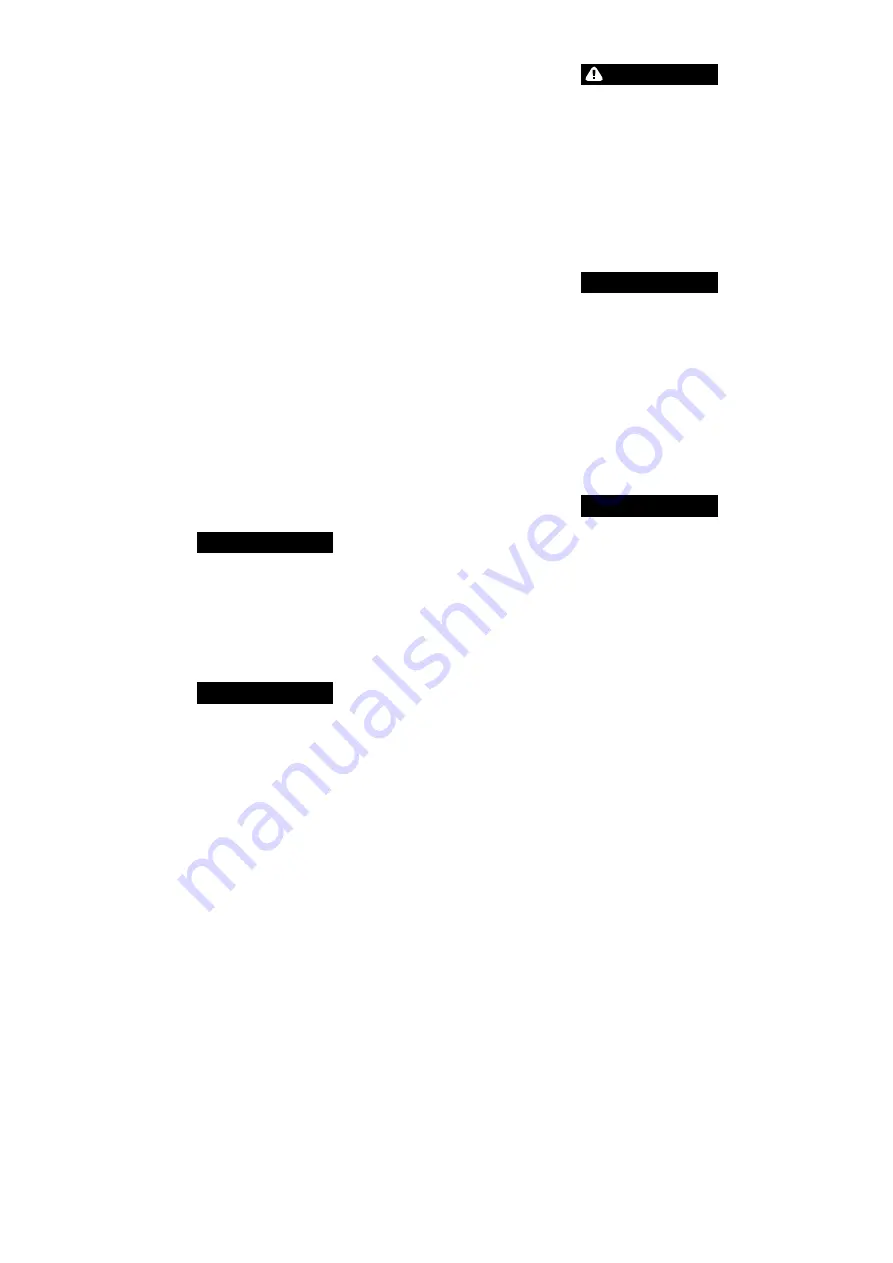
16. Insert rotary valve into rotary valve bushing. The raised tang on rotary valve
should be pointing toward the inlet bushing.
17. Lubricate the inside and outside of crank pin sleeve (36) and place on rotary valve
tang, all the way to the left.
18. Slide crank pin sleeve to the right, until it falls onto the rotary valve tang.
19. Lubricate bushing (37) and place bushing over crank pin sleeve.
20. Place one connecting rod ring (38) over bushing.
21. Place feet of four connecting rods (39) into the space between bushing and ring.
22. Place second connecting rod ring over the connecting rod ends, beveled face
first. Apply oil to this assembly.
23. Insert crankshaft assembly into crank pin sleeve. Ensure that the slot in crankshaft
end and tang on rotary valve are aligned.
24. When crankshaft is seated, move assembly to the left. There should be a slight
drop as assembly seats onto the rotary valve.
25. Install piston rings (16) into grooves in pistons (17). Ensure that the piston ring
face marked with a dot is toward the top (closed) end of the piston (17). Do not
expand piston rings more than is necessary to slip rings over pistons. Expand
and slide the Ingersoll Rand ring tool D01-933 over piston ring on piston. Ensure
upper and lower piston ring ends are offset from each other.
26. Insert a wrist pin (18) partially into piston.
27. Place this assembly onto the connecting rod and push wrist pin fully into piston.
28. Place cylinder gasket (24) onto cylinder sleeve (19).
29. Using fingers, compress top piston ring and press the cylinder sleeve down over
the piston. Sleeve will push Ingersoll Rand ring tool D01-933 off piston. Remove
ring tool.
30. Place a copper washer (22) on capscrew (21). Ensure that the flat side of copper
washer faces cylinder head.
31. Align gasket and motor case capscrew holes. Insert capscrew and washer
through cylinder head (23) and loosely secure it to motor case. Repeat for the
other three capscrews.
32. Holding motor case still, rotate crankshaft 90˚. This will bring the next connecting
rod to its highest position.
33. Repeat steps 25 to 32 above for the other three pistons.
34. Snug up the four capscrews. DO NOT final tighten.
35. Snug up the capscrews on opposite cylinder head.
36. Repeat this procedure for the other two cylinder heads.
37. Repeat these steps until ALL cylinder heads are final tightened. Hold the
crankshaft FIRMLY and in a vertical position. Spin the motor case 4 to 8 complete
revolutions. Assembly should rotate freely without any signs of binding or
knocking.
38. Apply a thin coat of grease to gasket surface of motor mounting bracket (79).
39. Match hole pattern in gasket (32) and motor mounting bracket. Press gasket into
position.
40. Place motor mounting bracket onto motor case.
NOTICE
•
Ensure that the inlet bushing (20) is pointing to the left and motor mounting
bracket feet and oil drain plug are pointing towards the assembler.
41. Slide motor assembly to the edge of the bench. Insert capscrew (29) through
lockwasher (4) and secure mounting bracket to motor case. DO NOT final tighten.
42. Rotate assembly 180˚ and install one more capscrew and washer.
43. Install motor pinion bearing (63) in counterbored end of drum shaft (62).
44. Place drum shaft (62) onto crankshaft. Lower and align setscrew holes.
45. Insert two setscrews (77), final tighten both setscrews in equal steps to keep
drum shaft centered.
46. Tip assembly over WHILE inserting fingers under the rotary valve (15).
NOTICE
•
Ensure that rotary valve does NOT slide out of rotary bushing. If rotary valve
slides out, motor will have to be disassembled to line up rotary valve and
crankshaft.
47. Lay assembly on its side with motor to the left.
48. Insert capscrew (69) through lockwasher (71). Place capscrew and lockwasher
through base (87) and into motor case. Repeat 3 times. Tighten capscrews. Refer
to ‘Torque Chart’ on page 11 for torque requirements.
49. Tip motor assembly onto its base.
50. Note that an arrow is stamped on the face of the valve chest cover (7) and that
a line is scribed on the shank of the reverse valve (10). Turn reverse valve until
line and arrow are in alignment and slide stem of valve into valve chest cover,
entering square shank in square hole in control arm. Ensure main port in reverse
valve is installed facing down. Apply reverse valve nut (1) to threaded end of
reverse valve.
n
Control Valve Assembly
Refer to Dwg. MHP1207.
1. Insert six capscrews (29) and lockwashers (4) into motor case (28). Hand tighten.
DO NOT final tighten.
2. Attach the vent cap assembly (25) to one of the left side capscrews on motor
housing and finally tighten all capscrews. Refer to ‘Torque Chart’ on page 11
for torque requirements.
3. Install and tighten stop pin (6) into valve chest cover (7) if it was removed.
4. Insert thrust washer (13) into valve chest cover.
5. Slide ‘O’ rings (8) and (9) onto reverse valve (10). Lubricate with oil.
6. Insert the reverse valve into valve chest housing. Ensure that ‘O’ ring is not cut
upon installation.
7. Place gasket (102) onto valve chest cover.
8. Insert throttle lever (2) onto outside of reverse valve.
9. Install valve chest cover assembly. Ensuring that throttle lever and main (large)
ports in reverse valve are face UP.
10. Secure valve chest cover with capscrews (5) and lockwashers (4), tighten
capscrews. Refer to ‘Torque Chart’ on page 11 for torque requirements.
Remove throttle lever.
11. Place spring (3) onto throttle lever, on right side of stud.
12. Use bench to hold free end of spring. Then, twist throttle lever so that the stud
goes past the free end of spring.
13. Continue twisting the throttle lever while pushing free end of spring over stud.
CAUTION
•
The spring can SNAP off throttle lever. KEEP the throttle lever pointed away
from your body.
14. Align the square hole in throttle lever with the reverse valve and press onto the
reverse valve.
15. Rotate throttle lever slightly to the left and right to allow spring to ‘pop’ over
stop pin.
16. Use nut (1) to secure throttle lever to reverse valve and final tighten.
17. Check lever rotates freely in both directions and spring returns to neutral when
released.
n
Wire Rope Drum Assembly
Refer to Dwg. MHP1207.
1. Install drum bearings (84) in wire rope drum (86).
2. Grease ALL teeth in the drum.
NOTICE
•
Do NOT get any grease on brake band lining.
3. Place drum thrust plate (83) in motor end of wire rope drum until it contacts
shoulder in bore. Install drum grease seal (82), lip side first, in motor end of wire
rope drum. Start seal in bore squarely and drive into position using a large, flat-
faced arbor that will not damage seal.
4. After making sure that there are no nicks or burrs on the hub surface of motor
mounting bracket (79) on which grease seal revolves; apply a thin coat of grease
to this surface. Place a small quantity of light grease in each needle bearing and
slide drum onto drum shaft.
5. Place brake band assembly (61) in position making sure that lug on brake band
assembly enters the space between brake anchor (91) and pad on base. Install
cotter pins (92) and bend ends apart. Ensure both cotter pin heads are facing
the same direction.
6. Insert one end into base above the tab on brake band assembly with the cotter
pin heads facing out. Place the shorter end (distance of cotter pin to the edge
of the brake anchor) in first.
7. Press the drum seal (65) into the groove in the gear case (66).
NOTICE
•
Ensure that the staples are facing the side of the groove. The metal staples
should not rub on the drum.
8. Place the gear case onto the drum.
9. Secure the gear case to the base with four capscrews (69) and lockwashers (71)
and tighten. Refer to ‘Torque Chart’ on page 11 for torque requirements.
n
Gear Case Assembly
Refer to Dwg. MHP1207.
1. Press inner bearing (96) onto drive shaft (93) then seat the assembly in gear case
(66) and stake bearing.
2. Install bearing (72) into bore in gear case and stake.
3. Press bearing (72) onto the larger gear side of intermediate gear (70).
4. Slide drive gear (99), jaw side outward, onto drive shaft and against bearing.
5. Place a washer (97) over the drive shaft and secure with a retainer ring (98).
6. Install intermediate gear assembly in gear case. Carefully mesh gear teeth with
drive gear (99) and crank assembly.
7. Insert one ball (95) into drive shaft cross hole followed by spring (94).
8. Insert the second ball (95). Use grease to keep ball in position.
9. Slide clutch jaw (101), jaw side first, onto the drive shaft.
10. Press ball down and push clutch jaw into drive gear. Ensure jaws are fully meshed.
11. Place the third bearing (72) onto drive shaft and carefully tap with a hammer
until seated.
12. Pull the clutch jaw OUT until the detent ball is engaged. Drive gear will spin freely.
13. Grease both bearing pockets in the gear case cover (76).
14. Apply a thin coat of grease to the gasket surface of the gear case.
15. Align the holes in gasket (74) and press into grease.
16. Install gear case cover (76) by aligning the capscrew holes and pin. Push gear
case cover onto gear case.
17. Carefully tap gear case cover with a hammer until seated.
18. Secure gear case cover with capscrews (5) and lockwashers (4). Tighten
capscrews. Refer to ‘Torque Chart’ on page 11 for torque requirements.
19. Insert the clutch handle assembly into the gear case cover, aligning the setscrew
(77) hole in bushing with one in gear case cover.
20. Install a setscrew (77) and tighten.
21. Add grease to gear case housing as outlined in the Product Information Manual
“LUBRICATION” section.
22. Install plugs (75) and tighten.
n
Brake Band Assembly
Refer to Dwg. MHP1207.
1. Screw the brake trunnion (56) onto the brake adjusting screw (57) until 3 or 4
threads are exposed.
2. Insert the eye end of the brake screw between the loops on brake band (61).
Ensure that the round part of the brake screw is facing up.
3. Insert the brake band pin (59) through the slot in the brake band loops and
adjusting screw eye.
4. Insert retainer ring (58) into the groove in the brake band pin. Press the retainer
ring until fully seated. Ensure that the flat side of the retainer is against the brake
screw. Pin must be centered in brake band. If pin is not centered move retainer
ring to other side of the brake adjusting screw.
5. Insert the stud on the brake lever (55) half into the brake band bracket. Ensure
that the lever extends past the right side of the winch.
6. Insert the brake trunnion with adjusting screw into the hole in the lever half.
7. Place the remaining lever half on the brake trunnion and brake band bracket.
Squeeze handle halves together.
8. Install brake lever screws (50) and tighten. Refer to ‘Torque Chart’ on page 11
for torque requirements.
Form MHD56461 Edition 2
9