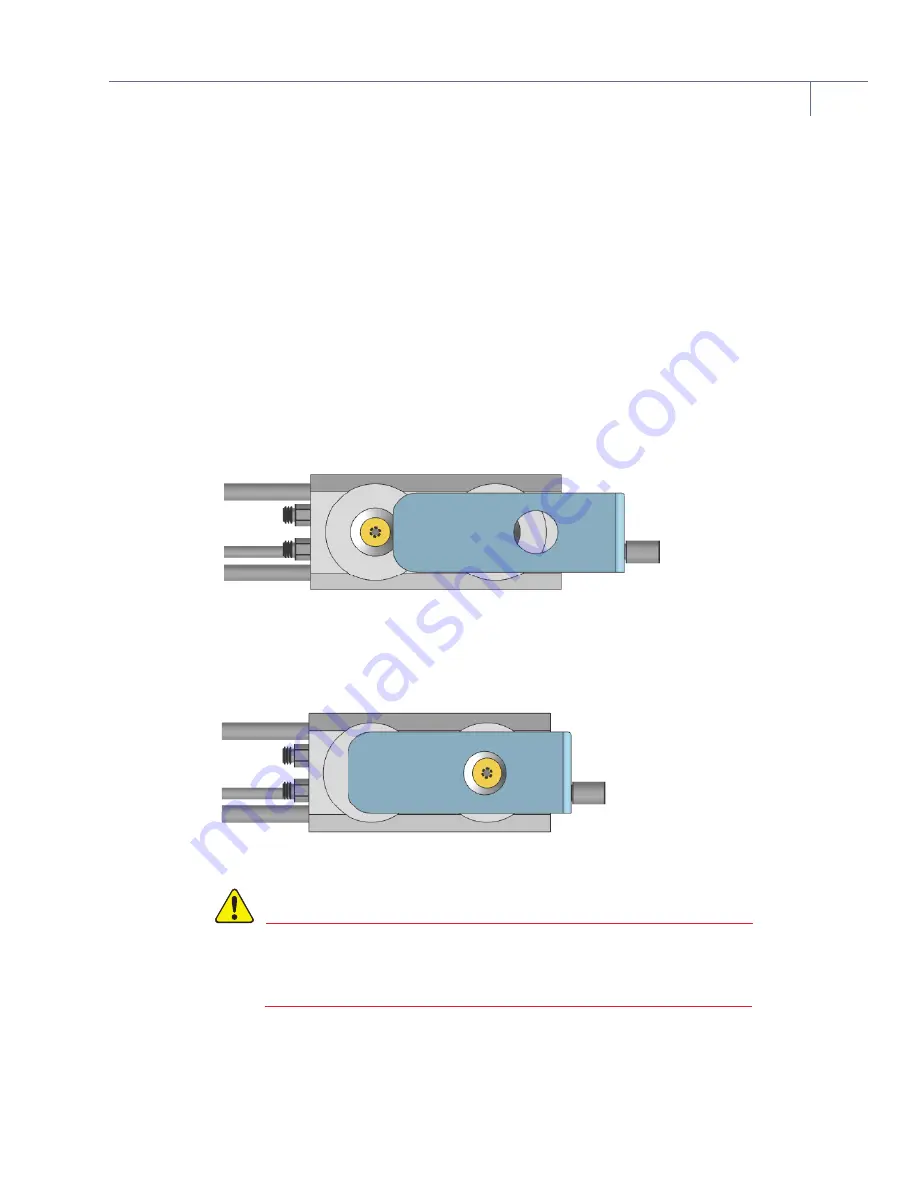
5 of 13
Easy Rate Sensor
PN 074-677-P1A
Actuator Function Check
Temporarily connect an air supply to the actuator air tube and test operation for 10 to 15
cycles. Operating range is:
70–80 psi (gauge)
85–95 psi (absolute)
5.8–6.5 bar (absolute)
584–653 kPa (absolute)
When actuated, shutter movement should be smooth, rapid, and complete, and should
extend as shown. The crystal aperture must be completely exposed. It is acceptable if
the crystal holder is only partially exposed. (See
Figure 3 Acceptable shutter end extension
When deactivated, the shutter should completely cover the crystal opening.
Repositioning of the shutter or actuator may be required to achieve optimum on/off
positioning. If operation is found to be impaired, contact INFICON. (See
Figure 4 Shutter completely covering the crystal opening
NOTE:
A solenoid valve (PN 750-420-G1) is required with any new shutter installation.
WARNING
Do not exceed 100 psi (gauge), 115 psi (absolute), 7.9 bar
(absolute), or 791 kPa (absolute). Connection to excessive
pressure may result in personal injury or equipment damage.