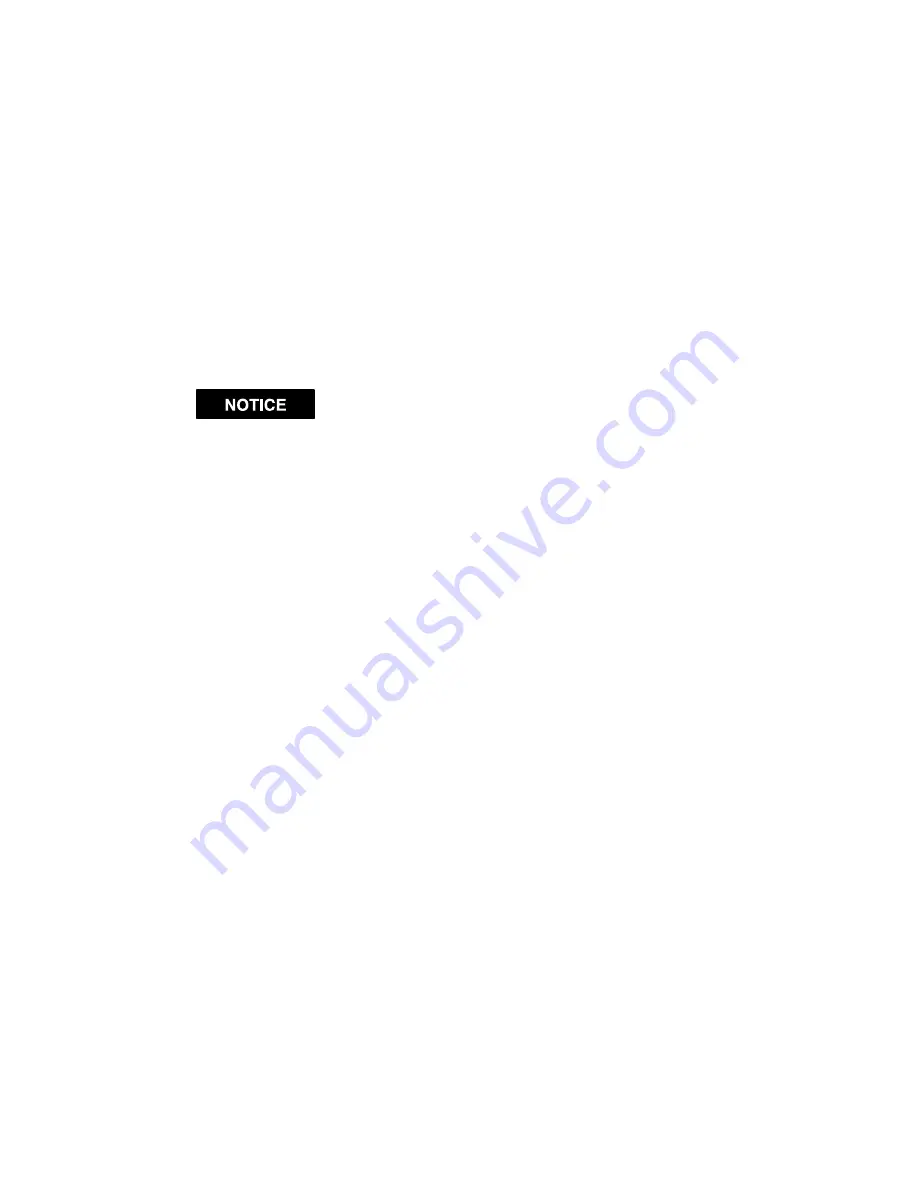
21
MAINTENANCE SECTION
6. Insert the Throttle Valve into the Throttle Valve
Bushing, taking care to line up the retaining pin hole
in the Throttle Valve with the elongated hole in the
Bushing. Drive the Throttle Valve Retaining Pin (14)
into the Throttle Valve pin hole.
7. If the Trigger (13) was removed, press it onto the end
of the Throttle Valve.
8. Install the Throttle Valve Assembly into the Housing,
taking care to line up the cross hole in the Throttle
Valve Bushing with the retaining pin hole in the
Housing. Drive in the Bushing Retaining Pin (18)
from right to left when facing the rear of the tool.
(Refer to Drawing TPA979–4). Work the Trigger a
few times to assure a good sliding fit.
9. If the Exhaust Silencer (24) was removed, install it in
the housing handle. Make sure the Silencer is rolled
tightly for easy installation.
If you are installing an Exhaust Muffler Kit (20,
21, 22, 23 and 24) for the first time, you must first
remove the Exhaust Deflector Retaining Ring
(3B), the circular Exhaust Deflector (3A), and the
second Exhaust Deflector Retaining Ring.
10. If your tool has a built–in muffler, install the
Deflector Gasket (23) and Exhaust Deflector (22).
11. If using Inlet Bushing (2), install the Exhaust Deflec-
tor (3A) between the two Exhaust Deflector Retain-
ing Rings (3B). Install the Inlet Bushing (2 or 20).
Tighten the Bushing between 20 and 25 ft–lb
(27.1 and 33.9 Nm) torque.
12. If the Nameplate (19) has become disfigured, replace
it after transferring the proper serial number,
Assembly of the Motor for 1702SB1
1. Install a new End Plate Gasket (31) into the motor
bore of the Motor Housing (1), making sure the holes
in the Gasket align with those in the bottom of the
Housing.
2. Slide the Rear End Plate (30) onto the short hub of
the Rotor (22), with the bearing recess trailing.
3. Slide the Rear Rotor Bearing (24) onto the short hub
of the Rotor against the Rear End Plate.
4. Install the Rear Rotor Bearing Retainer (25).
5. With the splined end of the Rotor upright, place the
Cylinder (26), pocket end first, over the Rotor with
the dowel hole and ports aligned with the holes in the
Rear End Plate.
6. Apply a light film of oil to the Vanes (28) and insert
them into the vane slots in the Rotor.
7. If the Front Rotor Bearing (23) was removed, press a
new Bearing into the recess of the Front End
Plate (29).
8. Slide the assembled Front End Plate over the splined
hub of the Rotor, Bearing trailing, with the dowel
hole and ports of the Front End Plate aligning with
like holes in the Cylinder and Rear End Plate.
9. Insert a rod approximately 6” (150 mm) long and
1/8” (3.2 mm) in diameter through the aligned dowel
holes in the two End Plates and Cylinder. Use the rod
as a guide to insert the motor into the Motor Housing
with the dowel hole and ports of the motor and End
Plate Gasket aligned.
10. Grasp the Motor Housing in a vise, motor upward.
Withdraw the rod and replace it with the Cylinder
Dowel (27).
Assembly of the Motor for 1702P1
1. Install a new End Plate Gasket (25) into the motor
bore of the Motor Housing (1), making sure the holes
in the Gasket align with those in the bottom of the
Housing.
2. Slide the Rear End Plate onto the short hub of the
Rotor (29), with the bearing recess trailing.
3. Slide the Rear Rotor Bearing (27) onto the short hub
of the Rotor against the Rear End Plate.
4. Install the Rear Rotor Bearing Retainer (26).
5. With the splined end of the Rotor upright, place the
Cylinder (31), pocket end first, over the Rotor with
the dowel hole and ports aligned with the holes in the
Rear End Plate.
6. Apply a light film of oil to the Vanes (30) and insert
them into the vane slots in the Rotor.
7. If the Front Rotor Bearing (34) was removed, press a
new Bearing into the recess of the Front End Plate
(33).
8. Slide the assembled Front End Plate over the splined
hub of the Rotor, Bearing trailing, with the dowel
hole and ports of the Front End Plate aligning with
like holes in the Cylinder and Rear End Plate.
9. Insert a rod approximately 6” (150 mm) long and
1/8” (3.2 mm) in diameter through the aligned dowel
holes in the two End Plates and Cylinder. Use the rod
as a guide to insert the motor into the Motor Housing
with the dowel hole and ports of the motor and End
Plate Gasket aligned.
10. Grasp the Motor Housing in a vise, motor upward.
Withdraw the rod and replace it with the Cylinder
Dowel (32).