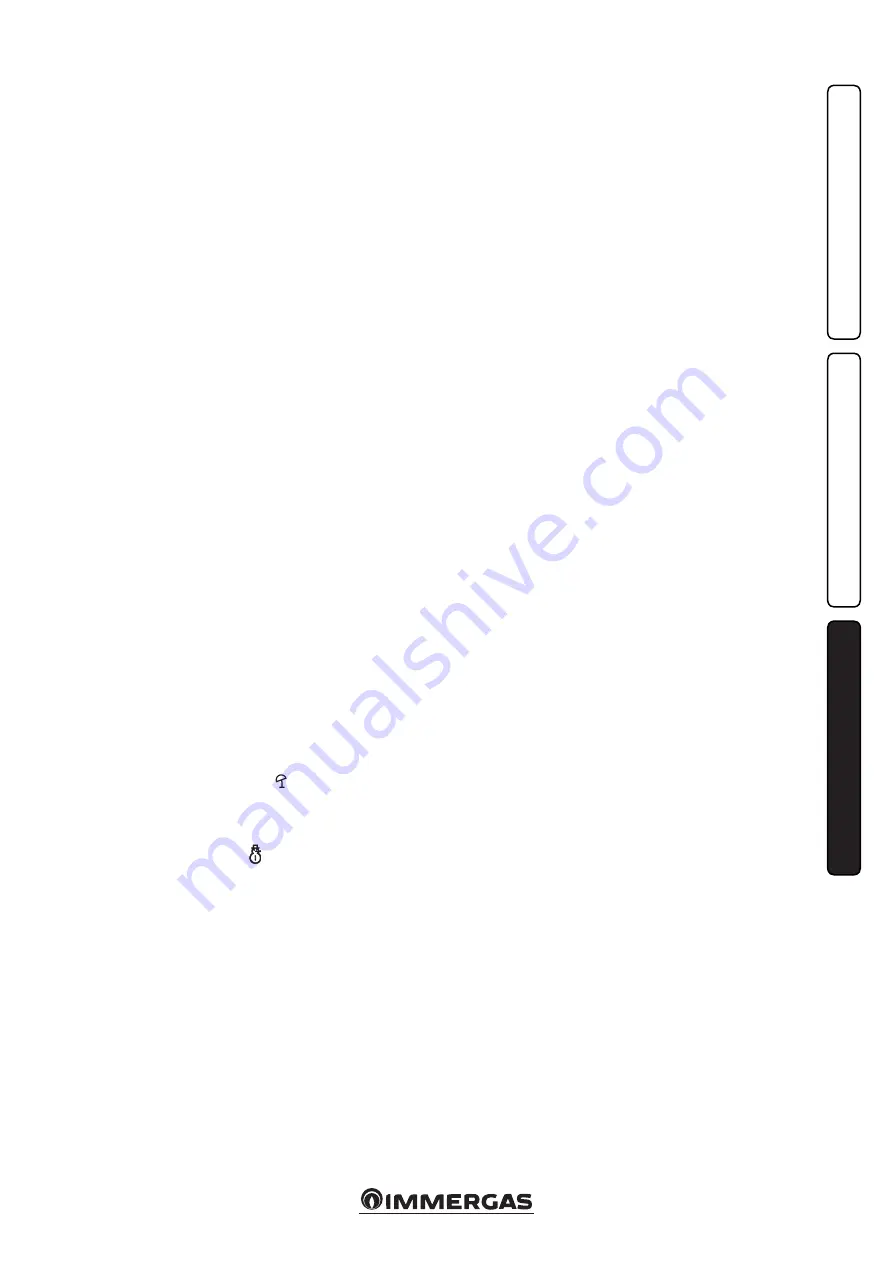
27
INS
TALLER
US
ER
MAINTEN
AN
CE TECHNI
CI
AN
3.8 "CHIMNEY SWEEP” FUNCTION.
When activated, this function forces the boiler
at max. output (P06) for 15 minutes.
In this state all adjustments are excluded and
only the temperature safety thermostat and the
limit thermostat remain active. To activate the
chimney sweep function, press the Reset key
for at least 5 seconds. Its activation is indicated
by the flashing symbols (8 and 11 Fig. 2-1). This
function allows the technician to check the com-
bustion parameters. After the checks disable the
function, switching the boiler off and then on
again or simply by pressing the reset button for
about 5 seconds (1 Fig. 2-1).
The maximum heating power can be set to P06
and P05 by pressing buttons (3 or 4). The power
can be adjusted by one percentage point by
pressing buttons (5 or 6).
If you wish to run the "chimney sweep" function
in D.H.W., open a D.H.W. tap after switching
the burner on.
The maximum boiler power can be set to 0% and
100% by pressing buttons (3 or 4). The power can
be adjusted by one percentage point by pressing
buttons (5 or 6).
Note:
the display of the boiler power percentage
alternates with the display of the temperature
read by the flow probe.
3.9 HEATING TIMER.
The boiler has an electronic timing device that
prevents the burner from igniting too often in
the heating phase. The boiler is supplied as per
standard with a timer adjusted at 3 minutes. To
adjust the timer values, follow instructions for
parameter settings by selecting parameter (P07)
and set it with one of the values indicated on the
relative table.
3.10 THREE-WAY ANTI-BLOCK SYSTEM.
The boiler is supplied with a function that ac-
tivates the motorised three-way unit every 24
hours, carrying out a complete cycle in order
to reduce the risk of three-way block due to
prolonged inactivity.
3.11 PUMP ANTI-BLOCK FUNCTION.
In the “summer” functioning mode ( ) the
boiler has a function that starts the pump at least
once every 24 hours for 30 seconds in order to
reduce the risk of the pump becoming blocked
due to prolonged inactivity.
In the “winter” functioning mode ( ) the boiler
has a function that makes the pump start at least
once every 3 hours for 30 seconds.
3.12 RADIATORS ANTIFREEZE
FUNCTION.
If the system return water is below 4°C, the boiler
starts up until reaching 42°C.
3.13 P.C.B. PERIODICAL SELF-CHECK.
During functioning in central heating mode or
with boiler in standby, the function activates
every 18 hours after the last boiler check/power
supply. In case of functioning in domestic hot
water mode the self-check starts within 10 minu-
tes after the end of the withdrawing in progress,
for duration of approx. 10 seconds.
Note:
during self-check, the boiler remains off,
including signalling.
Summary of Contents for EOLO MYTHOS DOM 10 1E
Page 1: ...EOLO MYTHOS DOM 10 18 24 1E Instructions and warning book 1 041321ENG ...
Page 2: ......
Page 34: ...34 ...
Page 35: ...35 ...