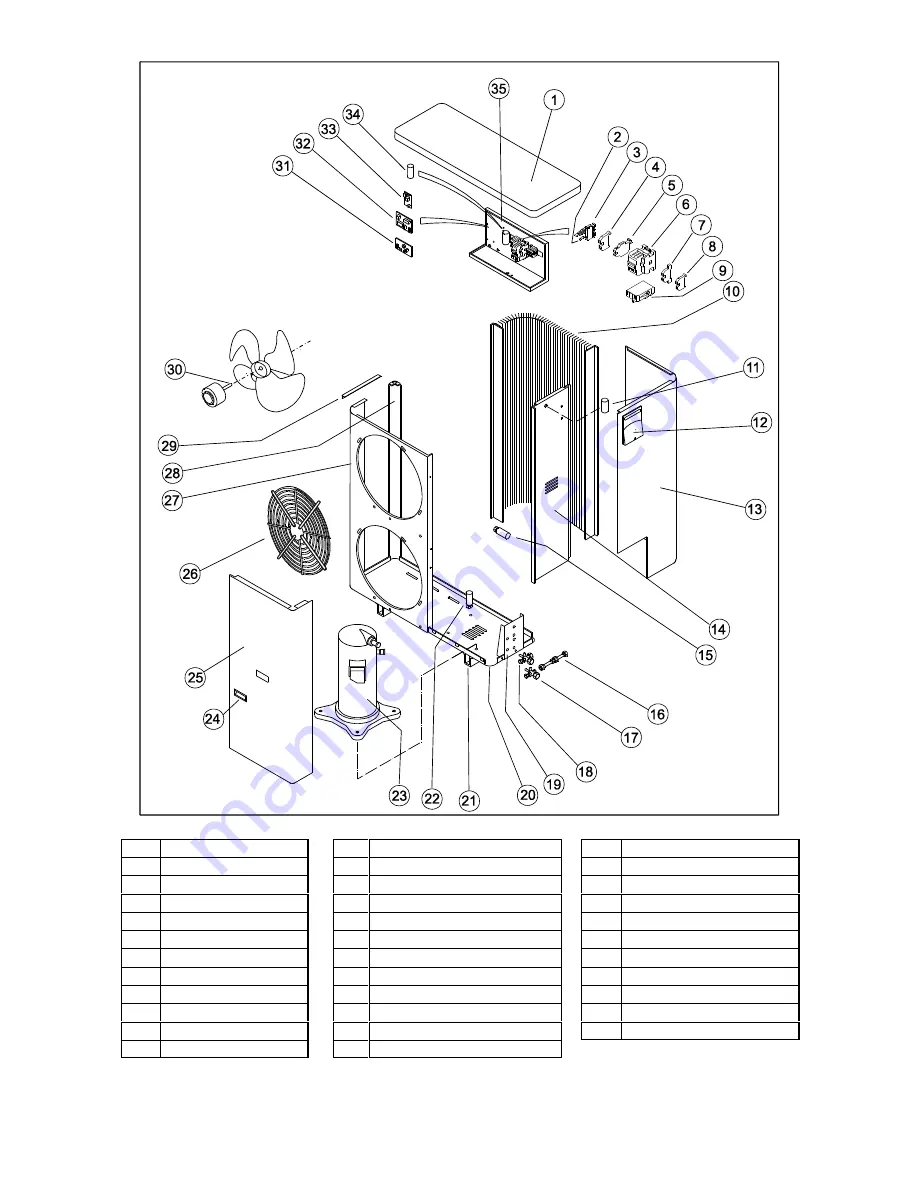
-38-
MCU(+) 130 - 200 COMPONENT IDENTIFICATION
1
Lid
13
Rear access panel
25
Front access panel
2
Fuse terminal
14
Bulkhead panel
26
Fan guard
3
Fuse
15
HP switch (manual: Accessory)
27
Fascia panel
4
Terminal (screw - screw)
16
Expansion assembly
28
Corner panel
5
Terminal (4 way)
17
Service valve (expansion)
29
Support bracket
6
Contactor
18
Service valve (suction)
30
Fan motor assembly
7
Earth terminal
19
Valve panel
31
Head pressure control pcb
8
End clamp
20
Base
32
Power board (MHPUE)
9
Overload
21
Mounting foot
33
3 minute timer pcb
10
Heat exchanger
22
LP switch
34
Compressor capacitor (1Ph)
11
Fan capacitor
23
Compressor
35
Electrics box
12
Mains terminal cover
24
Handle
Heronhill - for all your IMI requirements
Tel: 01823 665660
www.heronhill.co.uk
Fax: 01823 665807