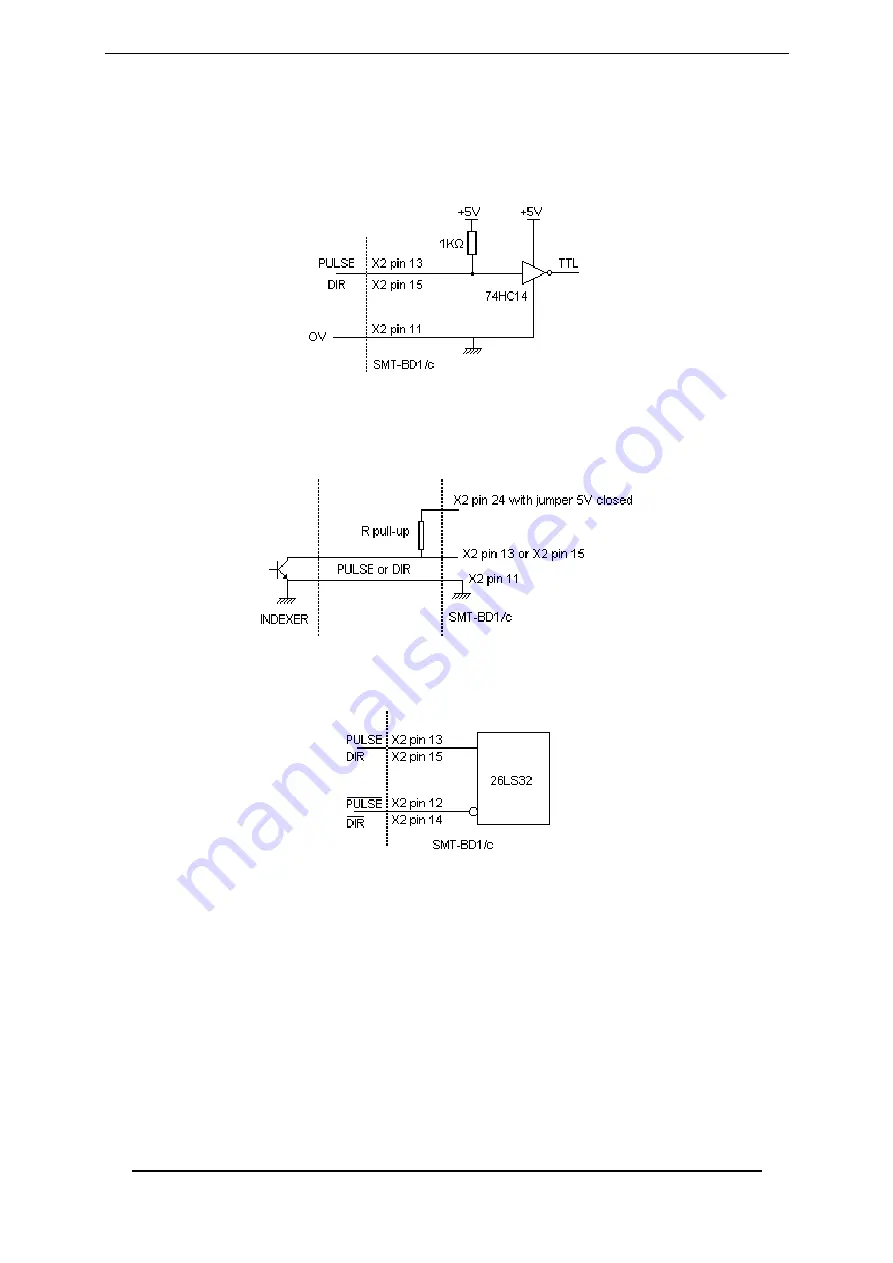
Option "c" · Chapter 3: Inputs - Outputs
10
1.3 - I
NDEXER INPUT SPECIFICATION
The TTL
PULSE
and
DIR
inputs are connected to the amplifier as shown below:
For indexers with open collector output and operating at high frequencies (> 100 kHz), a pull-up
resistor corresponding to the transistor output current must be wired in the X2 connector, as
shown below (the pull-up resistor is parallel mounted to the 1 k
W
resistor in the amplifier).
The differential
PULSE
and
DIR
inputs are connected to the amplifier as shown below:
This type of input is suitable for long indexer-amplifier connections (a 26LS31 driver is
recommended).