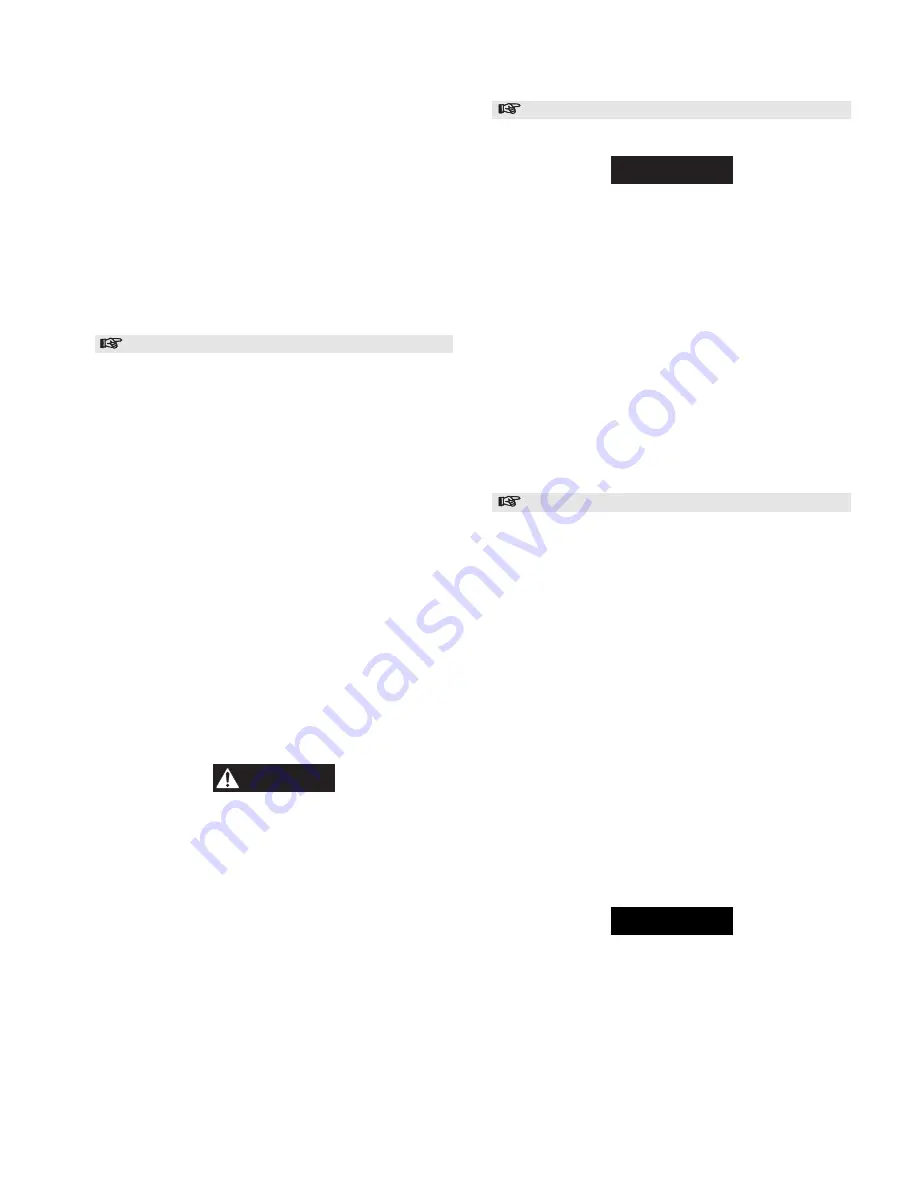
27
d.
Remove retainer ring (432) and separate valve piston
(431) and poppet seat (428).
e.
Remove and discard ‘O’ rings (426), (427) and (430).
f.
Push shaft (401) to the front of valve body to cause pin
(405) to push seat restrictor (403) out of valve body.
Remove and discard ‘O’ ring (404).
g.
Support shaft (401) on both sides of pins (405) and
push pins out.
h.
Insert allen wrench into open hole in sleeve (408) and
back out setscrew (407) a couple of turns to loosen
sleeve on shaft (401). Remove sleeve.
8.
To remove valve assemblies (413) or pins (412) remove
capscrew (465), washer (417) and spring washer (416).
From the exhaust port, using a soft material probe, push the
valve assembly or pin up through the top of the valve body
until it can be grasped from the top. Pull out valve
assembly or pin.
Pendant Operated Pilot Control Valve Disassembly
Optional feature. Refer to Dwg. MHP1408.
It is recommended that the valve be separated from the winch
and moved to a clean work area before disassembly of valve.
1.
Disconnect the air line fittings at the shuttle valve body
(479).
2.
Disconnect the air inlet line at the valve inlet. On units
equipped with an emergency stop valve, disconnect air inlet
at the valve.
3.
To separate valve from motor, alternately loosen capscrews
(442) on adapter (440). Capscrews and washers (434)
cannot be removed until adapter is separated from valve
body (410). Separate valve as an assembly from winch
motor rotary valve housing (247).
4.
Remove capscrews (441) and separate adapter (440) from
valve body. Remove and discard gasket (424).
To disassemble the end caps of the pendant operated control
valve:
1.
Disconnect the air line from the elbow fitting (482) located
on the cylinder (451).
2.
Disconnect tubing at fittings and remove capscrews (528).
Separate emergency stop valve as an assembly from valve
body (410).
3.
Remove capscrews (437) and (439) and washers (433).
Separate valve cap assembly (450) from valve body (410).
CAUTION
• Do not disassemble valve cap assembly further unless
necessary to conduct a repair. Valve cylinder (451) and valve
cap (438) are press fit together. Close fit tolerances cannot be
maintained if disassembled. If repair is required, replace
these parts to ensure secure fit.
4.
To separate the valve cap assembly into component parts,
place the valve cap in a vise. Using a strap wrench, or
similar tool, remove cylinder.
5.
Remove seal cup (456). Remove and discard ‘O’ ring
(457).
6.
Pull piston (454) from cylinder. Remove and discard ‘O’
ring (453).
7.
Remove capscrew (465), retainer spring (459) and spring
(452).
8.
To further disassembly valve body refer to ‘Lever Operated
Control Valve’ section and conduct steps 6 through 8 with
the following exceptions:
a.
Step 6a. applies to both ends of the valve shaft,
therefore, remove pins (406) and shims (444) from
both ends of valve shaft (401).
b.
Step 7a. does not apply to the Pendant Operated Pilot
Control Valve. Skip this step and proceed to step 7b.
Live Air Throttle Valve Disassembly
Optional feature. Refer to Dwg. MHP1380.
NOTICE
• Match mark throttle valve parts to ensure proper re-
assembly.
1.
Remove the two capscrews (302) and lockwashers (304)
that hold the valve body retainer (305).
2.
Mark the square end on the valve body (316) and the
handle (300) to ensure correct orientation during re-
assembly.
3.
Drive out pin (301) and remove handle (300).
4.
Make note on how the spring (303) is positioned before
removing it. Pull valve body (316) out of the valve bushing
(314) while disconnecting the spring (303).
5.
Remove seal rings (315) from valve body (316).
6.
Check parts for score marks or wear.
7.
Measure clearance between the valve bushing (314) and
valve body (316). Clearance between valve bushing and
valve body should not exceed 0.002 inch (0.05 mm) or
excessive air leakage will occur.
Motor Disassembly
Refer to Dwg. MHP0690.
1.
Remove the five capscrews (255) from the exhaust flange
(254).
2.
Remove the rotary valve housing (247) by pulling it out of
the motor housing (217) as an assembly with the exhaust
flange (254).
3.
Remove rotary valve (250) by pulling it out from the
assembly through the motor end of the rotary valve housing
(247).
4.
Remove exhaust flange (254) from rotary valve housing
(247) by gently tapping edges of flange with a soft hammer
until seal is loosened.
5.
Remove each cylinder head (201) by removing the four
capscrews (200). Remove head gaskets (209) and discard.
6.
Remove mounting flange (216) from motor by pulling
straight away from motor.
7.
Pull the cylinder liner (208) straight out.
8.
Position the piston (204) at the top of its stroke. In this
position, with the cylinder liner pulled out in step 7, the
wrist pin (203) can be removed. Remove one retainer ring
(205) from either side of piston (204). Push the wrist pin
(203) out by hand from one side. If the wrist pin is too tight
it is acceptable to carefully heat the piston to 200° F (93°
C) or less and then push the wrist pin out.
NOTICE
• If original piston, wrist pin, connecting rod or cylinder liner
are to be reassembled, number each set. Also add radial
alignment marks for each piston and cylinder liner to the
motor housing.
9.
Remove the remaining cylinder liners and pistons as
described in steps 7 and 8. To remove the crank assembly,
all pistons and cylinder liners must be removed.
10. Crank assembly (231) can now be removed with the oil
slinger (230) by pulling straight out from the motor housing
(217). Use care while guiding the connecting rods (206)
through the inside of the motor housing.
Summary of Contents for ManRider force5 FA5AMR-LAK1
Page 39: ...39 WINCH CROSS SECTION DRAWING ...
Page 40: ...40 WINCH ASSEMBLY PARTS DRAWING ...
Page 42: ...42 MOTOR ASSEMBLY PARTS DRAWING ...
Page 44: ...44 DISC BRAKE ASSEMBLY PARTS DRAWING ...
Page 48: ...48 LEVER OPERATED CONTROL VALVE ASSEMBLY PARTS DRAWING ...
Page 50: ...50 PENDANT OPERATED PILOT CONTROL VALVE ASSEMBLY PARTS DRAWING ...
Page 52: ...52 REMOTE PENDANT ASSEMBLY PARTS DRAWING ...
Page 54: ...54 SHUTTLE VALVE ASSEMBLY PARTS DRAWING ...
Page 56: ...56 EMERGENCY STOP AND OVERLOAD ASSEMBLY PARTS DRAWING ...
Page 64: ...64 SERVICE NOTES ...
Page 65: ...65 SERVICE NOTES ...