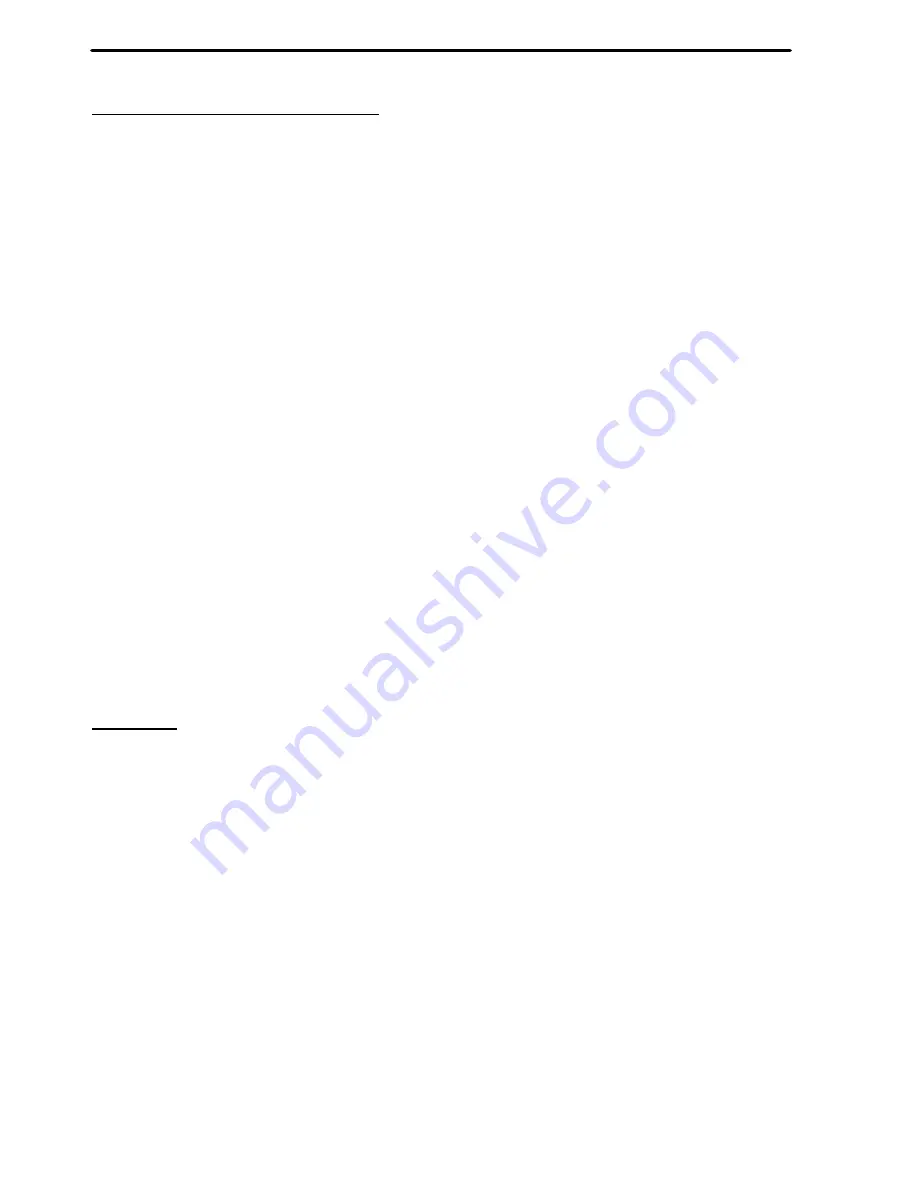
Book 35392877 (1/01)
35
( )
COMPRESSOR OIL COOLER
The compressor lubricating and cooling oil is cooled by
means of the fin and tube--type oil cooler. The
lubricating and cooling oil, flowing internally through
the core section, is cooled by the air stream from the
cooling fan flowing past the core section. When
grease, oil and dirt accumulate on the exterior
surfaces of the oil cooler, its efficiency is impaired.
Each month it is recommended that the oil cooler be
cleaned by directing compressed air which contains a
nonflammable, non--caustic safety solvent through
the core of the oil cooler. This should remove the
accumulation of grease, oil and dirt from the exterior
surfaces of the oil cooler core so that the entire cooling
area can transmit the heat of the lubricating and
cooling oil to the air stream.
In the event foreign deposits, such as sludge and
lacquer, accumulate in the oil cooler to the extent that
its cooling efficiency is impaired, a resulting high
discharge air temperature is likely to occur, causing
shut down of the unit. To correct this situation it will be
necessary to clean it using a cleaning compound in
accordance
with
the
manufacturer’s
recommendations.
HOSES
Each month it is recommended that all of the intake
lines to and from the air cleaners, the engine cooling
system hoses and all of the flexible hoses used for air,
oil, and fuel be inspected.
To ensure freedom from air leaks, all rubber hose
joints and the screw--type hose clamps must be
absolutely tight.
Regular inspection of these
connections for wear or deterioration is necessary.
Premature wear of both the engine and compressor is
ASSURED whenever dust--laden air is permitted to
enter the engine’s combustion chamber or the
compressor intake.
The flexible hoses used in the fuel, oil and air lines on
these units are primarily used for their ability to
accommodate
relative
movement
between
components. It is important they be periodically
inspected for wear and deterioration.
It is also
important the operator does not use the hoses as
convenient hand hold or steps. Such use can cause
early cover wear and hose failure.
NOTICE
Piping systems operating at less than 150 psi
(1050 kPa) may use a special nylon tubing. The
associated fittings are also of a special “push--in”
design. If so, features are as follows:
Pulling on the tubing will cause the inner sleeve to
withdraw and compress, thus tightening the
connection. The tubing can be withdrawn only while
holding the sleeve against the fitting. The tubing can
be removed and replaced numerous times without
losing its sealing ability.
To install the nylon tubing, make a mark (with tape or
grease pencil) approximately 7/8 inch from the end of
the tubing. Insert the tubing into the sleeve and
“push--in” past the first resistance to the bottom. The
mark should be approximately 1/16 inch from the
sleeve, for the 3/8 inch O.D. tubing; 1/8 inch for the
0.25 inch O.D. tubing. This will ensure that the tubing
is fully engaged in the sealing mechanism.
NOTICE
The oil filter must be replaced every 500 hours of
operation or three (3) months, whichever comes
first. On new or overhauled units, replace the ele-
ment after the first 50 and 150 hours of operation;
thereafter, service the oil filter every 500 hours.
To service the oil filters it will first be necessary to shut
the unit down. Wipe off any external dirt and oil from
the exterior of the filter to minimize any contamination
from entering the lubrication system. Proceed as
follows: