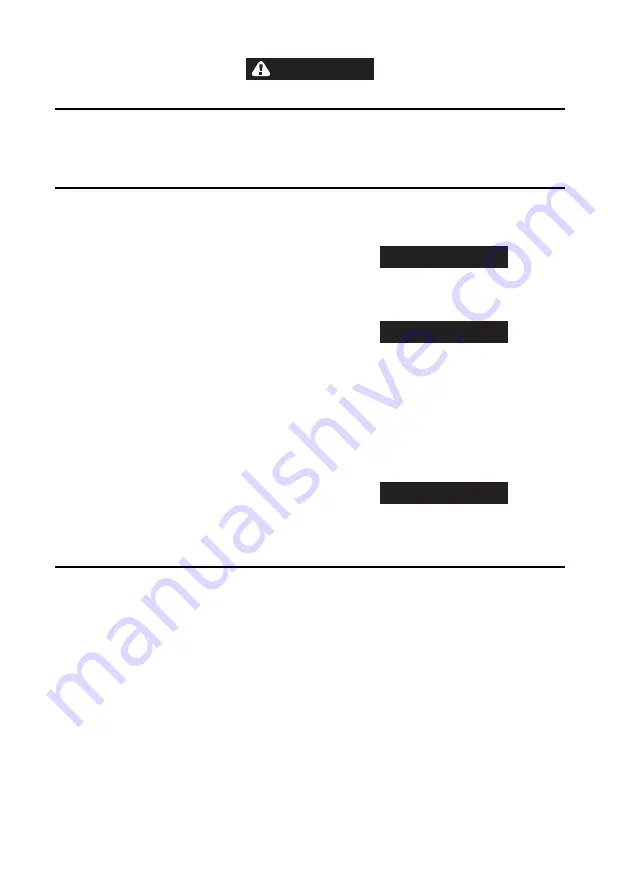
2
Form 04584249-Edition 1
WARNING
Always wear eye protection when operating or performing maintenance on this tool. Always turn off the air supply and disconnect hose before
installing, removing or adjusting any accessory on this tool, or before performing any maintenance on this tool.
Lubrication
Each time a Series 2903P Air Impact Wrench is disassembled for
maintenance, and repair or replacement of parts, lubricate the tools as
follows:
1.
Work approximately 6 to 8 cc of
Ingersoll-Rand
No. 100 Grease into
the impact mechanism. Coat the Anvil (46) or (49) lightly with grease
around the Hammer Case Bushing (41). Inject approximately 1 to 2
cc of grease into the Grease Fitting (23).
2.
Use
Ingersoll-Rand
No.50 Oil for lubricating the motor. Inject
approximately 1 to 2 cc of oil into the air inlet before attaching the air
hose. Remove the Oil Chamber Plug (4) and fill the oil chamber.
Disassembly
General Instructions
1.
Do not disassemble the tool any further than necessary to replace or
repair damaged parts.
2.
Whenever grasping a tool or part in a vise, always use leather-
covered or copper-covered vise jaws to protect the surface of the
part and help prevent distortion. This is particularly true of threaded
members and housings.
3.
Do not remove any part which is a press fit in or on a subassembly
unless the removal of that part is necessary for repairs or
replacement.
4.
Do not disassemble the tool unless you have a complete set of new
gaskets and O-rings for replacement.
Disassembly of the Air Impact Wrench
1.
Clamp the handle of the Air Impact Wrench in a vise with the square
drive upward.
2.
Unscrew and remove the four Hammer Case Cap Screws(45).
3.
While lightly tapping on the end of the Anvil (46 or 49) with a plastic
hammer, lift off the Hammer Case (40).
4.
Grasp the Hammer Frame (36) and carefully lift off the entire impact
mechanism, making certain not to drop the two Hammer Pins (37).
5.
Lift the Rear Hammer Frame Washer (38) and the two Motor Clamp
Washers(35) from the front of the motor.
6.
Grasp the splined end of the Rotor (28) and pull the assembled
motor from the Motor Housing (1).
Disassembly of Impact Mechanism
1.
With the Impact Mechanism on a workbench, driver end up, grasp
the Anvil (46) or (49) and lift it from the mechanism.
2.
Remove the two Hammer Pins (37).
3.
Slide the Hammer (39) from the Hammer Frame (36).
Disassembly of the Motor
1.
Lift the Front End Plate (33) and Front Rotor Bearing (34) from
splined end of Rotor.
2.
Remove Cylinder (30) and Vanes (29).
3.
Remove Rear Rotor Bearing Retainer (25).
4.
Lift the Rear End Plate (27) and Rear Rotor Bearing (26) from Rotor.
Disassembly of the Reverse Valve
NOTICE
The Reverse Valve Screw (22) is installed with a thread locking
compound.
1.
Unscrew the Reverse Valve Knob Screw and remove the Reverse
Valve Knob (21).
NOTICE
Be careful you do not lose the Reverse Valve Detent Ball (19) and
Spring (20) from the hole in the side of the Reverse Valve.
2.
While slowly rotating the Reverse Valve (18), withdraw it from the
Reverse Valve Bushing(16).
Disassembly of the Throttle
1.
Unscrew and remove the Air Inlet (15).
2.
Lift off the Exhaust Deflector (14) and withdraw the Exhaust Silencer
(13).
3.
Remove the Oiler Retaining Ring (12) from inside the handle.
4.
Withdraw the Oiler Body Assembly (9), Throttle Valve Spring (8) and
Throttle Valve (7).
5.
Withdraw Trigger Assembly (2).
NOTICE
Do not remove the Throttle Valve Seat (6) unless you have a new
Throttle Valve Seat on hand for installation.
6.
If the Throttle Valve Seat (6) must be replaced, thread a long 3/8’’
cap screw into it and withdraw it from the handle.
Assembly
General Instructions
1.
Always press on the
inner
ring of a ball–type bearing when installing
the bearing on a shaft.
2.
Always press on the
outer
ring of a ball–type bearing when pressing
the bearing into a bearing recess.
3.
Whenever grasping a tool or part in a vise, always use leather–
covered or copper–covered vise jaws. Take extra care with threaded
parts and housings.
4.
Always clean every part and wipe every part with a thin film of oil
before installation.
5.
Apply a film of O-ring lubricant to all O-ring before final assembly.
Assembly of the Throttle Mechanism
1.
If the Throttle Valve Seat (6) was removed from the handle, install a
new Throttle Valve Seat by pushing it into place with a 1/2’’ (13 mm)
diameter dowel.
2.
Wipe the trigger pin with some light grease and insert the Trigger
Assembly (2) into the trigger bushing.
3.
Insert the Throttle Valve (7), long stem end first, into the bottom of the
handle so the end of the valve stem engages the hole in the Trigger
pin.
4.
Install the Throttle Valve Spring (8), small end first, into the handle of
the Motor Housing Assembly (1).
5.
Make certain the two Oiler Body Seals (11) are positioned in the
annular grooves on the Oiler (9) and install the Oiler counterbored
end first into the handle. The large end of the Throttle Valve Spring
should seat in the counterbore in the Oiler.
6.
Install the Oiler Retaining Ring (12) in the groove in the handle.
7.
Grasp the Exhaust Silencer (13) by the long edge and rolling it into a
tight cylindrical shape, insert the Silencer into the handle flush with
the recess.
8.
Position the Exhaust Deflector (14) on the bottom of the handle and
retain it with the Air Inlet (15). Tighten the Air Inlet to 30 to 50 ft-lb
(40.5 to 47.5 Nm) torque.
Assembly of the Reverse Valve
1.
Make certain the Reverse Valve Bushing Seals (17) are properly
located in undercuts in the Reverse Valve Bushing (16).
2.
Dampen the Reverse Valve (18) with light oil. Install the Reverse
Valve Detent Spring (20) followed by the Reverse Valve Detent Ball
(19) in the Hole in the Reverse Valve. With the Air Impact Wrench in
an upright position, and while facing the handle end of the Air Impact
Wrench, slowly rotate the Reverse Valve and insert it from left to right
in the splined end of the Reverse Valve Bushing.