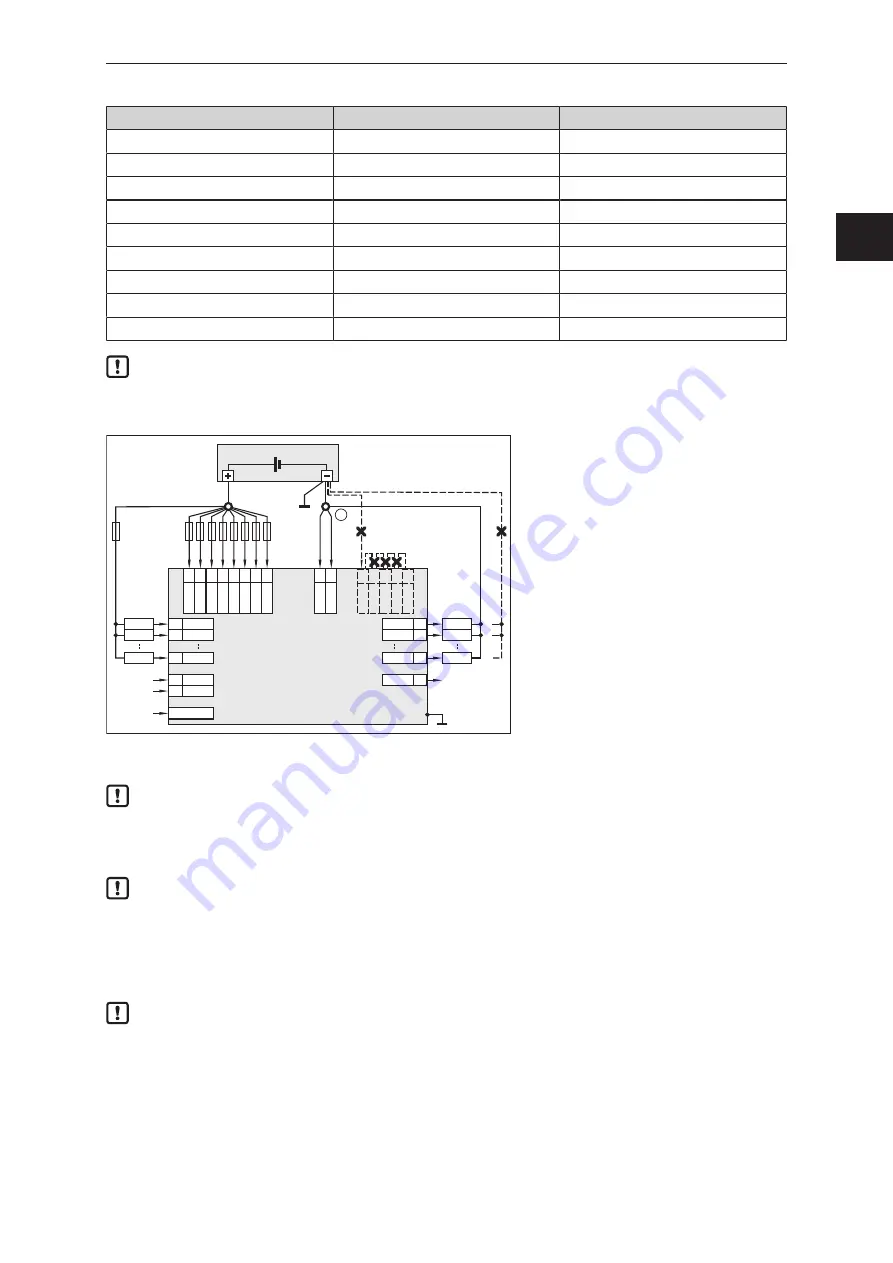
CR720S CR721S
9
Connection
Nominal value fuse
Required triggering characteristics
VBB
15
2 A
T
fuse
≤ 120 s at max. 6.25 A
VBB
30
2 A
T
fuse
≤ 120 s at max. 6.25 A
VBB
0
15 A
-
VBB
1
≤ 15 A
-
VBB
2
≤ 15 A
-
VBB
3
≤ 15 A
-
VBB
4
(only with CR721S)
≤ 15 A
-
VBB
5
(only with CR721S)
≤ 15 A
-
Inputs / input groups
2 A
T
fuse
≤ 120 s at max. 6.25 A
All supply lines of the inputs can be protected within the input groups.
6.5 Laying of the supply and signal cables
supply
output
nn
output
nn
output
nn
controller
VBB
30
nn
VBB
15
nn
VBB
0
nn
VBB
1
nn
VBB
2
nn
VBB
3
nn
VBB
4
nn
VBB
5
nn
GND
SYS
nn
GND
1...4
GND
SYS
GND
RES
GND
ANA
GND
O
VA
GND
1...4
nn
input
nn
input
nn
GND
ANA
nn
nn
input
nn
sensor
sensor
sensor
load
load
load
GND
OVA
Shield
nn
nn
nn
nn
nn
nn
GND
RES
RESET-COM
1
Fig. 4: Connection of the supply and signal cables (X = not permitted), example CR721S
1:
GND star point
Bridging of connections in the connectors is not permitted.
RESET-COM is a service input (see programming manual).
u
For the operation of the controller, connect RESET-COM to the GND star point
①
.
Faulty laying of the supply and signal cables
w
Deterioration of EMC may occur
u
Lay all supply and signal cables separately to maintain application/EMC integrity
u
Connect supply and ground cables to the controller and the sensors/actuators via the
respective common star point.
If a prewired connection cable is used, remove the cores with unused signal inputs and outputs.
Provide the unconnected signal inputs with sealing of the individual cores. Unconnected cores or
core loops are not permitted.
In case of signal failures, operate inputs with shielded cables. Connect the shields to the shield
connection on one side.
GB