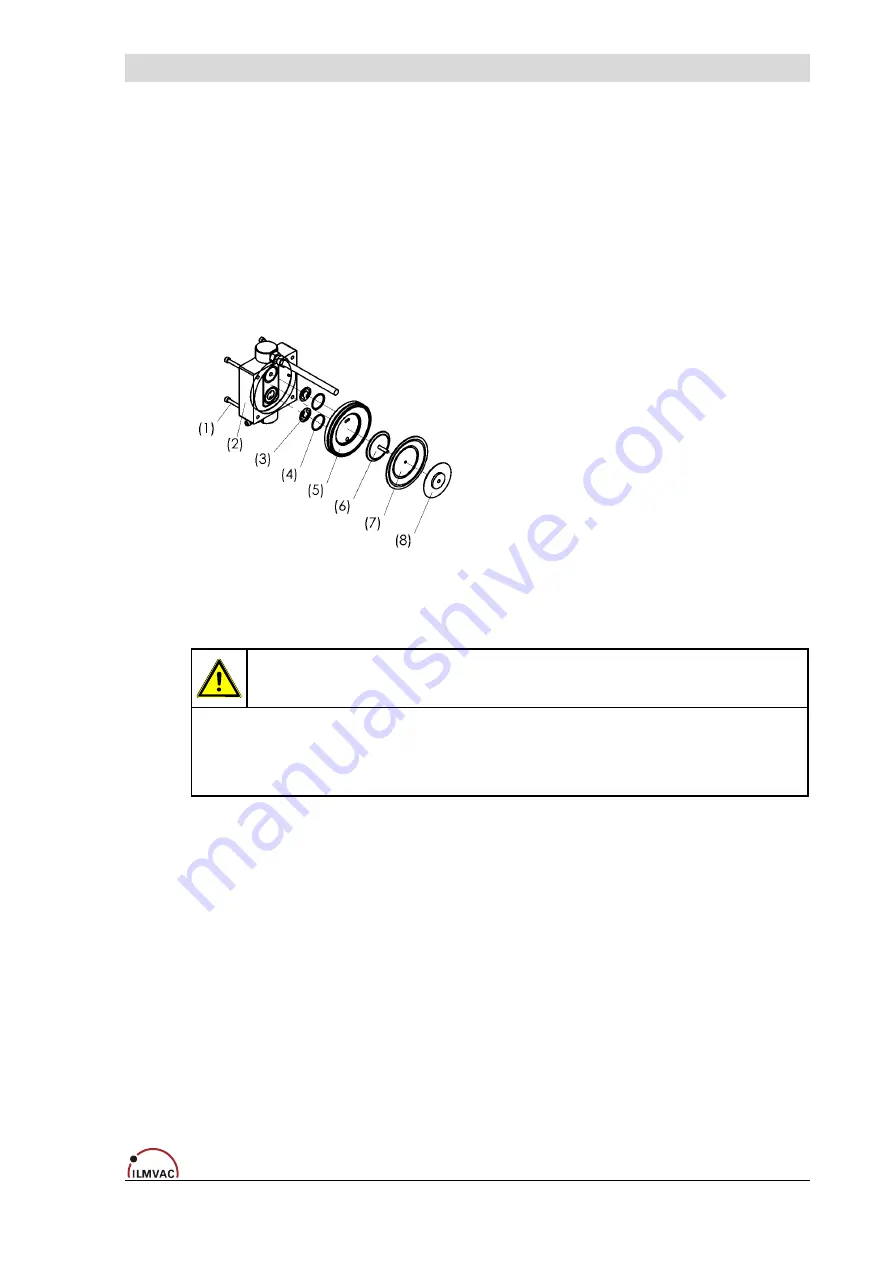
Maintenance and Servicing
6.2.1 Disassembly
1. Disconnect the power supply and ensure that it cannot be switched on again.
2. Remove four machine screws
(1)
from each connection head with an Allan key, size 4.
3. Lift off the connection head
(2)
and the pump head
(5)
. The valves
(3)
, o-rings
(4)
and di-
aphragm
(7)
are now freely exposed.
4. Loosen the diaphragm
(7)
at the strain washer
(6)
by turning the size 3 pin type face
wrench anticlockwise.
5. Clean the valves
(3)
, the pump head
(5)
and the diaphragm
(7)
with a soft cloth and ace-
tone.
6. Check that the drive is in good working order.
Fig. 4 Disassembly, assembly
WARNING !
Renew defective parts, if necessary ! Wear protective gloves!
Parts must be renewed at the intervals stated in this Operating Manual or as speci-
fied by the user internally.
Do not clean with compressed air !
6.2.2
Assembly
(Fig. 4)
1. Use the size 3 pin-type face wrench to tighten the pressure disc
(8)
, the diaphragm
(7)
and the strain washer
(6)
with the correct torque of 2 - 4 Nm.
2. Bring the connecting rod
(see fig. 5)
and the diaphragm
(7)
into the central position.
3. Replace the pump head
(5)
.
4. Insert the valves
(3)
and the o-rings
(4)
.
Ensure that they are lying completely flat. Do not insert the burred side facing the sealing
surface. Align the connection head flush with the pin.
5. Tighten the four machine screws
(1)
symmetrically with a torque of 3 to 4 Nm.
4000732
15