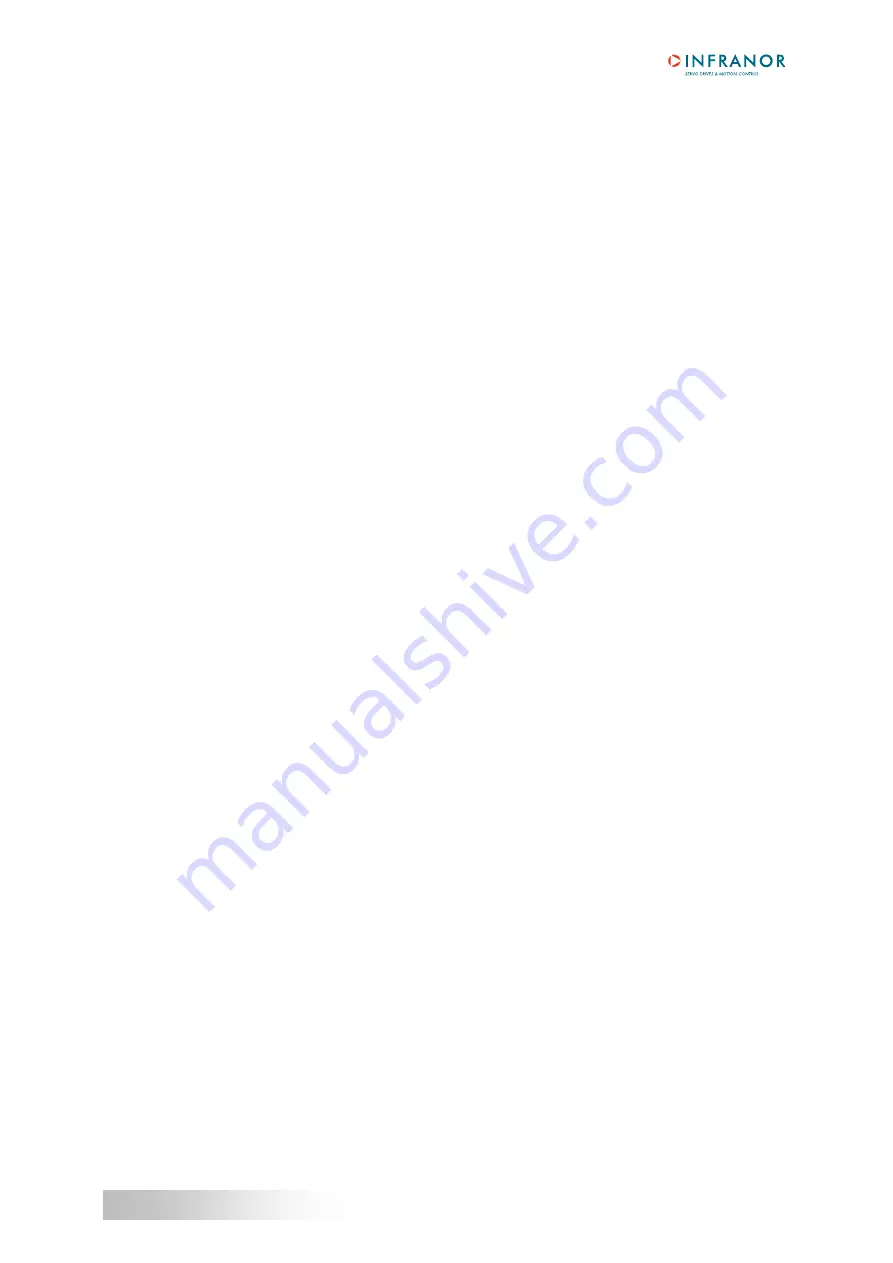
75
CHAPTER 10 – Troubleshooting
SMT-BD1/t
2.3.9 - "POSITION" (FOLLOWING ERROR) fault
Check that the
Speed following error
parameter value is compatible with the required amplifier operating cycle.
If necessary, increase the
Speed following error
parameter value.
3 - OPERATING PROBLEMS
3.1 - Motor does not move
- Check that the amplifier is on.
- Check that the power supply is on.
- Check the amplifier fuses (F1 and F2) and the motor connection.
- Check the wiring of the ENABLE logic input.
- Check that the amplifier is enabled.
3.2 - Motor supplied but no torque
- Check that the
Maximum current
and
Rated current
parameters have no zero value.
3.3 - Shaft locked, eratic oscillations or rotation at maximum speed
- Check the resolver wiring on the X1 connector and the mechanical mounting of the resolver on the motor.
- Check the value of the motor parameters (number of pole pairs, resolver wiring, motor phase).
3.4 - Discontinuous motor rotation with zero torque positions
- Check the connection of all three phase cables between motor and amplifier.
3.5 - Loud crackling noise in the motor at standstill
- Check that the Motor-Amplifier-Controller ground connections comply with the recommendations
3.6 - Loud noise in the motor at standstill and when running
- Check the rigidity of the mechanical transmission chain between motor and load (backlash and elasticity in
the gearboxes and couplings).
- Execute
the
AUTOTUNING
command again by choosing a lower bandwidth (
Medium
or
Low
).
3.7 - Sequence not executed
If in "operation enabled" status, the motor does not move at a sequence start:
* Check if a start condition has been defined for this sequence and not been fulfilled.
4 - SERVICE AND MAINTENANCE
When exchanging an amplifier on a machine, proceed as follows:
- Check that the new amplifier has the same hardware configuration as the old one (including its address),
- Plug the parameter EEPROM of the old amplifier on the new one.
The new amplifier is configurated like the old one.