the
Spindle are tapered smaller toward the output end of the spindle
shaft. Remove the Drive Plate (41) from the Spindle.
For all other ratios, support the short hub end of the Spindle
on the table of an arbor press and press the Spindle Planet Gear
Shafts (33, 39 or 47) from the Spindle. Make certain the Shafts are
pressed out toward the short hub because the holes in the gear
frame of the Spindle are tapered smaller toward the output end
of the spindle shaft. Remove the Spindle Planet Gears (34, 42 or
48) from the Spindle.
11. If the Spindle Planet Gear Bearings (35, 43 or 49) must be
replaced, press them from the Planet Gears.
12. For P, Q, S or U ratio, insert a hooked tool into the flange end of
the Gear Case and catching the spindle end of the Internal
Gear (57), pull it from the Gear Case.
Assembly
General Instructions
1. Always press on the Inner ring of a ball-type bearing when
installing the bearing on a shaft.
2. Always press on the Outer ring of a ball-type bearing when
pressing the bearing into a bearing recess.
3. Whenever grasping a tool or part in a vise, always use leather-
covered or copper-covered vise jaws. Take extra care not to
damage threads or distort housings.
4. Except for bearings, clean every part and wipe every part with a
thin film of oil before installation.
5. Check every bearing for roughness. If an open bearing must be
cleaned, wash it thoroughly with a clean suitable solution and
dry with a clean cloth. Sealed or shielded bearings should not be
cleaned. Work grease into every bearings before installation.
6. Apply a film of O-ring lubricant to every O-ring before installation.
7. When installing the Planet Gear Shafts (25 or 36), support the
spindle end of the assembly and press the Shafts in toward the
spindle end. The shaft holes through the web are slightly tapered
so that the Shafts have a tighter fit in the front web.
8. Unless otherwise noted, always press on the stamped end of a
needle bearing when installing a needle bearing into a recess.
When installing Spindle Planet Gear Bearings (49), always insert
one Bearing into each end of the Gear. Never use one Bearing as
a pressing plug for the second Bearing. Use a bearing inserting
tool similar to the one shown in Dwg. TPD786.