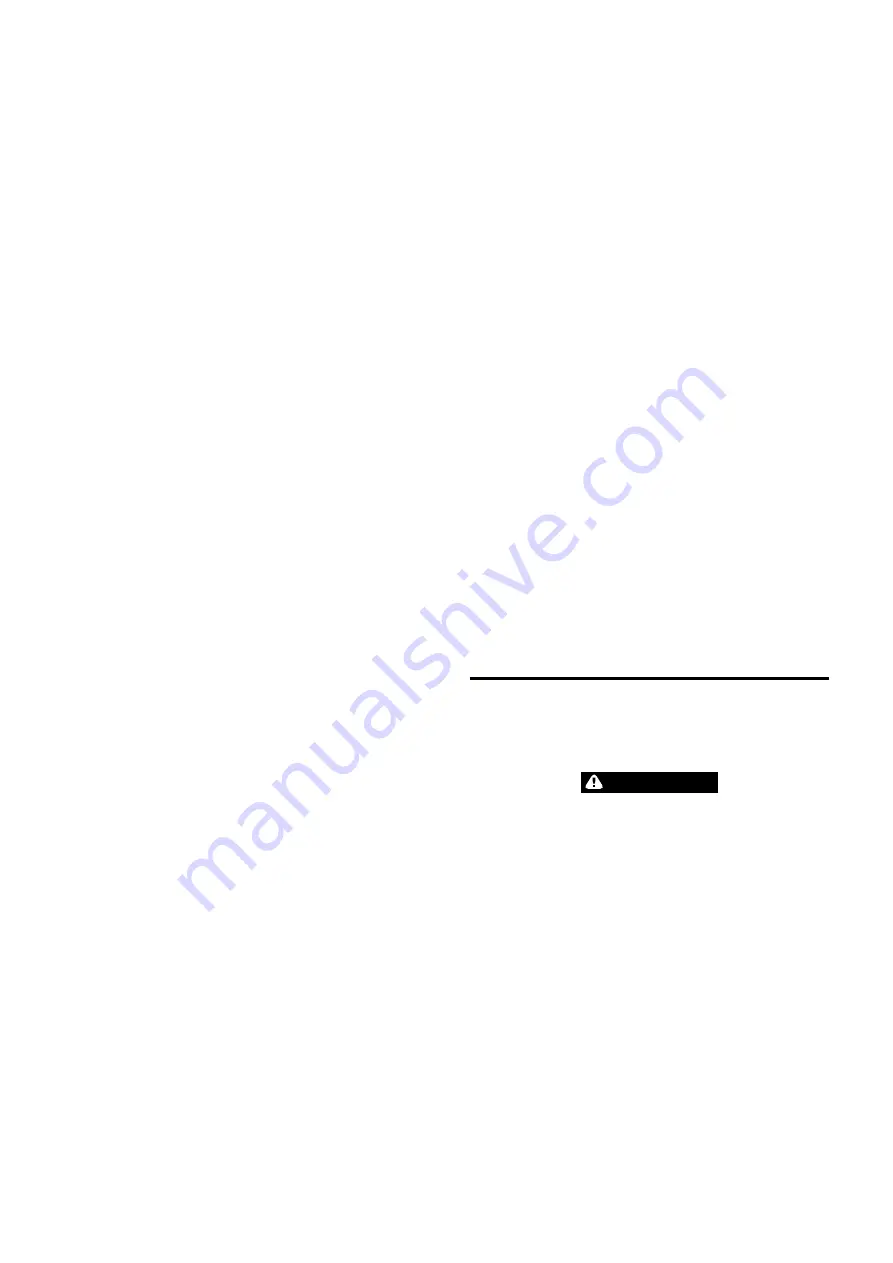
14. Remove planet support assembly (341) from ring gear (19).
15. Remove bearing (18) from planetary carrier (17).
16. Tap out planet axles (16) and remove planet gears (13), bearing rings (14), needle
bearings (15) and spacers (12).
n
Powerhead Body Disassembly
1.5 and 3 ton Hoists
Refer to Dwgs. MHP2650 and MHP2657.
1. Ensure reduction gear, disc brake and motor assemblies have been removed.
2. Remove chain limit stop washer (110) from load chain. Remove load chain from
hoist body (36).
3. Remove capscrews (41), nut (42) and pins (43) from hoist body using drift pin
and hammer.
4. Remove chain stripper (31). Pull sprocket assembly (30) from hoist body (36).
5. Remove and discard oil seal (20) and ‘O’ ring (29) from sprocket (30).
6. Remove bearing (8) and (39) from sprocket if necessary.
7. Remove and discard oil seal (37) from sprocket (30).
4 ton and 6 ton Single, 8 ton and 12 ton Double Fall
Refer to Dwgs. MHP3003 and MHP3011.
1. Ensure reduction gear, disc brake and motor assemblies have been removed.
2. Remove chain limit stop washer (110) from chain. Remove load chain from hoist
body (36).
3. Remove pins (43) from hoist body using drift pin and hammer.
4. Remove chain stripper (31). Pull sprocket assembly (30) from hoist body (36).
Remove adapter ring (59) on 6 ton and 12 ton hoists.
5. Remove oil seal (20) and discard.
6. Remove bearings (8) and (39) from sprocket if necessary.
7. Remove ‘O’ rings (6) and (104).
6 ton Quad Fall
Refer to Dwg. MHP2822.
1. Ensure reduction gear, disc brake and motor assemblies have been removed.
2. Remove chain limit stop washer (110) from load chain. Remove capscrew (56),
nut (55) and load chain from hoist body (36).
3. Remove capscrews (41) and lockwashers (44) from chain guide housing (58).
4. Separate hoist body (36) and chain guide housing (58).
5. Remove spacer (33).
6. Remove pins (43) from hoist body using drift pin and hammer.
7. Remove chain stripper (31). Pull sprocket assembly (30) from hoist body (36).
8. Remove bearings (39) and quad ring (29) from sprocket if necessary.
9. Remove pins (43) from hoist body (36) using drift pin and hammer.
10. Remove chain stripper (31). Pull sprocket assembly (50) from chain guide housing
(58).
11. Remove bearings (8) and (39) from sprocket (50) if necessary.
18 ton Triple and 25 ton Quad Fall
Refer to Dwg. MHP3014.
1. Ensure reduction gear, disc brake and motor assemblies have been removed.
2. Remove chain limit stop washer (110) from load chain. Remove load chain from
hoist body (36) and chain guide housing (58).
3. Remove capscrews (98), lockwashers (44), nuts (99) and top hook assembly or
clevis from hoist.
4. Remove capscrews (41) and lockwashers (44) from chain guide housing (58).
5. Separate hoist body (36) and chain guide housing (58).
6. Remove pins (43) from hoist body using drift pin and hammer.
7. Remove chain stripper (31). Pull sprocket assembly (30) from hoist body (36).
8. Remove oil seal (20).
9. Remove bearings (8) from sprocket if necessary.
10. Remove capscrew (41) and lockwasher (44) from chain guide housing.
11. Pull sprocket assembly (50) and adapter (150) from chain guide housing (58).
12. Remove bearings (149) and ‘O’ rings (105) from sprocket (50) if necessary.
13. Remove ‘O’ rings (104).
n
Remote Two Function Pendant Disassembly
Refer to Dwg. MHP3039 or MHP3040.
1. Remove fittings (603) and lifting eye (501).
2. Unscrew plugs (518). Remove springs (46) and balls (47).
3. Tap out pin (502) and remove levers (503).
4. Remove setscrew (173) from pendant handle (514).
5. Remove valve assemblies (165). Remove ’O’ rings (53) and (171) and protectors
(170). Discard ’O’ rings.
6. Remove plug (615) or emergency stop valve (164) from pendant handle.
7. Remove retainer ring (512) and exhaust washer (513).
n
Remote Four Function Pendant Disassembly (optional feature)
Refer to Dwg. MHP3061 without emergency stop or MHP3062 with emergency stop.
1. Remove fittings (603) and lifting eye (501).
2. Unscrew plugs (518). Remove springs (46) and balls (47).
3. Remove capscrews (525) and (527) and washers (526) from attachment (left)
(523). Remove attachment (left) taking care not to damage pin (529). Separate
pin (529), lever (522) and ’O’ rings (528) from attachment (left). Discard ’O’ rings.
4. Repeat step 3 for attachment (right) (524).
5. Tap out pin (502) and remove levers (503).
6. Remove valve assemblies (165). Remove ’O’ rings (53) and (171) and protector
(170) from valve assemblies. Discard ’O’ rings.
7. Remove plug (615) or emergency stop valve (164) from pendant handle (514).
8. Remove retainer ring (512) and exhaust washer (513).
n
Bottom Hook Disassembly
1.5 ton Single Fall
Refer to DWG. MHP2657.
1. Remove retainer wire (111) and ring (112) from hook block (113).
2. Remove pin (114) and load chain from hook block (113).
3. Remove plug (115) and lightly tap hook block to remove balls (117) through
threaded hole.
4. Remove hook (106) from hook block.
3 ton Double Fall
Refer to Dwg. MHP2657.
1. Remove nuts (123), lockwashers (122) and capscrews (56) from half hook blocks.
2. Separate half hook blocks (118) and (121).
3. Remove sprocket (120) and bearings (119).
4. Remove thrust bearing (125) and ring halves (124) from hook (106).
4 and 6 ton Single Fall
Refer to Dwg. MHP3006.
1. Remove nuts (123), lockwashers (122) (6 ton hoist only) and capscrews (56) from
half hook blocks.
2. Separate half hook blocks (118) and (218).
3. Remove load chain, thrust bearing (125), ring halves (124) and hook (106).
8 and 12 ton Double Fall
Refer to Dwg. MHP3006.
1. Remove nuts (123), lockwashers (122) and capscrews (56) from half hook blocks.
2. Separate half hook blocks (118) and (218).
3. Remove sprocket (120) and bearings (119).
4. Remove thrust bearing (125) and ring halves (124) from hook (106).
5. Pull bearings (119) from sprocket (120) and remove ‘O’ rings (129).
18 ton Triple Fall
Refer to Dwg. MHP3018.
1. Remove retainer ring (224) and anchor pin (219).
2. Remove nuts (123), lockwashers (122) and capscrews (133) from half hook blocks.
3. Separate half hook blocks (118) and (218).
4. Remove sprocket (120) and bearings (119).
5. Remove thrust bearing (125) and ring halves (124) from hook (106).
6. Pull bearings (119) from sprocket wheel (120) and remove ‘O’ rings (129).
6 and 25 ton Quad Fall
Refer to Dwgs. MHP2821 and MHP3029.
1. Remove nuts (123), lockwashers (122) and capscrews (133) from half hook blocks.
2. Separate half hook blocks (118) and (218).
3. Remove sprockets (120), bearings (119) and center ring (132).
4. Remove thrust bearing (125) and ring halves (124) from hook (106).
5. Pull bearings (119) from sprockets (120) and remove ‘O’ rings (129) or quad rings
(130) (6 ton hoist only).
n
Rope Control Disassembly
Refer to Dwg. MHP2662.
1. Remove capscrews (316) and washers (75). Separate rope control block (313) from
hoist motor.
2. Remove gasket (302) and discard.
3. Remove nut (314), capscrew (312), ‘O’ rings (70) and spacers (319).
4. Remove lever (317) from rope control block (313). If required remove rings (318),
pull chain (323) and throttle handles (321) from lever.
5. Remove setscrews (309).
6. Remove adjustment screws (311) and nuts (310).
7. Remove valves (315).
8. Remove protectors (170) and ‘O’ rings (53) and (171) from each valve. Discard ‘O’
rings if worn.
9. Remove plugs (304).
10. Remove springs (307) and balls (308).
11. Remove retainer rings (305), springs (306) and balls (47).
n
Cleaning, Inspection and Repair
Use the following procedures to clean, inspect, and repair the components of the
hoist system.
n
Cleaning
CAUTION
• Bearings that are loose, worn or rotate in the housing must be replaced.
Failure to observe this precaution will result in additional component
damage.
Clean all hoist component parts in solvent (except for the brake friction discs). The
use of a stiff bristle brush will facilitate the removal of accumulated dirt and
sediments on the gears and frames. If bushings have been removed it may be
necessary to carefully scrape old Loctite® from the bushing bore. Dry each part using
low pressure, filtered compressed air. Clean the brake friction discs using a wire brush
or emery cloth. Do not wash the brake friction discs in liquid. If the brake friction
discs are oil soaked, they must be replaced.
n
Inspection
All disassembled parts should be inspected to determine their fitness for continued
use. Pay particular attention to the following:
1. Inspect all gears for worn, cracked, or broken teeth.
2. Inspect all bushings for wear, scoring, or galling.
3. Inspect all bearings for play, distorted races, pitting and roller or ball wear or
damage. Inspect bearings for freedom of rotation. Replace bearings if rotation is
rough or bearings are excessively worn.
4. Inspect shafts for ridges caused by wear. If ridges caused by wear are apparent
on shafts, replace the shaft. Inspect all surfaces on which oil seal lips seat. These
surfaces must be very smooth to prevent damage to the seal lip.
5. Inspect all threaded items and replace those having damaged threads.
6. Inspect the brake drive plates and friction discs for oil. If the friction discs have
become oil-soaked, replace them. If the drive plates have become glazed, sand
them lightly using fine emery cloth and a flat surface as backing. Inspect the
remaining brake parts for warpage or other damage, and replace damaged parts
as necessary.
7. Measure the thickness of the brake friction disc. The brake friction disc must show
an even wear pattern. If the brake friction disc is 0.047 in (1.2 mm) or less,
replace discs.
Form MHD56279 Edition 4
11