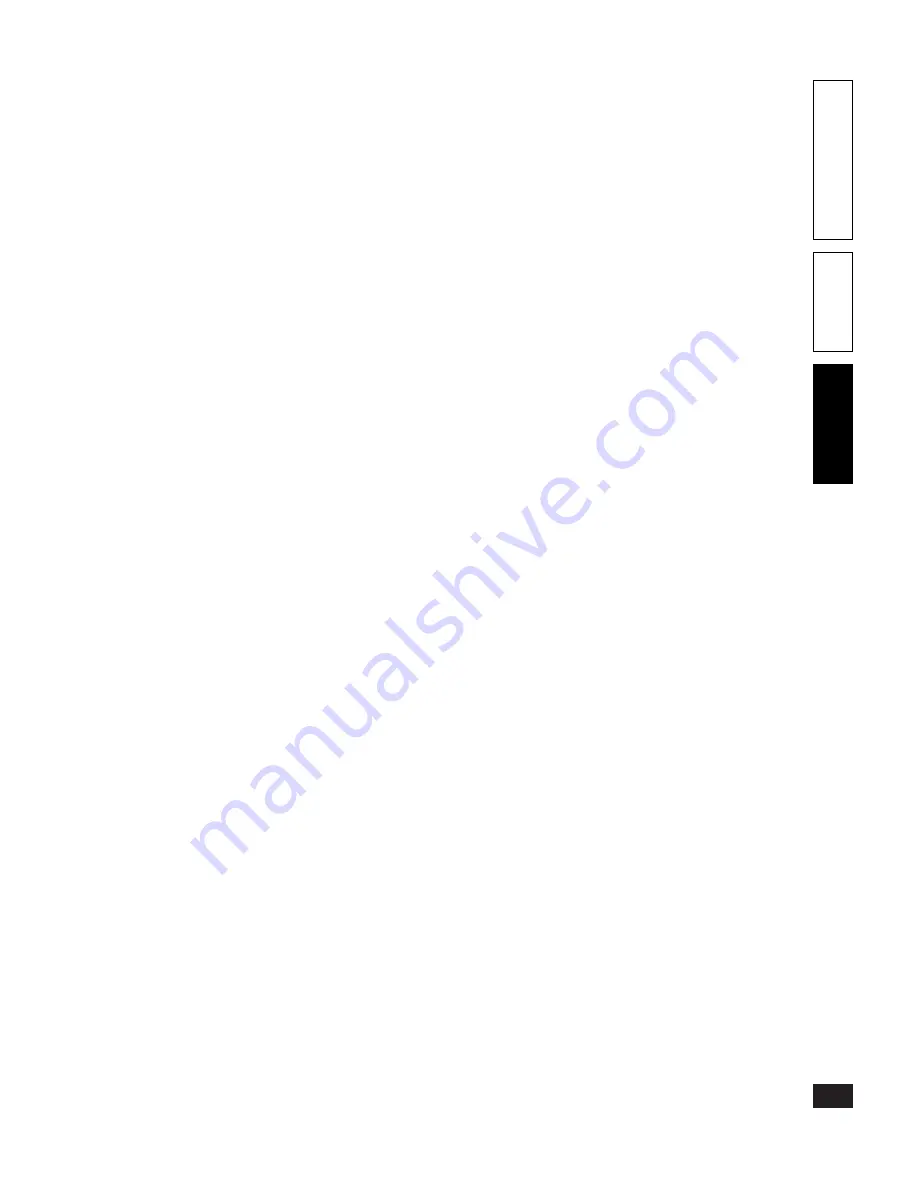
3.5 Troubleshooting.
N.B.:
maintenance must be performed by a qualified techni-
cian (e.g. Immergas Technical Assistance Service).
- Smell of gas. Caused by leakage from gas circuit pipes.
Check tightness of gas supply circuit.
- Repeated ignition blocks (error 1). is can be caused by:
incorrect electrical feed, check correct L and N polarity.
No gas, check pressure in mains and that the gas supply
cock is open. Incorrect gas valve adjustment, check correct
setting of gas valve.
- Irregular combustion or noisiness. is can be caused by:
dirty burner, incorrect combustion parameters, intake-
exhaust terminal not correctly installed. Clean the above
components and check correct installation of the terminal,
check correct setting of the gas valve (Off-Set setting) and
correct percentage of CO
2
in fumes.
- Frequent activation of the overtemperature safety ther-
mostat (error 2). is can be caused by lack of water in
the boiler, insufficient water circulation in the system or
blocked circulating pump. Check on the pressure gauge
that values are within the fixed limits. Check that radiator
valves are not all closed and that the circulating pump is
working correctly.
- Trap clogged (error 1). is can be caused by dirt or com-
bustion products inside. By means of the condensate drain
plug check for any residuals of material possibly blocking
the flow of condensate.
- Exchanger blocked (error 1). is can be caused by the
trap being blocked. By means of the condensate drain plug
check for any residuals of material possibly blocking the
flow of condensate.
- Noise due to air in the system (error 10). Check opening of
the cap on the special air valve (see fig. page 16-17). Check
that system pressure and the expansion tank precharge are
within the set limits. e expansion tank precharge value
must be 1.0 bar, and the system pressure between 1 and
1.2 bar.
3.6 Converting the boiler to another type of gas.
If the boiler has to be converted to a different gas type to that
specified on the dataplate, request the relative conversion kit
for quick conversion. Boiler conversion must be carried out
by a qualified technician (e.g. Immergas Technical Assistance
Service).
To convert to another type of gas the following operations
are required:
- replace the nozzle located between the gas pipe and gas/air
mixing sleeve (detail 9 page 23 or detail 12 page 24);
- adjust (if necessary) maximum boiler heat output;
- check the value of CO
2
In the fumes with the boiler at
max. output with respect to the following table;
- check the value of CO
2
in the fumes with boiler at min.
output with respect to the following table;
- seal the gas flow regulation devices (if the settings are
modified);
- after completing conversion, apply the sticker, included
in the conversion kit, near the dataplate. Using an indel-
ible marker pen, cancel the data relative to the old type of
gas.
ese adjustments must be made with reference to the type
of gas used, following that given in the table on page 32.
3.7 Checks following conversion to another type of gas.
After ensuring conversion was carried out with a nozzle of
suitable diameter for the type of gas used and the settings
were made at the correct pressure, check that:
- the burner flame is not too high or low and is stable (does
not detach from burner);
- the pressure testers used for calibration are perfectly closed
and there are no leaks in the gas circuit.
N.B.:
All boiler adjustment operations must be carried out by
a qualified technician (e.g. Immergas Assistance Service).
Burner adjustment must be carried out using a differential
digital-type pressure gauge (with scale in tenths of mm or
Pascal), connected to the gas valve (P3 - P2) outlet pressure
point and on the pressure tester located above the sealed
chamber (detail 28 page 16-17), respecting the pressure value
given in the table on page 32 for the type of gas for which
the boiler is arranged.
3.8 Possible adjustments.
• Rated heat output check.
e boiler rated heat output is correlated to the length of
the air intake and fume exhaust pipes. It decreases slightly in
proportion to the increase in pipe length. e boiler leaves the
factory adjusted for minimum pipe length (1 m), therefore
in case of max. pipe extension, it is necessary to check the
“p” values at the ends of the Venturi and gas pressure at the
nozzle after at least 5 minutes of burner operation, when
the air intake and exhaust gas temperatures have stabilized.
e trimmer (9 page 28) inserted in the electronic adjust-
ment card must be operated in order to adjust the rated heat
output according to the values given in the table on page 32.
Use differential manometers connected to the “p” pressure
points on the Venturi and nozzle gas pressure as specified in
the chapter “Air/gas ratio adjustment”.
is adjustment is not necessary during the preliminary
check, as the boiler is factory-set with the correct air/gas
ratio.
However, it may be necessary during extraordinary main-
tenance, with replacement of air and gas circuit compo-
nents.
After any adjustments:
- ensure that the pressure testers used for calibration are
perfectly closed and there are no leaks in the gas circuit;
- seal the gas flow regulation devices (if the settings are
modified).
24
INST
ALLER
USER
TECHNICIAN
25
INST
ALLER
USER
TECHNICIAN