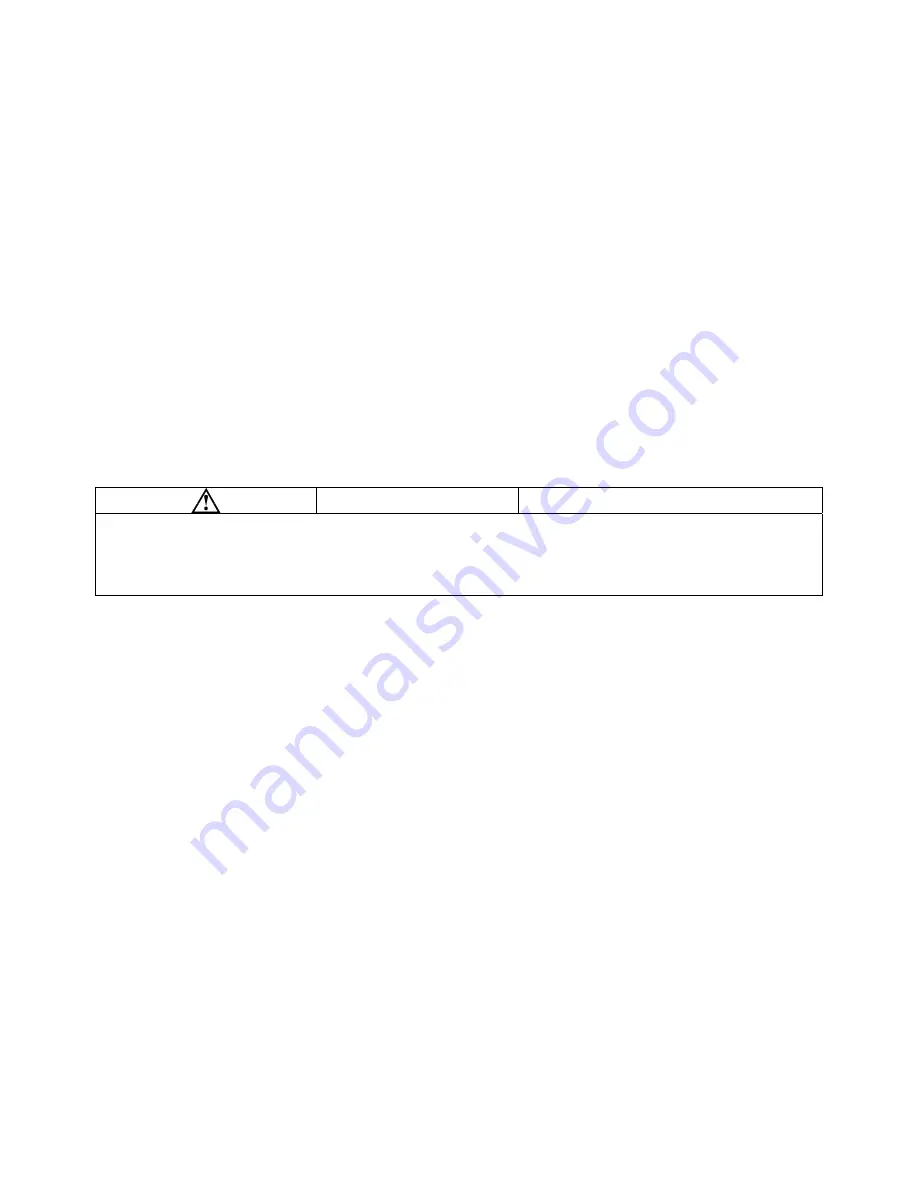
3
A. GENERAL INSTRUCTIONS
Instructions found herein cover disassembly, assembly and parts identification of
BK6DHZ(C)-250, 275, 312 and 400 pumps.
NOTE:
Individual contracts may have specific provisions that vary from this manual.
Should any questions arise which may not be answered by these instructions,
refer to General Instructions Manual, CA-1, provided with your order. For further
detailed information and technical assistance please refer to Imo Pump,
Technical/Customer Service Department, at (704) 289-6511.
This manual cannot possibly cover every situation connected with installation, operation,
inspection, and maintenance of equipment supplied. Every effort was made to prepare text of
manual so that engineering and design data is transformed into most easily understood wording.
Imo Pump must assume personnel assigned to operate and maintain supplied equipment and
apply this instruction manual have sufficient technical knowledge and are experienced to apply
sound safety and operational practices which may not be otherwise covered by this manual.
In applications where equipment furnished by Imo Pump is to become part of processing
machinery, these instructions should be thoroughly reviewed to ensure proper fit of said
equipment into overall plant operational procedures.
WARNING
If installation, operation and maintenance instructions are not correctly and strictly followed and
observed, injury to personnel or serious damage to pump could result. Imo Pump cannot accept
responsibility for unsatisfactory performance or damage resulting from failure to comply with
instructions.
B. INTRODUCTION
Instruction manual covers series BK6DHZ(C)-250, 275, 312 and 400 Imo pumps. This series of
pumps has been designed for use in high pressure fuel oil applications. Model, and design
construction of each pump can be identified by designator code on pump nameplate. Definitions
of model designators are identified in Figure 1.
C. DESCRIPTION OF EQUIPMENT
BK6DHZ(C)-250, 275, 312 and 400 pumps are positive displacement, rotary screw pumps
consisting of a precision bored housing that encloses a driven screw (power rotor) and two
intermeshing following screws (idler rotors). These screws, when rotating, form a succession of
closures or cavities. As they rotate, fluid is moved axially from inlet port to outlet port in a
continuous, uniform flow with minimum fluid pulsation and pump noise.