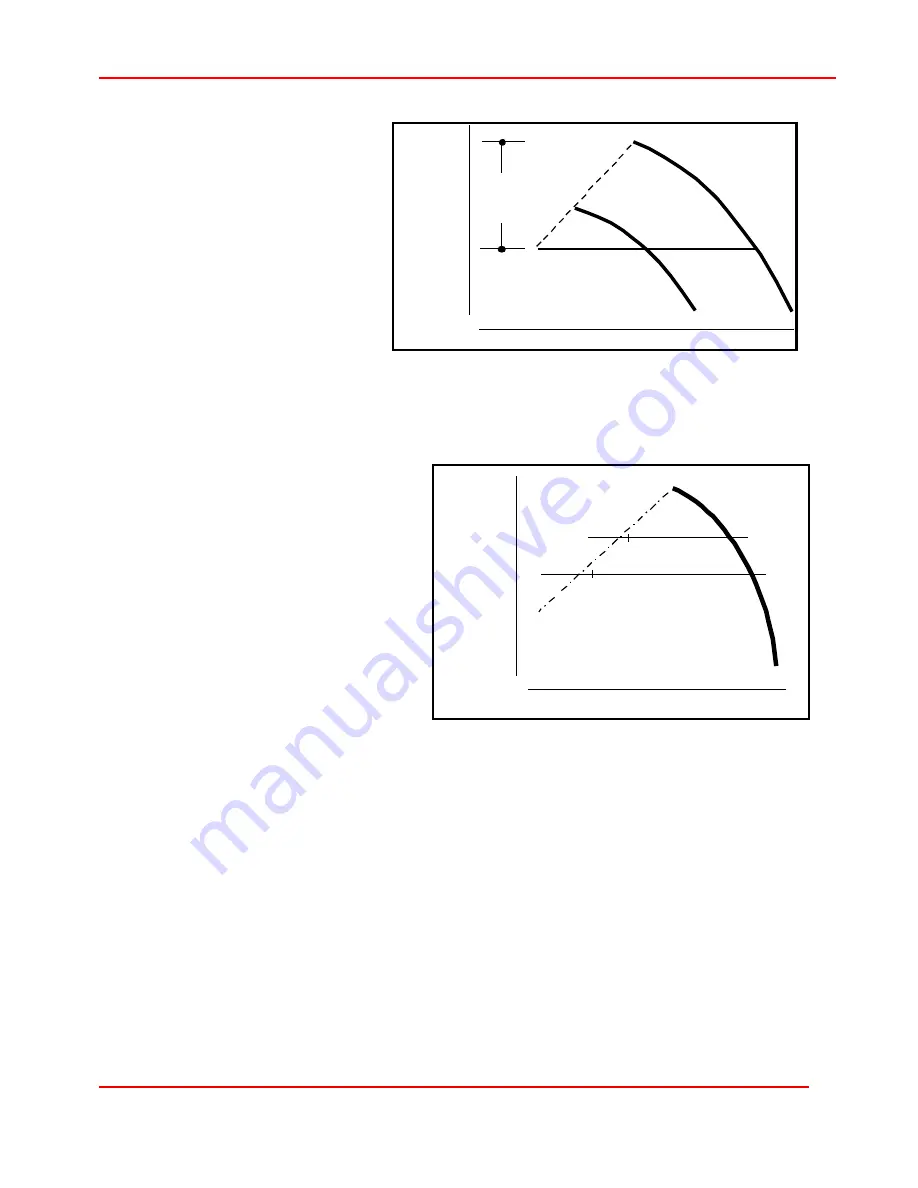
CMC TECHNICAL REFERENCE MANUAL
1X36003 Version 2.52
1996-1999 Ingersoll-Rand Company
Date of Issue: 18-Oct-1999
11
Typically sufficient rise to surge
exists when a ten- percent rise
to surge can be achieved for the
hottest ambients that are
expected for the site. If this
design criterion is followed, the
control system should be able
to prevent surge for variations in
air demand and inlet
temperature. The same design
methodology applies for
changes in cooling water
temperature for multi-stage
compressors.
Changes in System Discharge Pressure
MinLoad
corresponds to a specific
constant discharge pressure;
therefore, if the discharge pressure
changes,
MinLoad
must be reset to
properly control surge. As shown in
Figure 9, when the discharge
pressure is changed from point 1 to
2, a surge can occur at point 2 if
MinLoad
is not reset.
Changes in system discharge
pressure also apply, but more subtly,
when the compressor begins to age.
Dirty inlet filter elements and fouled
coolers can change the
compressor's natural curve; so
MinLoad
should be checked
periodically to prevent surge from an
incorrect setting.
Rapid System Demand Changes
When the system demand varies rapidly over a wide range of capacity, the controller may
not react fast enough to open the bypass valve to prevent surge. The CMC reads discharge
pressure, motor amps, and approximately twenty other pressure and temperature inputs;
plus controls the inlet and bypass valve position. The time required to do all of this
approximately 100 milliseconds. When the controller is too slow to react, it is referred to as
"driving through
MinLoad
". The only prevention for a situation like this is to set
MinLoad
at a
more conservative value. The only negative implication to this is reduced energy savings,
because the bypass valve is opened early.
Incorrect Instrumentation Output
If the instrumentation, defined in Figure 4, is improperly calibrated or gives inaccurate
readings, the compressor could surge even though the CMC thinks it should not. Areas of
Capacity
Discharge
Pressure
Rise
To
Surge
T=cold
T=hot
Figure 8: Rise To Surge
Capacity - Mass Flow
Discharge
Pressure
TL
1
TL
2
Figure 9: Changes in Discharge Pressure