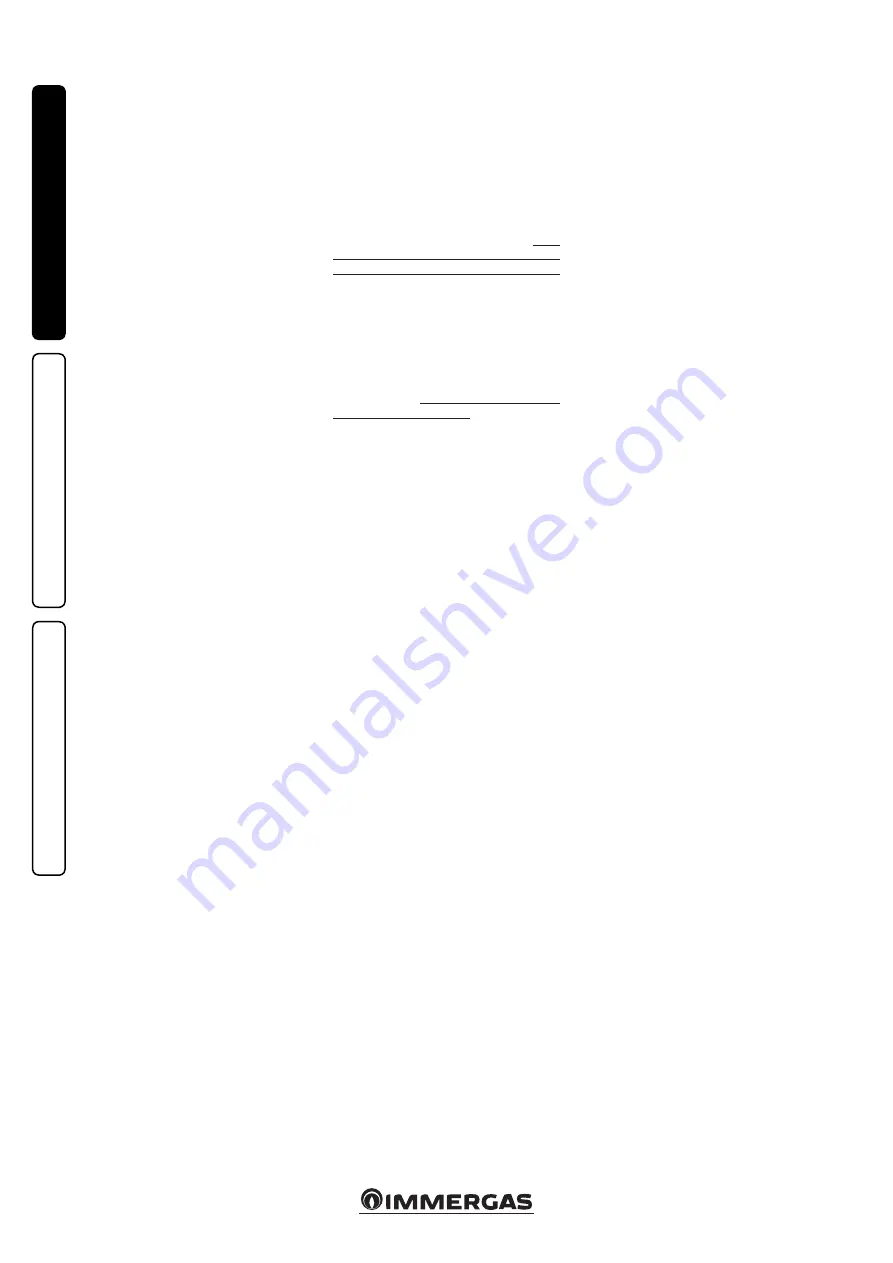
8
INS
TALLER
US
ER
MAINTEN
AN
CE TECHNI
CI
AN
1.9 VENTILATION OF THE ROOMS.
In the room in which the boiler is installed it is
necessary that at least as much air flows as that
requested for by normal combustion of the gas
and ventilation of the room. Natural air flow must
take place directly through:
- permanent openings in the walls of the room
to be ventilated that lead towards the outside;
- ventilation pipes, individual or branched type.
The air used for ventilation must be withdrawn
directly from outside, in an area away from sourc-
es of pollution. Natural air flow is also allowed
indirectly by air intake from adjoining rooms.
For further information relative to ventilation of
the rooms follow that envisioned in the current
technical regulation.
Evacuation of foul air.
In the rooms where the
gas appliances are installed it may also be neces-
sary, as well as the intake of combustion agent air,
to evacuate foul air, with consequent intake of a
further equal amount of clean air. This must be
realised respecting the provisions of the technical
regulations in force.
1.10 EVACUATION OF COMBUSTION
PRODUCTS: SMOKE DUCTS AND
BRANCHED MULTIPLE FLUES.
The European regulation 813/2013 provides that
this boiler can be installed only to replace sim-
ilar equipment connected to existing branched
multiple flues.
Connection to branched multiple flues.
Fitting the appliances to a branched multiple flues
takes place by means of flue ducts.
In the event of fittings with pre-existing flues,
these must be in safe and efficient status and per-
fectly clean because the detachment of any waste
from the walls during functioning, could block
the passage of flue gases, thus causing extremely
dangerous situations for the user.
The flue ducts must be connected to the chimney
or flue in the same room in which the appliance
is installed or, at most, in the adjoining room and
must comply with the requirements indicated by
the current technical regulations.
1.11 FLUE GAS CONTROL DEVICE.
Important:
it is prohibited to put the fumes
exhaust control device out of order voluntarily.
Every piece of this device must be replaced using
original spare parts if they have deteriorated. In
the case of repeated interventions of the fumes
exhaust control device, check the fumes exhaust
flue and the ventilation of the room in which the
boiler is located.
For the right functioning of the Nike Star, the
pipe the boiler is connected to is to have a mini-
mum vacuum equivalent to the fan assisted of 1
meter of vertical pipe with a diameter of 130 mm.
1.12 SYSTEM FILLING.
Once the boiler is connected, proceed with
system filling via the filling cock
(Fig. 7 Fig.
9)
. Filling is performed at low speed to ensure
release of air bubbles in the water via the boiler
and central heating system vents.
The boiler has a built-in automatic venting valve
on the circulator.
Check if the cap is loose (Ref.
15 Fig.9 and Ref. 13 Fig. 12).
Open the radiator
vent valves.
Close radiator vent valves when only water
escapes from them.
Close the filling valve when the boiler pressure
gauge indicates approx. 1.2 bar.
1.13 GAS SYSTEM START-UP.
To start up the system, refer to the technical
standard in force: In particular, for new gas
systems:
- open windows and doors;
- avoid presence of sparks or naked flames;
- bleed all air from pipelines;
- Check that the internal system is properly
sealed according to technical regulations in
force;
1.14 BOILER START UP (IGNITION).
To commission the boiler (the operations listed
below must only be performed by a qualified firm
and without any unauthorised persons):
- Check that the internal system is properly
sealed according to technical regulations in
force;
- ensure that the type of gas used corresponds to
boiler settings;
- check that there are no external factors that
may cause the formation of fuel pockets;
- switch the boiler on and ensure correct ignition;
- make sure that the gas flow rate and relevant
pressure values comply with those given in the
manual
(Par. 3.17)
;
- check the correct ventilation of the rooms;
- check the existing draught during normal
functioning of the appliance, e.g. a draught
gauge positioned at the exit of the appliance
combustion products;
- check that there is no backflow of combustion
products into the room, even during function-
ing of fans;
- ensure that the safety device is engaged in the
event of gas supply failure and check activation
time;
- check activation of the main switch located
upstream from the boiler.
The boiler must not be started up even if only
one of the checks should be negative.