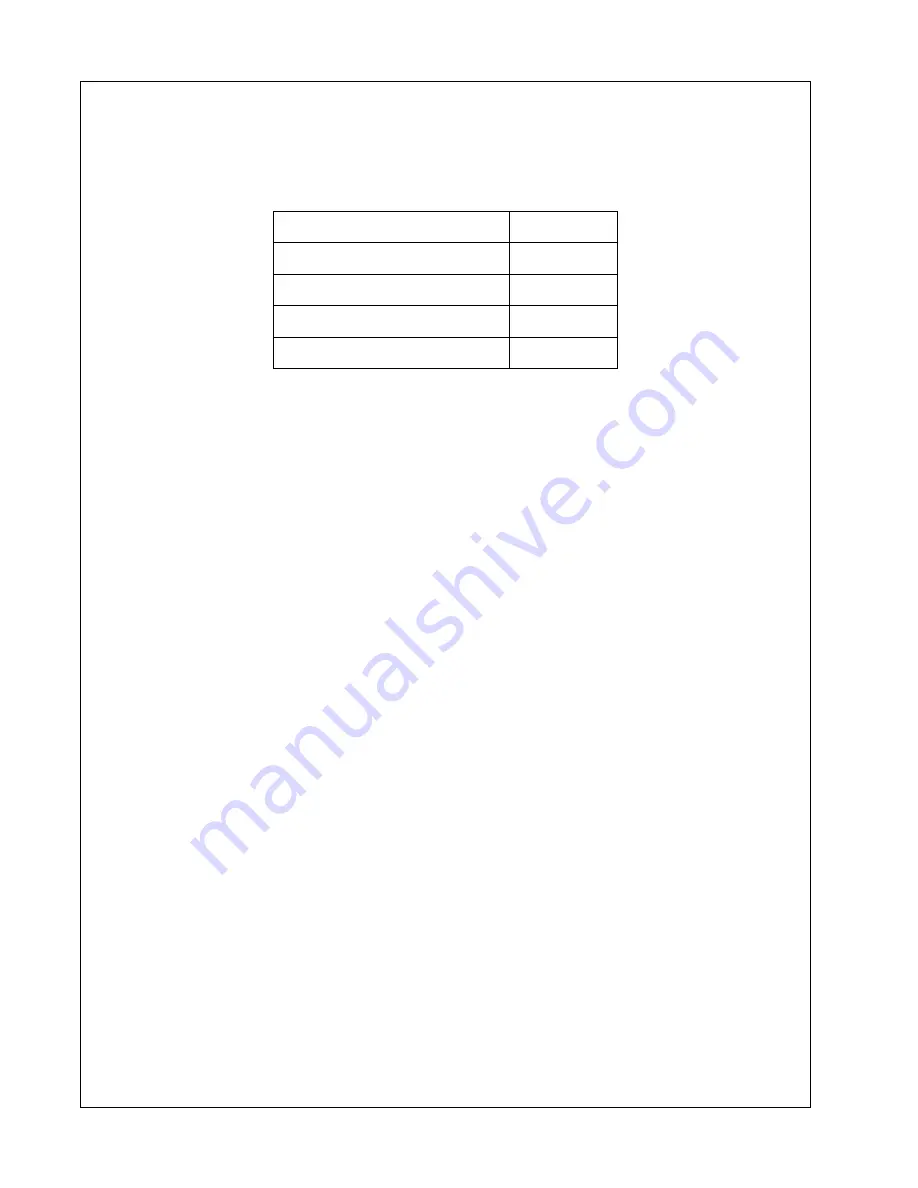
Operating & Maintenance Manual
Engine Instructions
70
22442594
Water quality is important to the performance of the cooling system. Distilled, or de-
mineralized water is recommended for mixing with ethylene glycol base engine coolant
concentrate.
IMPORTANT: Do not use cooling system sealing additives or antifreeze that contains
sealing additives.
Supplemental Coolant Additives
The concentration of coolant additives is gradually depleted during engine operation. For all
recommended coolants, replenish additives between drain intervals by adding a supplemental
coolant additive every 12 months.
IMPORTANT: Only use coolant additive to replenish the coolant. Do not use additive
when the entire system is drained and refilled.
Consult the coolant supplier and follow the manufacturer's recommendation for use of
supplemental coolant additives.
The use of non-recommended supplemental coolant additives may result in additive drop-out
and gelation of the coolant.
Add the manufacturer's recommended concentration of supplemental coolant additive. DO
NOT add more than the recommended amount.
Coolant Drain Intervals
Drain the factory fill engine coolant, flush the cooling system, and refill with new coolant after
the first 3 years or 3000 hours of operation. Subsequent drain intervals are determined by the
coolant used for service. At each interval, drain the coolant, flush the cooling system, and refill
with new coolant.
Operating in Warm Temperature Climates
Ingersoll-Rand engines are designed to operate using glycol base engine coolants.
Always use a recommended glycol base engine coolant, even when operating in geographical
areas where freeze protection is not required.
Chlorides
<40 mg/L
Sulfates
<100 mg/L
Total Dissolved Solids
<340 mg/L
Total Hardness
<170 mg/L
pH
5.5 to 9.0
Summary of Contents for 10/125
Page 8: ...8 TABLE OF CONTENTS Operating Maintenance Manual TITLE PAGE...
Page 9: ...22442594 9 Foreword...
Page 13: ...22442594 13 Warranty...
Page 21: ...22442594 21 Decals...
Page 23: ...Decals Operating Maintenance Manual 22442594 23...
Page 24: ...Operating Maintenance Manual Decals 24 22442594...
Page 25: ...Decals Operating Maintenance Manual 22442594 25...
Page 27: ...Decals Operating Maintenance Manual 22442594 27...
Page 28: ...Operating Maintenance Manual Decals 28 22442594...
Page 29: ...22442594 29 Noise Emission...
Page 36: ...Operating Maintenance Manual Noise Emission 36 22442594...
Page 37: ...22442594 37 Safety...
Page 43: ...22442594 43 General Arrangement...
Page 51: ...22442594 51 Operating Instructions...
Page 64: ...Operating Maintenance Manual Operating Instructions 64 22442594...
Page 65: ...22442594 65 Engine Instructions...
Page 91: ...22442594 91 Maintenance...
Page 108: ...Operating Maintenance Manual Maintenance 108 22442594...
Page 109: ...Maintenance Operating Maintenance Manual 22442594 109...
Page 112: ...Operating Maintenance Manual Maintenance 112 22442594...
Page 113: ...22442594 113 Machine Systems...
Page 117: ...22442594 117 Service Tools...
Page 122: ...Operating Maintenance Manual Service Tools 122 22442594...
Page 123: ...22442594 123 Fault Finding...
Page 127: ...22442594 127 Options...
Page 133: ...2004 Ingersoll Rand Company Printed in the USA...