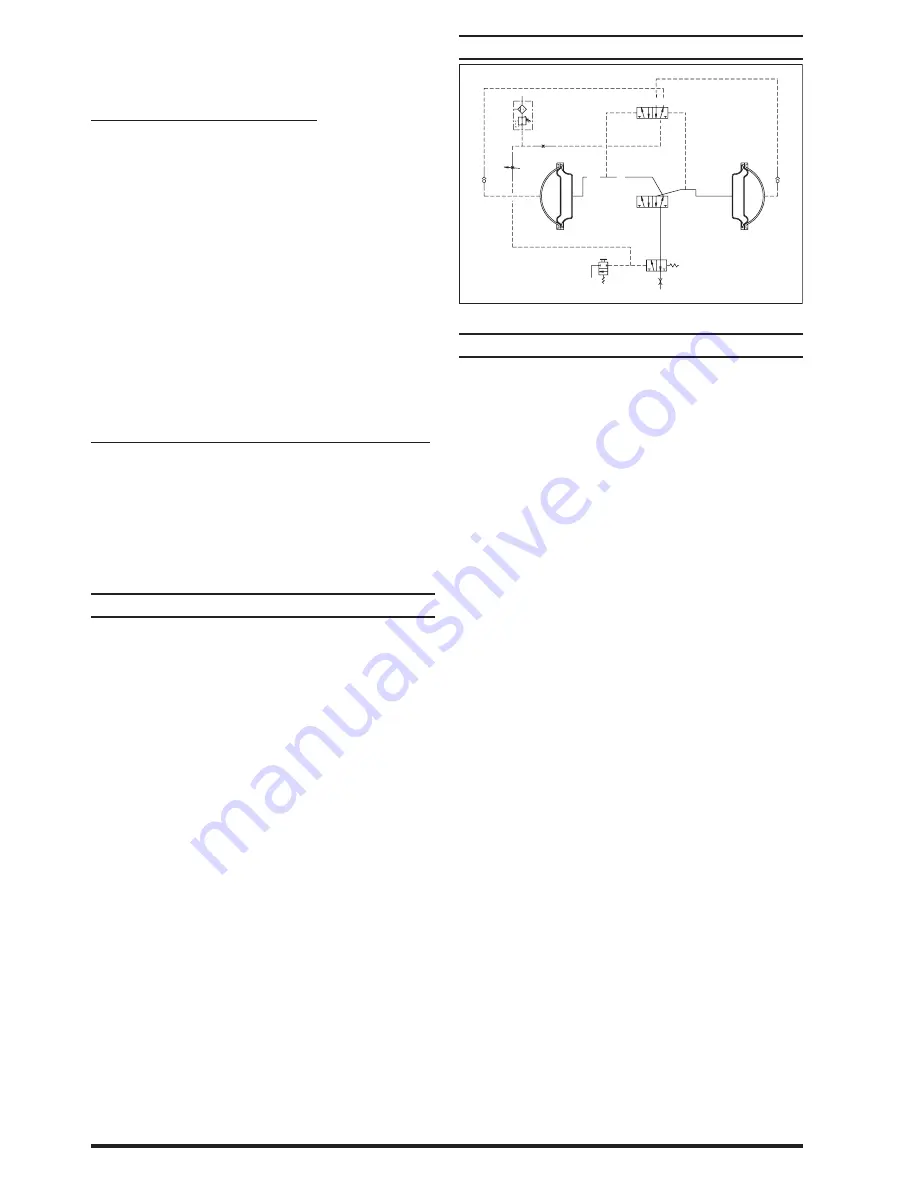
Page 4 of 12
PP20A-XXX-XXX (en)
compress some powders to a solid that may cause the pump
to fail. The pump should cycle until most of the powder has
been purged before it is shut down.
Calibration procedure on initial start-up:
NOTE: Once these parameters are established for your spe-
cifi c application, they should not need to be changed.
Turn the fl ow and pressure on the (248) fi lter / regulator
all the way up.
Slowly decrease pressure and fl ow until pump begins to
labor (work harder).
Increase pressure and flow back to a point where the
pump begins to run smoothly. This will optimize the air-
to-powder mix and will help to establish the most effi-
cient working parameters.
If the pump should begin to cycle slowly (bog down), the
powder can be purged by depressing restart button. This will
stop the pump and restart the aeration cycle and allow time
to increase air fl ow to the aeration ports for proper material
movement.
IMPORTANT
SHUT DOWN PROCEDURE - TO HELP PREVENT PACK-OUT
It is good operating practice to dry cycle the pump 5 - 10
seconds at the end of each dispense cycle. This can be ac-
complished by closing off the powder source at the suction
of the pump or pull wand from material. This will help clear
the pump chambers of any residual powder.
NOTICE: Failure to insure proper fl uidization can result in
internal parts breakage and pump failure.
MAINTENANCE
Refer to the part views and descriptions as provided on page
6 through 11 for parts identifi cation and Service Kit informa-
tion.
Keep good records of service activity and include pump
in preventive maintenance program.
Certain ARO “Smart Parts” are indicated which should be
available for fast repair and reduction of down time.
Service kits are divided to service two separate dia-
phragm pump functions: 1. AIR SECTION, 2. FLUID SEC-
TION. The FLUID SECTION is divided further to match
typical part MATERIAL OPTIONS.
Provide a clean work surface to protect sensitive internal
moving parts from contamination from dirt and foreign
matter during service disassembly and reassembly.
Before disassembling, empty captured material in the
outlet manifold by turning the pump upside down to
drain material from the pump.
1.
2.
3.
SCHEMATIC CIRCUIT
Figure 2
A212PD
12
14
4 2
Left
2
95077
Air / Nitrogen
Right 4
4
1
2
Exh
24130
1
2
H254PS
94977
3
CP10-B
CP10-B
119309-103
TROUBLE SHOOTING
Product discharged from exhaust outlet.
Check for diaphragm rupture.
Check tightness of (14) diaphragm screw.
Motor blows air or stalls.
Check (176) check valve for damage or wear.
Check for restrictions in valve / exhaust.
Low output volume, erratic fl ow, or no fl ow.
Check air supply.
Check for plugged outlet hose.
Check for kinked (restrictive) outlet material hose.
Check for kinked (restrictive) or collapsed inlet material
hose.
Suction hose must be a non-collapsing type, conductive
and capable of pulling a high vacuum (up to 30” mer-
cury).
Check all joints on the inlet manifolds and suction con-
nections. Connection must be air tight.
Inspect the pump for solid objects lodged in the dia-
phragm chamber or the seat area.
Loctite® and 242® are registered trademarks of Henkel Loctite Corporation ARO® is a registered trademark of Ingersoll-Rand Company
Santoprene® is a registered trademark of Monsanto Company, licensed to Advanced Elastomer Systems, L.P. 271™ is a trademark of Henkel Loctite Corporation
Lubriplate® is a registered trademark of Lubriplate Division (Fiske Brothers Refi ning Company)