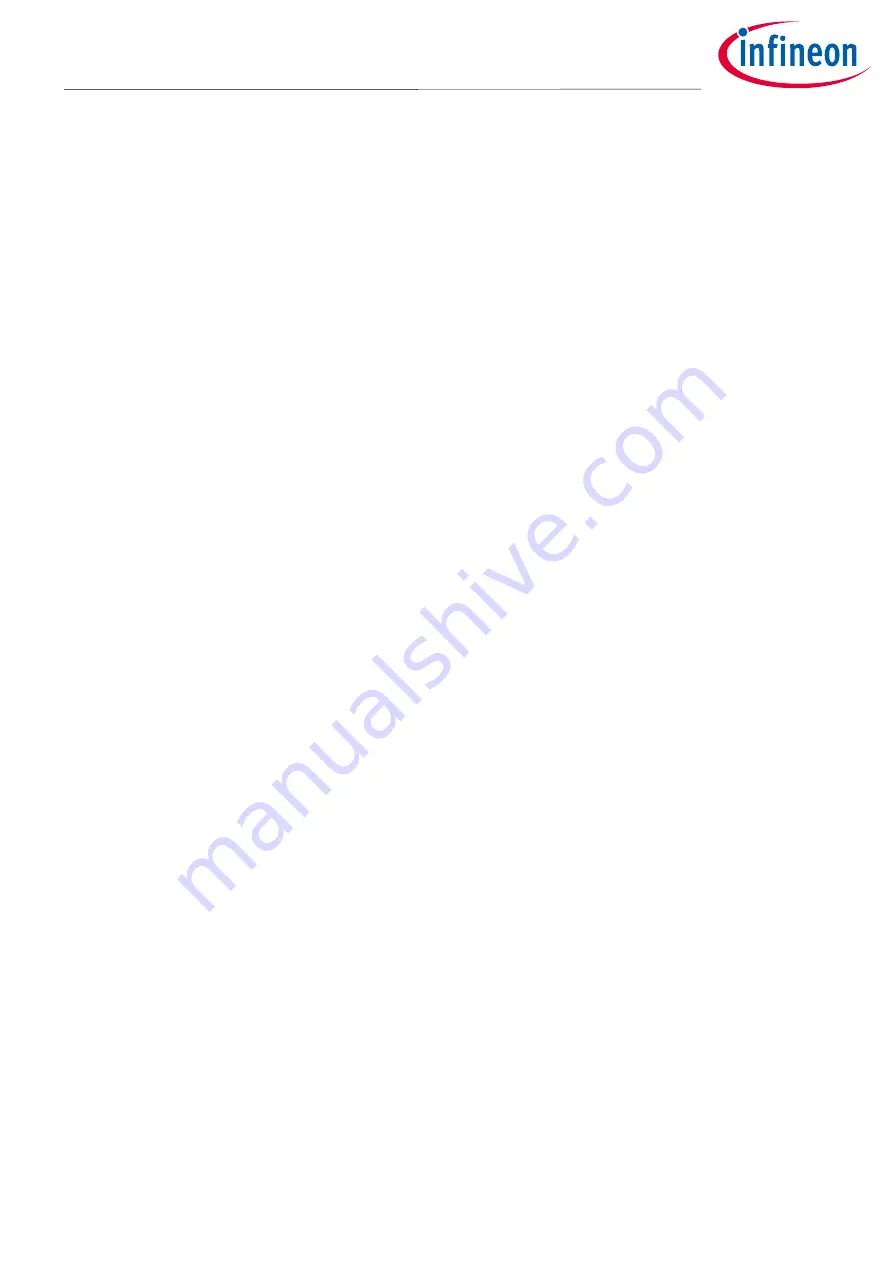
Additional Information
12 of 20
Revision 6.0
2020-11-12
Recommendations for Board Assembly of Infineon Quad Flat
Packages
PCB Assembly
highly difficult. Certain precautions have to be taken if any kinds of flux residues remain on the board prior to
any kind of coating. For power packages, leakage currents and the potential for shorting below components
have to be considered when choosing the specific flux type (e.g. halide-free vs. zero halides).
Generally, solder paste is sensitive to age, temperature, and humidity. Please follow the handling
recommendations of the paste manufacturer.
3.3
Component Placement
Although the self-alignment effect due to the surface tension of the liquid solder will support the formation of
reliable solder joints, the components have to be placed accurately depending on their geometry. Positioning
the packages manually is not recommended, especially for packages with small terminations and pitch. An
automated pick-and-place machine is recommended to obtain reliable solder joints.
Component placement accuracies of +/-50 µm and less are obtained with modern automatic component
placement machines using vision systems. With these systems, both the PCB and the components are optically
measured and the components are placed on the PCB at their programmed positions. The fiducials on the PCB
are located either on the edge of the PCB for the entire PCB, or at additional individual mounting positions
(local fiducials). These fiducials are detected by a vision system immediately prior to the mounting process.
For further information about component placement, please refer to the
General Recommendations for Board
Assembly of Infineon Packages
document that is available on the Infineon web page [1]. Please also feel free to
contact your local sales, application, or quality engineer.
3.4
Reflow Soldering
For PCB assembly of QFP components, the widely used method of reflow soldering in a forced convection oven
is recommended. Soldering in a nitrogen atmosphere can generally improve the solder joint quality but is not
necessary to create a reliable joint.
The soldering profile should be in accordance with the recommendations of the solder paste manufacturer to
achieve optimal solder joint quality. The position and the surrounding of the component on the PCB, as well as
the PCB thickness, can influence the solder joint temperature significantly. Power packages where leakage
currents and shorting below the component have to be considered should be soldered with decreased flux
spreading. Therefore, it is recommended to optimize the reflow profile in such a way that excessive flux or
solder spattering is avoided.
Minimum Reflow Conditions
The lower temperatures and durations of an optimal reflow profile must stay above those of the solderability
qualification. The solderability of the terminations of Infineon components is tested according to the standards
IEC 60068-2-58 and J-STD-002 [2][3].
Maximum Reflow Conditions and Cycles
Components that are Moisture-Sensitivity Level (MSL) classified by Infineon have been tested by three reflow
runs in accordance with the J-STD-020 standard, covering a double-sided reflow and one rework cycle. The
maximum temperatures must not be exceeded during board assembly. Please refer to the product barcode
label on the packing material that states this maximum reflow temperature according to the J-STD-020 [4]
standard as well as the MSL according to the J-STD-033 standard [5].
Typical Infineon QFP are generally suited for mounting on double-sided PCBs. Solder joints of components on
the first PCB side will again reflow in the second step. In the reflow zone of the oven (i.e. where the solder is
liquid), the components are only held in place by the wetting forces from the molten solder. Gravity acting in