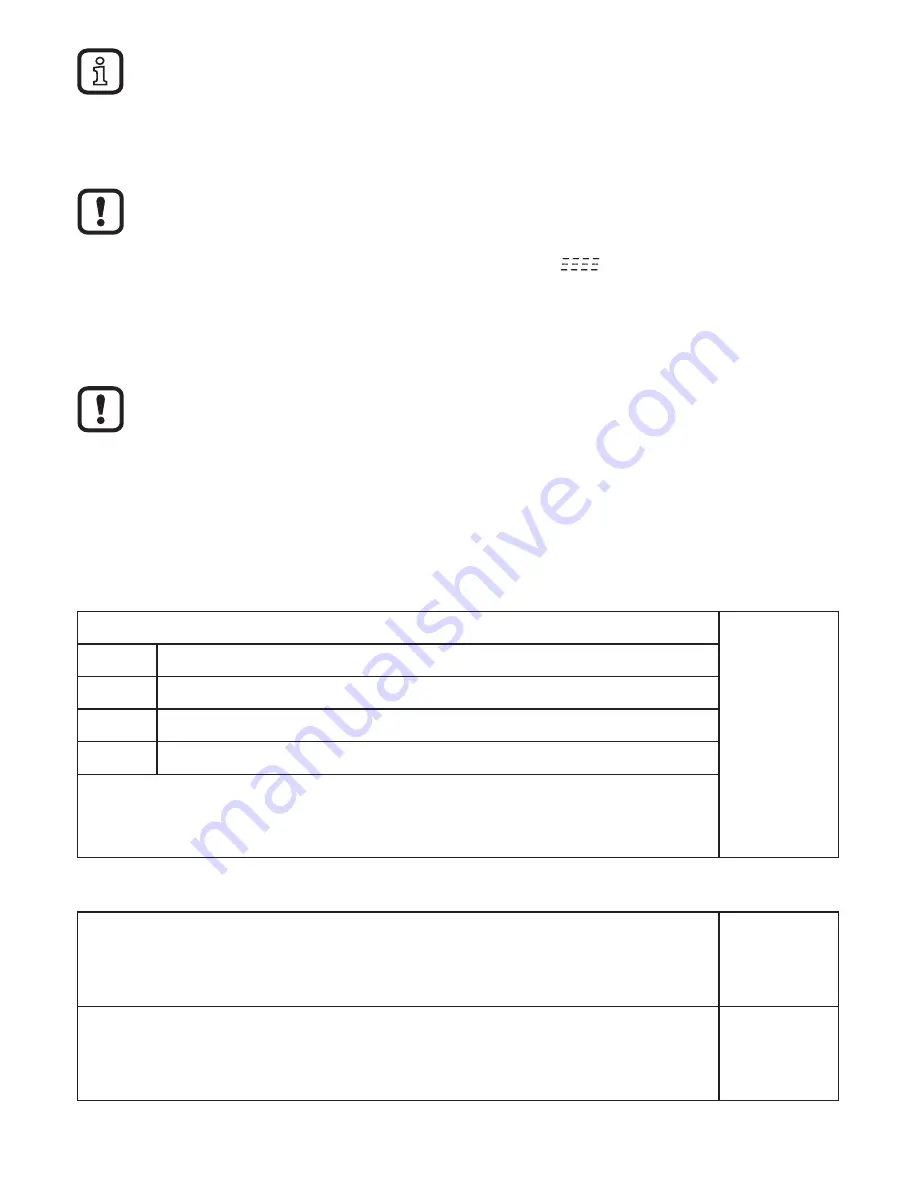
26
The position of the overflow prevention OP can be determined by calling up
the parameter [OP]. Note the offset if necessary.
The current level is to be determined manually since the unit is not yet
ready for operation before the adjustment.
When the overflow prevention is activated ([OP] = [value ...]), an
adjustment [cOP] must be carried out each time:
• [MEdI] or [OP] were changed. In this case
is displayed.
• The installation position (height, orientation) was changed.
• The connection between the sensor and the tank ground (e.g. cable
length) was changed.
With deactivated overflow prevention [OP] = [OFF] or [MEdI] = [Auto]:
To apply the basic settings and to adapt to the medium
and
installation
environment the unit has to be reinitialised when installed.
►
Switch the operating voltage off and on again.
10.3 Setting of output signals
10.3.1 Set output function [oux] for OUTx
►
Select [oux] and adjust the switching function:
ou1
...
ou4
[Hno] = hysteresis function / normally open
[Hnc] = hysteresis function / normally closed
[Fno] = window function / normally open
[Fnc] = window function / normally closed
If the switching output is used as an overflow prevention, the setting [oux]
= [Hnc] (NC function) is recommended. The principle of normally closed
operation ensures that wire break or cable break is also detected.
10.3.2 Define the switching limits [SPx] / [rPx] (hysteresis function)
►
Make sure that the function [Hno] or [Hnc] is set for [oux].
►
Set [SPx] first, then [rPx].
►
Select [SPx] and set the value at which the output is set.
SP1
...
SP4
►
Select [rPx] and set the value at which the output resets.
rP1
...
rP4