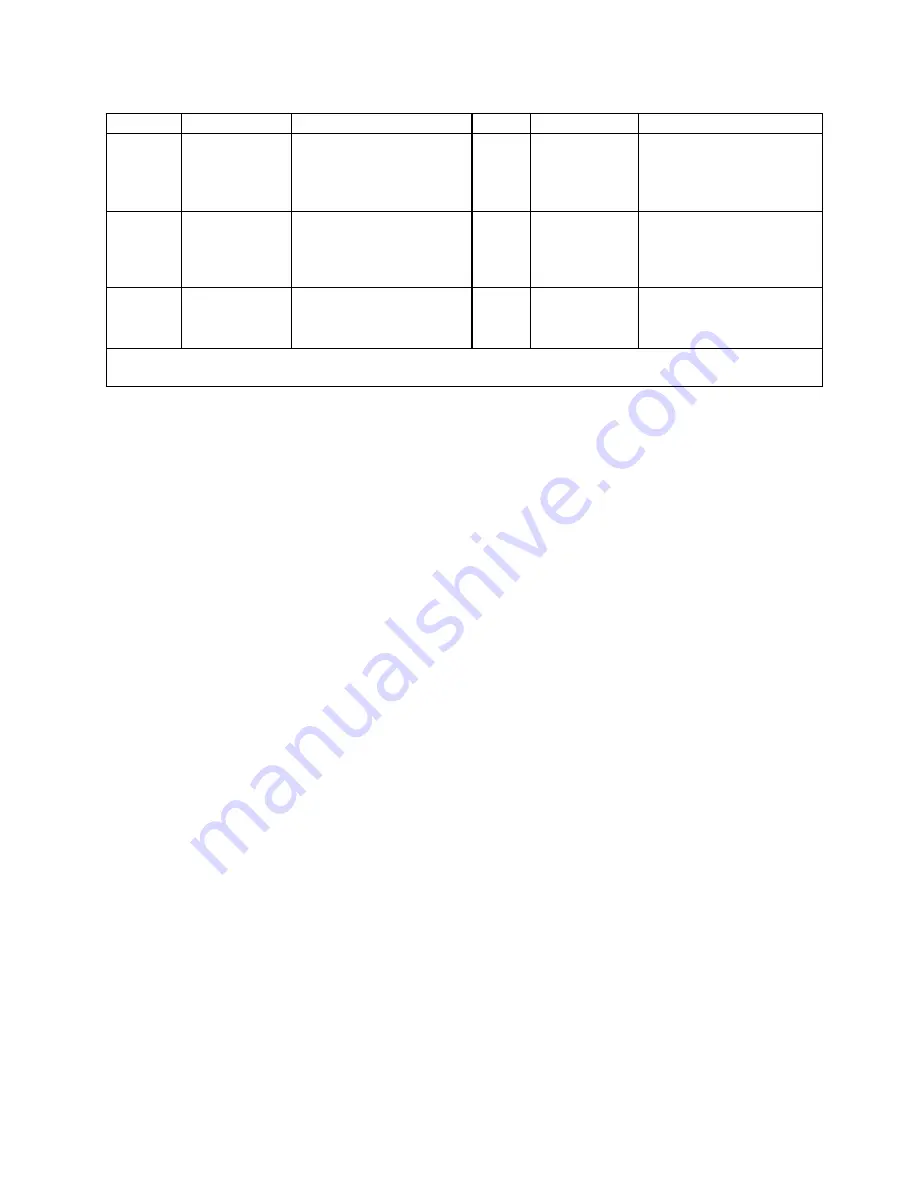
13
Table 3
TORQUE VALUES - MECHANICAL SEAL PUMPS
PART
ROTOR SIZE
TORQUE VALVE
PART ROTOR SIZE
TORQUE VALVE
010 and
031
(1)
187
218
250
312
35 lbs. ft. (± 5 lbs. ft.)
55 lbs. ft. (± 5 lbs. ft.)
70 lbs. ft. (± 5 lbs. ft.)
78 lbs. ft. (± 5 lbs. ft.)
018
187
218
250
312
18 lbs. ft. (± 2 lbs. ft.)
20 lbs. ft. (± 2 lbs. ft.)
20 lbs. ft. (± 2 lbs. ft.)
38 lbs. ft. (± 2 lbs. ft.)
010
(2)
187
218
250
312
90 lbs. ft. (± 5 lbs. ft.)
75 lbs. ft. (± 5 lbs. ft.)
145 lbs. ft. (± 5 lbs. ft.)
78 lbs. ft. (± 5 lbs. ft.)
023
187
218
250
312
10 lbs. ft. (± 2 lbs. ft.)
15 lbs. ft. (± 2 lbs. ft.)
15 lbs. ft. (± 2 lbs. ft.)
30 lbs. ft. (± 2 lbs. ft.)
003
187
218
250
20 lbs. ft. (± 2 lbs. ft.)
20 lbs. ft. (± 2 lbs. ft.)
20 lbs. ft. (± 2 lbs. ft.)
047
312
30 lbs. ft. (± 2 lbs. ft.)
(1) Part Number 010 or 031 installed in inboard cover (009).
(2) Part Number 010 installed in inlet head (026).
6. Assemble power rotor (011) as follows:
NOTE:
For pumps with no mechanical seal, proceed to Step 6 (d).
(a)
Install truarc ring (035, Figures 12 and 14) or shim (051, Figure 11, rotor size 312).
(b)
Install mechanical seal (025) rotating assembly (3, Figures 2 through 10).
(c)
Install mechanical seal (025) stationary assembly (1 and 2, Figures 2 through 10) on power
rotor or in spacer (014) based on seal design.
(d)
Install spacer (014) and inner truarc ring (013).
(e) Install ball bearing (015) by pressing on inner race only of ball bearing (015). NOTE: Inner
race of ball bearing (015) should be positioned next to truarc ring (013).
(f)
Install truarc ring (013) next to ball bearing (015) in outer ring groove of power rotor (011).
7. On pumps equipped with mechanical seal, install gasket or O-ring in mechanical seal bore of cover
(009).
8. Install assembled power rotor (011), centering all parts, in case (001).
9. Install retainer (017) using bolts (018). Torque bolts (018) to proper value given in Table 3.
10. Install idlers (019) into housing (002) idler bores by turning idlers (019) while inserting them into
housing.
11. Install cups (020) on idlers (019), where applicable.
*
.
* Note: Some Idlers have a hydrostatic thrust design and do not need idler cups (20).
12. Install spacers (022), thrust plate (021), lockwashers 24 and bolts (023) or jam nuts (047). Torque
bolts (023) or jam nuts (047) to proper value given in Table 3.
13. . Install O-ring (008) on inlet head (026) or gasket (008) on case (001). Install inlet head (026) or
clamp ring (026, Figure 26, Arrangement C) using capscrews or bolts (010). Torque capscrews or
bolts (010) to correct value given in Table 3. NOTE: If installed, lockwashers (030) will be installed
with bolts (010).
*
Note: Some idlers have a hydrostatic thrust design and do not use idler cups (020)
Summary of Contents for *G3D-187
Page 18: ...18 Figure 12 Type 2 8 1 O ring Seat Rotor Size 250...
Page 20: ...20 Figure 14 Type 2 81 and O ring Seat Rotor Size 250...
Page 21: ...21 Figure15 Type BX Rotor Size 187 through 250...
Page 22: ...22 Figure16 Type 9B3 Rotor Size 187...
Page 23: ...23 Figure 17 No Seal Rotor Sizes 187 through 312...
Page 27: ...27 Note Idler Cups 20 not required on some designs...
Page 28: ...28 Note Idler Cups 20 not required on some designs...
Page 29: ...29 Note Idler Cups 20 not required on some designs...
Page 30: ...30 Note Idler Cups 20 not required on some designs...
Page 31: ...31 Note Idler Cups 20 not required on some designs...
Page 32: ...32 Note Idler Cups 20 not required on some designs...
Page 33: ...33...
Page 34: ...34...
Page 35: ...35...