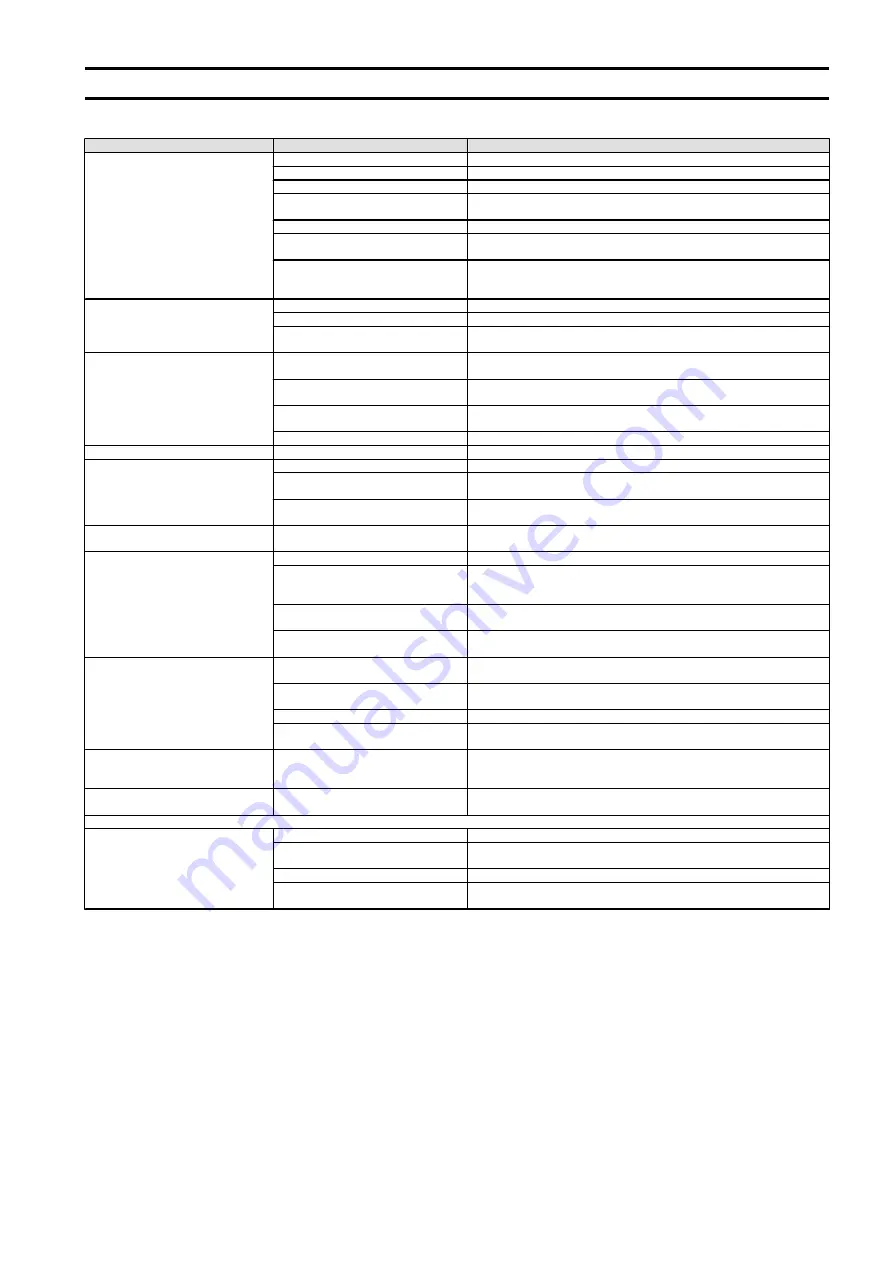
TROUBLESHOOTING
This section provides basic troubleshooting information. Determination of specific causes to problems are best identified by thorough inspections performed by personnel
instructed in safety, operation and maintenance of this equipment. The chart below provides a brief guide to common winch symptoms, probable causes and remedies.
SYMPTOM
CAUSE
REMEDY
Winch will not operate.
Insufficient or no air supply to winch.
Check air supply line connections and hoses.
Winch is overloaded.
Reduce load to within rated capacity.
Shipping plugs may still be in place.
Remove shipping plugs in valve and motor exhaust ports.
Drum brake does not release.
Disengage manual band brake, or refer to
‘Adjusting Automatic Brake’ on page 6.
Motor may be damaged.
Disassemble and clean the motor and replace any broken or damaged parts.
Air leak.
Check hose and fitting connections. Inspect hose(s) for breaks. Tighten fittings and
repair or replace hoses as necessary.
Air lines freeze due to water in air supply.
Install or drain air system moisture traps, moisture collecting air receivers and
compressor aftercoolers. After corrective action has been taken, disconnect lines at
winch inlet and purge with clean, dry air or nitrogen.
Load continues to move when winch is
stopped.
Brake is slipping.
Check ‘Adjusting Automatic Brake’ on page 6 and brake band lining wear.
Winch is overloaded.
Reduce load to within rated capacity.
Winch motor controls sticking.
Check pendant/throttle levers spring return to normal (neutral) position when
released.
Winch does not lift load or does not lift
rated capacity. Winch does not lift/pull
load.
Motor may be damaged.
Remove and disassemble motor as described in “MAINTENANCE” on page 6.
Examine all parts and replace any that are worn or damaged.
Insufficient air supply.
Verify air supply pressure and volume at winch inlet meets the requirements listed
in the “SPECIFICATIONS” section in Product Information Manual. Clean air line filter.
Automatic brake (optional feature) is not
releasing.
Check brake release pilot hole is not restricted. Check seals on cylinder piston are
not damaged. Brake will start to release at 50 psig (3.5 bar/350 kPa).
Winch is overloaded.
Reduce load to within rated capacity.
Oil leak from motor end of winch.
Motor assembly is leaking.
Disassemble winch and inspect motor assembly seals.
Throttle or pendant lever moves but winch
does not operate.
Motor may be damaged.
Disassemble and clean motor and replace any broken or damaged parts.
Insufficient air supply.
Ensure air pressure at winch inlet is at least 90 psig (6.3 bar/630 kPa) at rated volume.
Clean air line filter.
Air leak.
Check hose and fitting connections. Inspect hose(s) for breaks. Tighten fittings and
repair or replace hoses as necessary.
Motor does not run smoothly or makes
excessive noise during operation.
Damaged or broken piston or connecting
rod.
Disassemble and repair motor.
Motor runs hot or makes excessive noise
during operation.
Low oil level.
Check oil level in motor. Add oil as required to obtain proper level.
Improper lubrication.
Replace oil with type recommended in “LUBRICATION” section in Product
Information Manual. Set lubricator to provide 6 to 9 drops of oil per minute at
maximum winch operating capacity.
Water in oil.
Drain and refill with recommended oil. Operate winch with no load slowly, in both
directions. If noise still exists or motor overheats disassemble and repair motor.
Damaged or broken piston or connecting
rod.
Disassemble and repair motor.
Winch runs slow.
Improper hose or fitting sizes.
Check fittings, connections and hoses for correct size and length. Replace parts that
may cause restricted air flow. Inspect air line filter.
Motor may be damaged.
Remove and disassemble motor as described in “MAINTENANCE” on page 6.
Inspect all parts and replace all worn or damaged parts.
Brake not releasing.
Refer to brakes in “MAINTENANCE” on page 6.
Insufficient air supply.
Verify air supply pressure and volume at winch inlet meets the requirements. Refer
to “SPECIFICATIONS” section in Product Information Manual. Clean air line filter.
Air lines freeze.
Water in air supply.
Install or drain air system moisture traps, moisture collecting air receivers and
compressor aftercoolers. After corrective action has been taken, disconnect lines at
winch inlet and purge with clean, dry air or nitrogen.
Throttle lever hard to actuate, or lever does
not spring return to neutral.
Reverse valve sticking in bushing.
Remove and disassemble control valve. Clean control valve parts and check
clearance between reverse valve and bushing.
Automatic Band Brake:
Brake cylinder will not release.
Band brake out of adjustment.
Adjust band brake to maintain correct cylinder stroke.
Leaking cylinder seals.
If air is noticed escaping from cylinder breather when attempting to release brake,
replace or repair cylinder.
Dirty filter in air supply.
Clean or replace filter.
Faulty dump valve.
Check dump valve exhaust port. Air should exhaust when control valve handle is in
neutral. If no air escapes, replace dump valve.
Form MHD56461 Edition 2
5