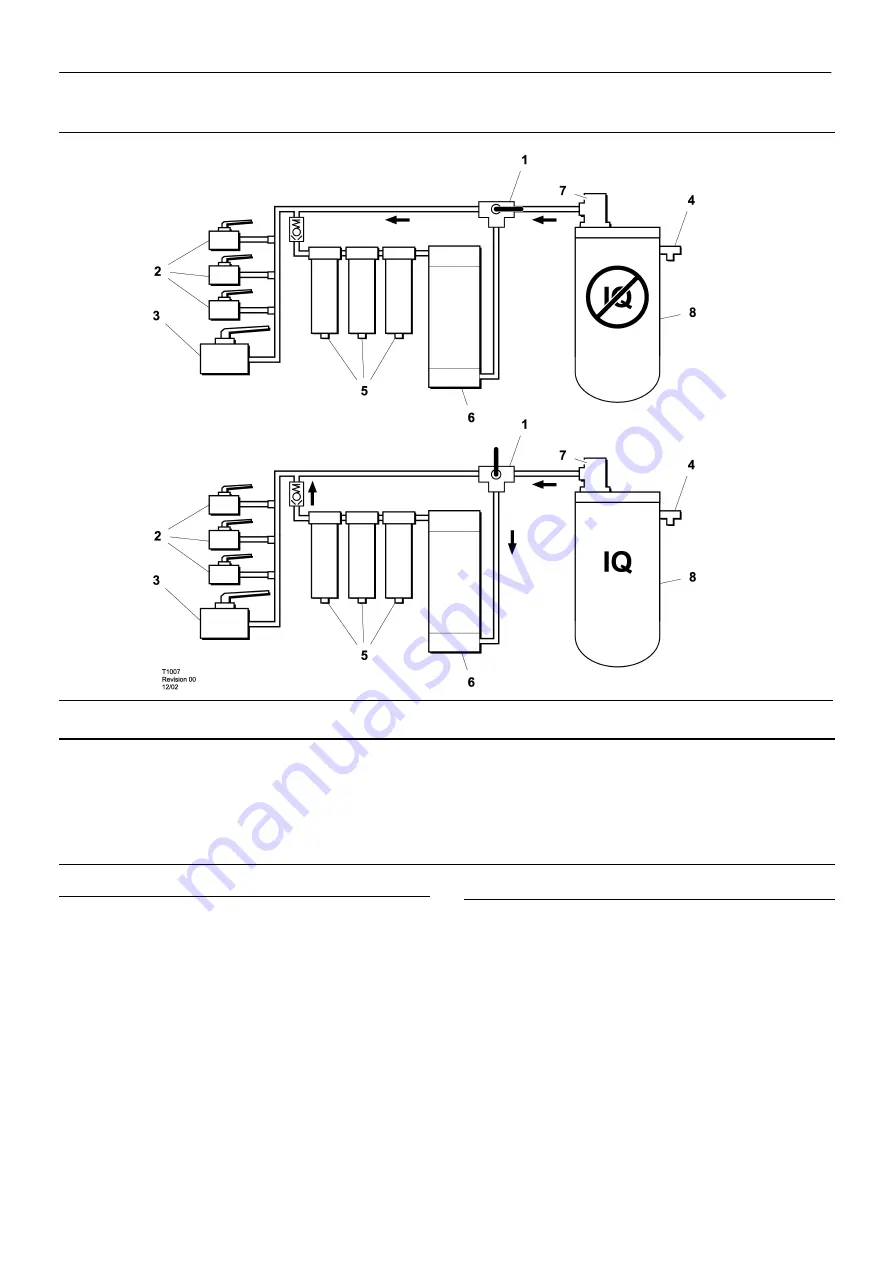
OPTIONS
47
9/230, 9/270, 9/300, 12/235, 17/235, 21/215, 9/230HA, 9/270HA, 9/300HA, 12/235HA, 17/235HA, 21/215HA
IQ SYSTEM
OPERATING INSTRUCTIONS – 1
KEY
1
Three way valve
2
Ball valve1
1
/
4
”
3
Ball valve2”
4
Safety valve
5
Filters
6
Aftercooler
7
Minimum pressure valve
8
Separator tank
IQ SYSTEM
The IQ System is a complete, self–contained system which
provides cooler, cleaner air than from a standard portable
compressor. The system utilizes an integral aftercooler,
high–efficiency filtration, and a patented condensate disposal system
to provide the cool, clean air. The condensate disposal system
injects all liquid condensed from the moisture separator and filters
into the engine exhaust system where it is vaporized by heat. This
eliminates the need for collecting the condensate, and the added
cost of disposing of the condensate, which is often regulated by
local, state, and/or federal regulations.
When equipped with the low ambient feature, the IQ System
automatically adjusts movable louvers to control airflow through the
aftercooler, ensuring that the compressed air temperature always
remains above freezing temperatures (typically 45
F) at any ambient
temperature down to –20
F. This prevents the need for 120V AC
heat tracing systems, or any manual adjustment to prevent freezing
of the compressed air system. All drain points for the condensate
handling system are heated with 24VDC heaters, which are integral
to the compressor heater system.
Standard Non–Louvered configuration not to be operated below
freezing.
IQ SYSTEM
OPERATING INSTRUCTIONS – 2
The compressed air exits the separator tank through the top
cover piping, and can then travel along one of two paths, selectable
via manual valving.
One path allows Standard Operation, which bypasses the IQ
System, and delivers air quality equivalent to a standard oil–flooded
portable compressor. If the IQ System is enabled by proper setting
of the selector valve, the compressed air first enters the aftercooler.
The aftercooler is cooled by the incoming compressor package
air, which is controlled by movable louvers mounted on the
aftercooler (if equipped with low ambient option). At most conditions,
the louvers are fully open, and maximum aftercooling is available.
The compressed air and condensate (water with a small amount of
compressor lubricant) exits the aftercooler and enters the moisture
separator, where most of the condensate is removed. The
compressed air then flows through two stages of filtration, where the
aerosol water and oil is removed down to approximately 0.01 ppm,
and all particulates are removed down to 0.01 micron.