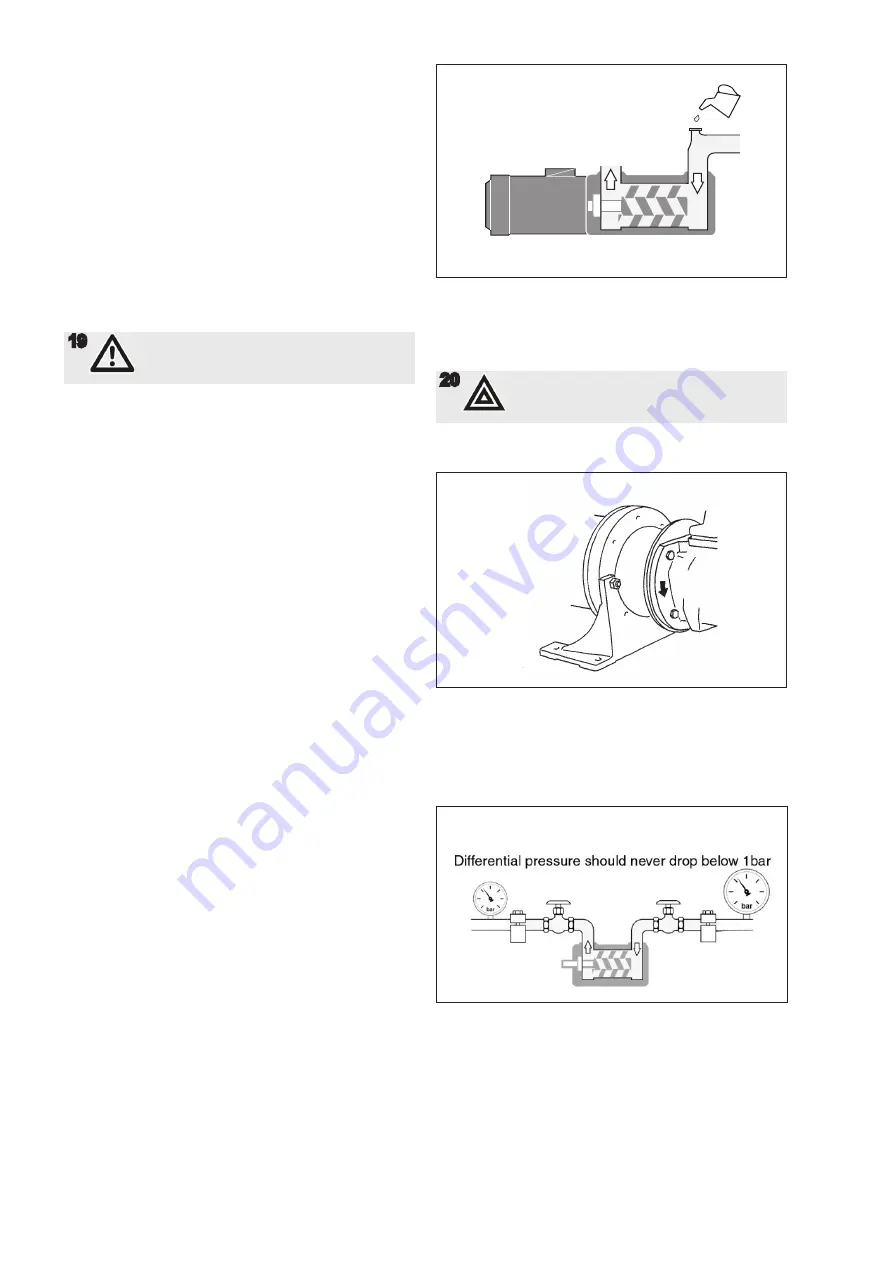
LP
E4
2
01
8.
01
e
n-
G
B
, I
D
-N
o.
: 1
63
-0
41
/0
www.imo.se
8
Pressure testing and flushing
The system must be flushed and pressure tested before
connecting the pump. If corrosive liquid, such as water
is used, the system must be thoroughly drained, dried
and protected against corrosion after having been
flushed.
Before starting:
After installation and whenever it can be assumed that
the pump has been emptied, the pump must be thor-
oughly filled with liquid. See fig 11.
19
Make sure the prime mover is locked out
and can not be started accidentally.
Direction of rotation
When the pump is ready to be started, switch the motor
briefly on and off and check that the drive motor rotates
in the correct direction as indicated by the rotation ar-
row. The arrow is placed on the side of the front cover
5010 as well as on riveted steel plates on the connect-
ing frame 003.
Differential pressure
Differential pressures bellow 1 bar is strictly forbidden
as the magnetic coupling under these conditions may
loose its cooling flow and cause an overheating of the
magnetic coupling with a risk of a potential fire as a
result.
We do strongly recommend magnetic coupled pumps to
be equipped with a differential pressure monitoring de-
vice that stops the pump automatically if the differential
pressure for some reason should drop to below 1bar.
Air in the pumped fluid
It is forbidden to use the LPE Optiline pump with fluids
that contains more than 0,2% of air due to the risk of
ignition during an eventual overheating of the pump.
Fig. 11 Filling the pump
Fig. 12 Direction of rotation
Fig. 13 Differential Pressure
20
Don't mix up with arrow for inlet and
outlet!
Startup