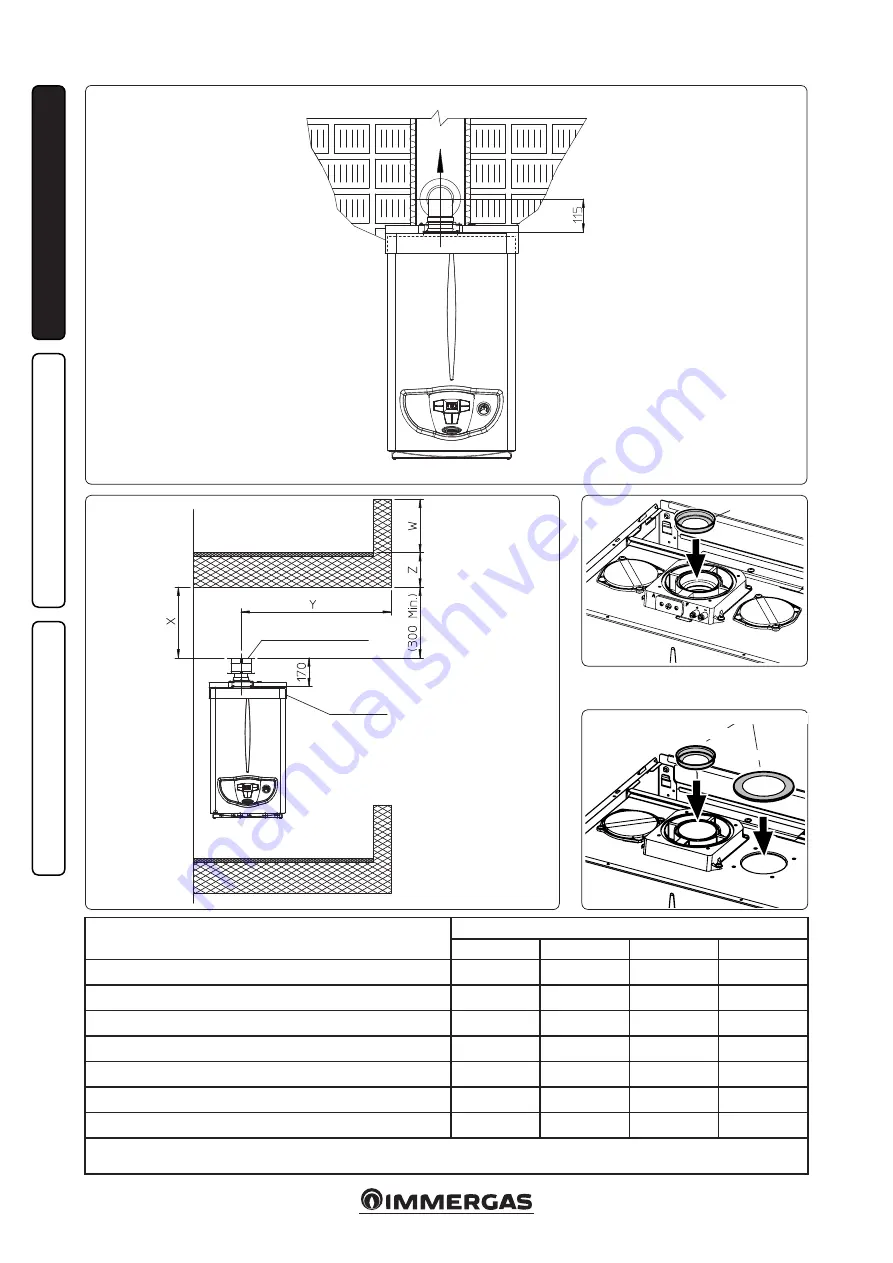
10
1-9
1-8
1-10
1-11
INS
TALLER
US
ER
MAINTEN
AN
CE TECHNI
CI
AN
Type of installation
(duct length in metres)
Diaphragm
Ø 38
Ø 40
Ø 42,5
WITHOUT
Ø 60/100 horizontal concentric kit
From 0 to 0.5
From 0.5 to 1.5
-
From 1.5 to 3.0
Ø 60/100 vertical concentric kit
From 0 to 2.2
From 2.2 to 3.7
-
From 3.7 to 4.7
Ø 80/125 horizontal concentric kit
From 0 to 0.5
From 0.5 to 4.6
-
From 4.6 to 7.4
Ø 80/125 vertical concentric kit
From 0 to 5.4
From 5.4 to 9.5
-
From 9.5 to 12.2
Ø 80 vertical separator kit without bends
*From 0 to 20
*From 20 to 40
**From 0 to 22 ** From 22 to 33
Ø 80 horizontal separator kit with two bend
*From 0 to 16
*From 16 to 35
**From 0 to 17 ** From 17 to 28
Direct intake kit and Ø 80 drain in B
22
configuration
From 0 to 0.5
-
From 0.5 to 15
-
*
These maximum extension values are considered intake with 1 metre drain pipe
** These maximum extension values are considered in draining with 1 metre intake pipe and Ø 47 diaphragm on the intake hole.
VERTICAL TERMINAL KIT
FOR DIRECT DRAINING
INTAKE
COVER KIT
DIAPHRAGM
DIAPHRAGM
Exhaust
Intake
Summary of Contents for MINI EOLO 28 3E
Page 1: ...MINI EOLO 28 3E Instruction and warning booklet IE 1 038767ENG ...
Page 2: ......
Page 28: ...28 3 5 4 4 5 6 6 d d c INSTALLER USER MAINTENANCE TECHNICIAN ...
Page 32: ...32 ...
Page 33: ...33 ...
Page 34: ...34 ...
Page 35: ...35 ...