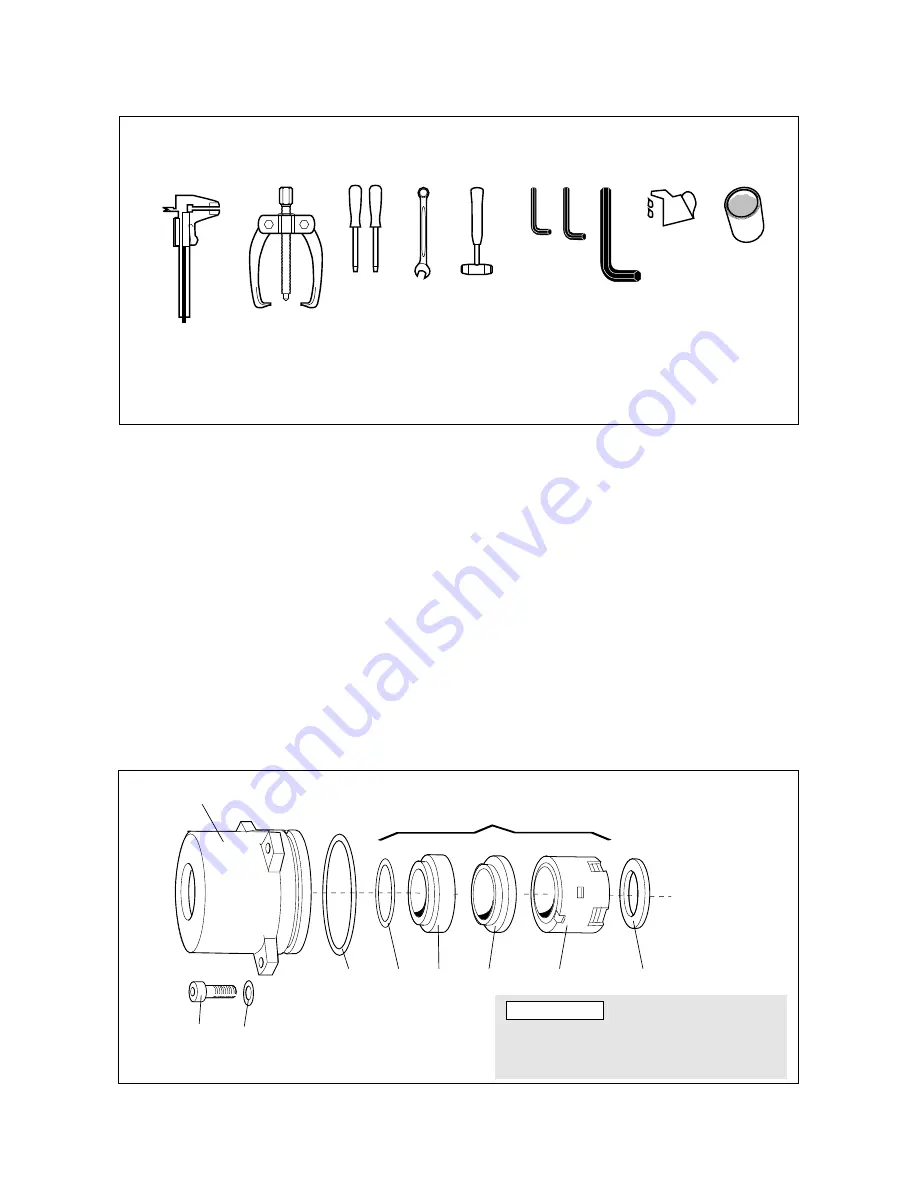
6
D4 0617GB
December 2000
GREASE
List of tools necessary for dismantling/reassembly
Fig. 3
Sliding Puller
calliper
Plastic
mallet
ACG7 © IMO AB
O-rings
All O-rings found to be hard or damaged shall be
replaced.
Inspection of shaft seal
As the seal faces of a mechanical shaft seal are
lubricated by the fluid, a certain leakage will
always be present. Up to ten drops per hour can be
considered as acceptable. An external visual
inspection of the pump is advisable at least every
two days to assure that the shaftseal is not leaking
too much. Excessively leaking shaft seals should be
changed without delay, as the leakage normally will
grow worse and cause additional damage.
Follow the instructions in the dismantling/reassembly
session.
When working with a shaft seal, cleanliness is of
utmost importance. Avoid touching the seal faces. If
necessary, the seal faces should be cleaned immedi-
ately prior to assembly, using a dust free cloth and
clean solvent.
Never use grease on the seal faces.
D4 5 © IMO AB
Shaft seal – assembly drawing
520A S2 S1 S4
S5
507
521
521A
520
ATTENTION
Be careful to mount these parts in right
order and in right direction!
Look carefully at this drawing!
S1 Seat
S2 O-ring
S4 Seal ring
S5 Bellows unit
2 pcs of
screw-
driver
Screw
spanner
14 mm
Allen keys
5 mm, 6 mm, 10 mm
Oil can
Grease
Shaft seal
D4 4 © IMO AB
Fig. 4