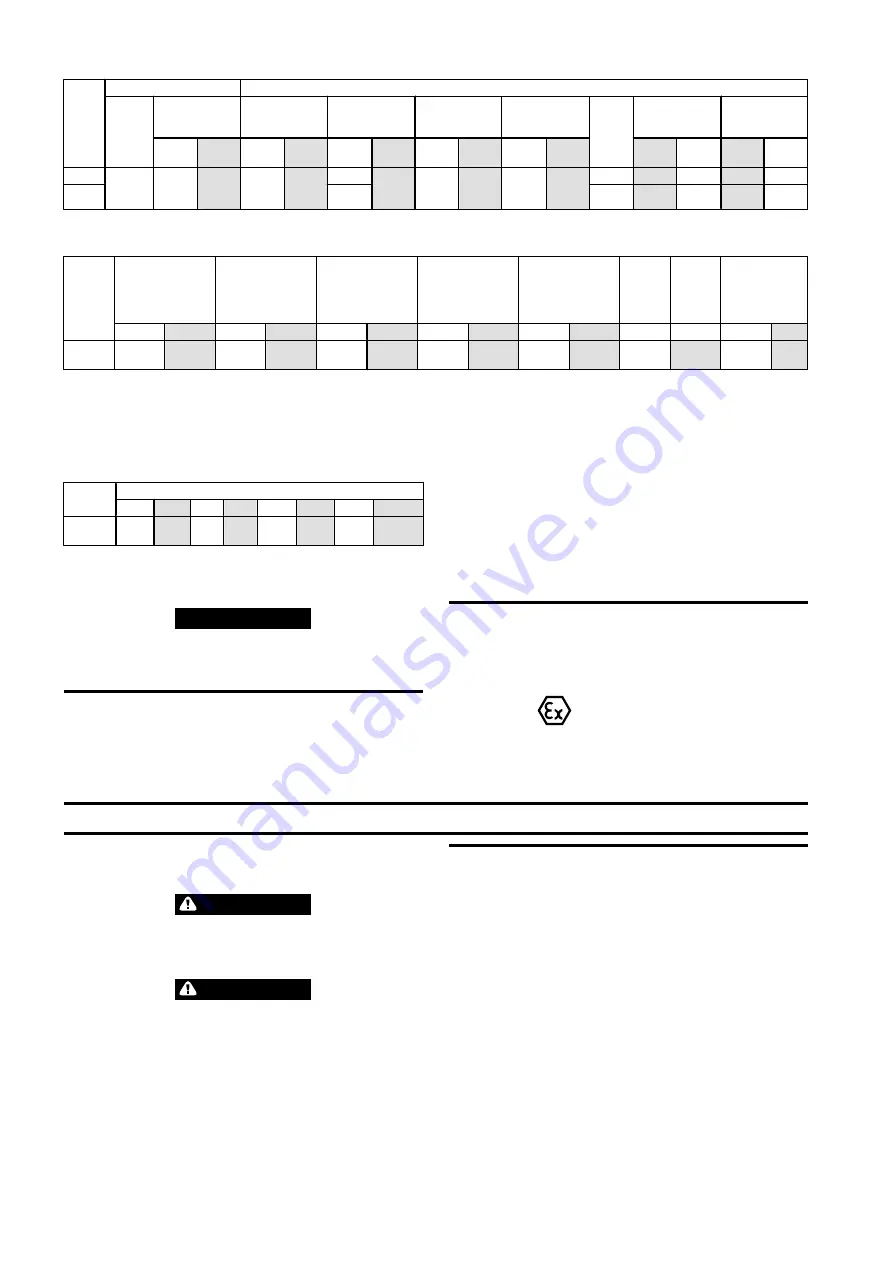
Table 2: Specifications
Models
Air System
Rated Performance (at rated pressure/volume)
Rated
Operatin
g
Pressure
Air Consumption
(at rated pressure
and load)
Full Drum
Line Pull
Full Drum
Line Speed
Mid Drum
Line Speed
Max Stall Pull
1st Layer
Force
Limit
Factor
Maximum
Freeboard
Net
Weight **
scfm
cu.m/
min
lbs
kgs
fpm
m/min
fpm
m/min
lbs
kgs
inch
mm
lbs
kgs
FA2i
90 psig
(630 kPa/
6.3 bar)
335
10
4,400
2,000
51
16
55
17
10,000
4,536
N/A
0.5
13
850
386
FA2i-CE
53
1.6
1
26
925
420
** Weight of standard winch without wire rope.
Table 3: Specifications
Models
Air Motor Pipe
Inlet Size
Minimum Air System
Hose Size (inside
diameter)
Drum
Barrel
Diameter
Drum Flange
Diameter
Recommended Wire
Rope Size (standard)
Sound
Pressure
Level
Sound
Power
Level
Maximum
Foundation
Anchor Shear
Force at One
Capscrew
inch
mm
inch
mm
inch
mm
inch
mm
inch
mm
dBA
dBA
lbs
N
FA2i &
FA2i-CE
1.0
25
1.25
32
10.75
273
19
483
1/2
13
87
99
1,825
9,120
Sound measurements have been made in accordance with ISO 11201, ISO 3744-3746
and ISO 4871 test specifications for sound from pneumatic equipment. Readings
shown are based on the average noise level of each winch configuration,
proportionate to the utilized time in a regular cycle.
Lpc (Peak Sound Pressure) does not exceed 130 dB. Performance based on 90 psig
(6.3 bar/630 kPa) operating pressure.
Table 4: Available Drum Lengths
Models
Drum Lengths
in
mm
in
mm
in
mm
in
mm
FA2i &
FA2i-CE
12
305
16
406
20
508
24 *
610 *
* Standard Length
Refer to sales literature for winch drum wire rope storage capacities.
NOTICE
•
All -E winch models are manufactured to previous European Machinery
directives. Refer to Data (Name) Plate on winch to determine model. If winch
is a custom build also refer to the Declaration of Conformity for serial
number break.
n
Traceability
Load bearing parts are documented to provide traceability. Documentation includes
chemical and physical properties of raw material, heat treating, hardening, tensile
and charpy tests as required for the part.
Units with M1, M2 or M3 in the model code have traceable load bearing
components.
M1 – Material Traceability certificates according to EN 10204 (Ex DIN 50049) 2.2 on
load bearing parts. Conformity documents affirm (by the manufacturer) that parts
are in compliance with requirements of the order, based on non-specific inspection
and testing (i.e. results are typical material properties for these parts).
M2 – Material Traceability certificates according to EN 10204 (Ex DIN 50049) 3.1b on
load bearing parts. Conformity documents affirm (by a department independent of
the manufacturing department) that actual parts are in compliance with
requirements of the order, based on specific inspection and testing (i.e. results are
actual material properties for these parts).
M3 – Material Traceability certificates according to EN 10204 (Ex DIN 50049) 3.1b on
load bearing parts. Conformity documents affirm (by a department independent of
the manufacturing department) that the actual parts used in the product are in
compliance with the order, based on specific inspection and testing (i.e. results are
actual material properties for these parts in a finished, as delivered condition).
Components with part numbers ending in CH are charpy parts for use under extreme
cold conditions. Traceability requirements must be stated when reordering these
parts for continued certification.
n
ATEX
Refer to labeling on product, located near or on data (name) plate, for specific ATEX
designation. Product not marked as such, are not suitable for use in any potentially
explosive atmosphere (ATEX). Refer to Product Safety and Maintenance Information
Manuals for further explanation.
II 2 GD c IIB 200°C X
(Dwg. MHP2584)
INSTALLATION
Prior to installing the product, carefully inspect it for possible shipping damage.
Products are supplied fully lubricated from the factory. Check oil levels and adjust
as necessary before operating product. Refer to “LUBRICATION” section
on page 8 for recommended oils and lubrication intervals.
WARNING
•
Product not installed properly may fall or cause a load to fall resulting in
sever injury or death. Before installation and operation of this product refer
to Product Safety Information manual and all safety warnings pertaining
to this product.
CAUTION
•
Always install, operate, inspect, and maintain this product in accordance
with all applicable standards and regulations (state, country, and federal,
etc.). For example In the USA, the applicable standards are American
Society of Mechanical Engineers (ASME) and National Fire Protection
Agency (NFPA).
n
Mounting
Care must be taken when moving, positioning or mounting the winch. In most cases,
lifting lugs have been provided to assist in handling the winch. If lug locations are
improper for your specific installation, great care should be taken to ensure that
winch, when lifted, will be properly balanced. Determine weight of your winch by
referring to “SPECIFICATIONS” section on page 3. Add weight of wire rope and other
installed options as necessary. Lift winch 3 to 4 inches (75 to 100 mm) off ground.
Verify winch is balanced and secure before continuing lift. Mount winch so axis of
drum is horizontal and that motor vent cap is not more than 15° off top vertical
center. If winch is to be mounted in an inverted position, motor case must be rotated
to position vent cap to the top.
1. The winch mounting surface must be flat and of sufficient strength to handle
rated load plus weight of winch and attached equipment. An inadequate
foundation may cause distortion or twisting of winch uprights and siderails
resulting in winch damage.
2. Make sure mounting surface is flat to within 0.005 inch (0.127 mm) per inch of
drum length. Shim if necessary. Refer to Table 5 ‘Mounting Surface Tolerance’
3. Mounting bolts must be Grade 8 or better. Use self-locking nuts or nuts with
lockwashers. Refer to Table 6 ‘Mounting Bolts’ on page 5.
4. Tighten mounting bolts evenly and torque to specification in torque chart. Refer
to ‘TORQUE CHART’ in Product Maintenance Manual.
5. Maintain a fleet angle between sheave and winch of no more than 1-1/2°. The
lead sheave must be on a center line with drum and, for every inch (25 mm) of
drum length, be at least 1.6 feet (0.5 metre) from the drum. Refer to Product
Safety Information Manual.
4
Form MHD56436 Edition 7