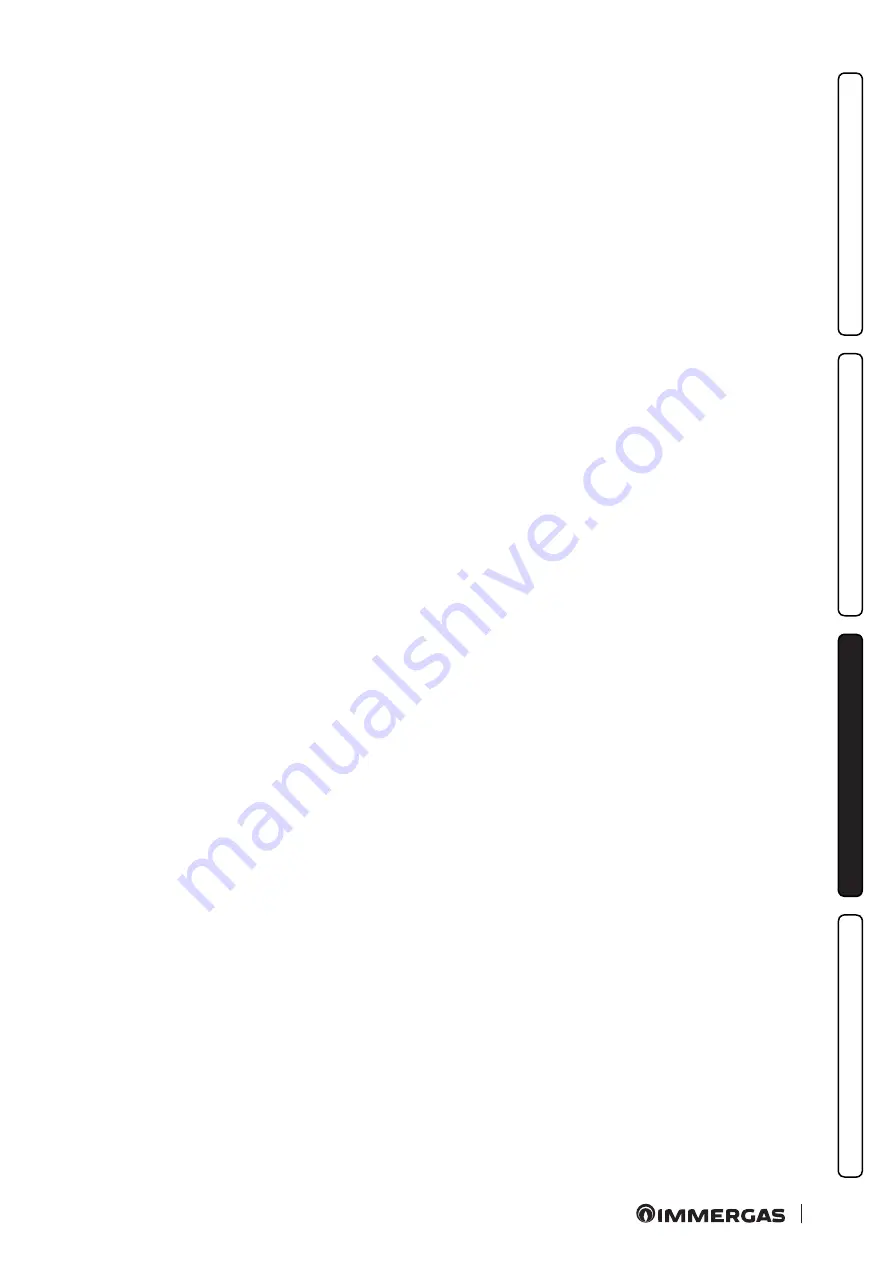
13
INS
TALLER
US
ER
MAINTEN
AN
CE
TECHNI
CI
AN
TECHNI
CAL
D
AT
A
3.2 YEARLY CONTROL AND MAINTENANCE OF THE
STORAGE UNIT.
The following checks and maintenance should be performed at
least once a year.
- Visually check for water leaks or oxidation from/on connections;
- Check visually that the safety and control devices have not been
tampered with and in particular:
- adjustment probes;
- expansion vessel;
- domestic hot water side safety valve;
- Check integrity of the storage tank sacrificial anodes;
- In the case of particularly hard water, decalcification of the stor-
age tank is recommended at least once a year. To perform this
operation the tank must be emptied through the draining valve
and then remove the flange in order to access the inside and use
a plastic or wooden spatula to remove the most resistant deposits
and then clean and rinse with a jet of water.
- During the cleaning phase pay particular attention not to damage
the internal protection of the tank.
- On completion of the operation, re-mount the flange by applying
the gasket (replace it with a new one if it is damaged), close the
draining valve and fill the tank, checking that there are no leaks
from the flange or the valve.