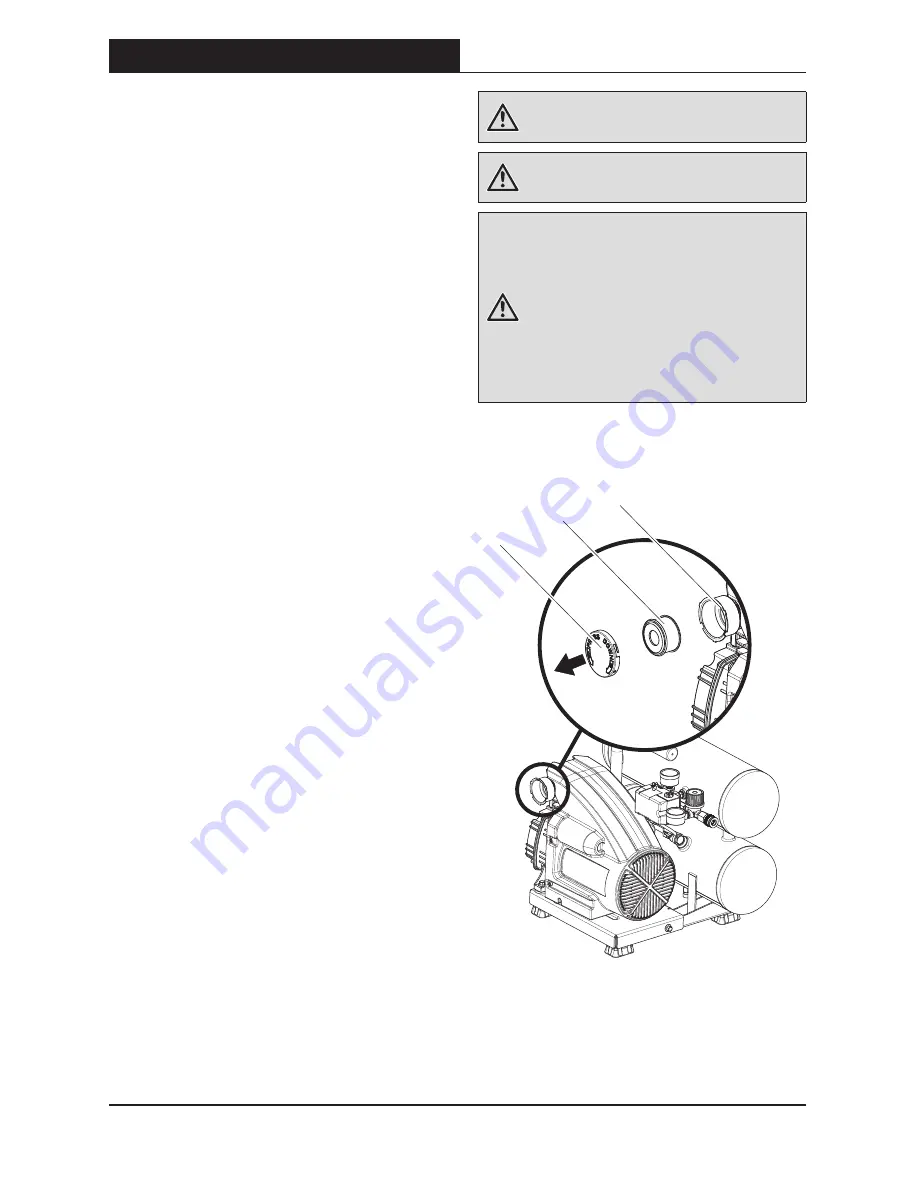
17
industrialaircontractor.com
Please contact 1-888-895-4549 for further assistance.
Maintenance
GENERAL MAINTENANCE
□
Condensate forms in the tank when
there is humidity in the air. Depending
on the environmental conditions, drain
the condensate daily and/or every hour.
For instructions, see
Draining the tank
on page 16.
□
The safety valve automatically releases air
when the receiver pressure exceeds the preset
maximum.
□
Inspect the tank annually for rust, pin holes,
or other imperfections that could cause it to
become unsafe.
□
Avoid using solvents when cleaning plastic
parts. Most plastics are susceptible to damage
from various types of commercial solvents and
may be damaged by their use.
□
Use clean cloths to remove dirt, dust, oil,
grease, etc.
LUBRICATION
This compressor requires oil to be in the crank case
in order to lubricate the pump for operation (see
REFILLING THE COMPRESSOR PUMP WITH OIL
on page
11). It is also necessary to change this oil after the
first 10 hours of use and every 100 hours after that.
CLEANING THE AIR FILTER
From time to time, the air filter needs to be removed
and cleaned.
□
Turn the air compressor OFF ( O ).
□
Unplug the air compressor.
□
Unsnap the air filter cover (1) to remove.
□
Remove the air filter (2) from the air filter
housing (3).
□
Blow compressed air through the air filter for
10-15 seconds using an approved OSHA nozzle.
2
1
3
WARNING:
When servicing, use only identical Industrial
Air Contractor replacement parts. Use of any other parts
may create a hazard or cause product damage.
WARNING:
Always release all pressure, disconnect from
the power supply, and allow the unit to cool to the touch
before cleaning or making repairs on the air compressor.
WARNING:
Do not at any time let brake fluids, gasoline,
petroleum-based products, penetrating oils, etc., come
in contact with plastic parts. Chemicals can damage,
weaken or destroy plastic which may result in serious
personal injury. Electric tools used on fiberglass material,
wallboard, spackling compounds, or plaster are subject to
accelerated wear and possible premature failure because
the fiberglass chips and grindings are highly abrasive to
bearings, brushes, commutators, etc. Consequently, we
do not recommended using this tool for extended work on
these types of materials. However, if you do work with any
of these materials, it is extremely important to clean the
tool using compressed air.