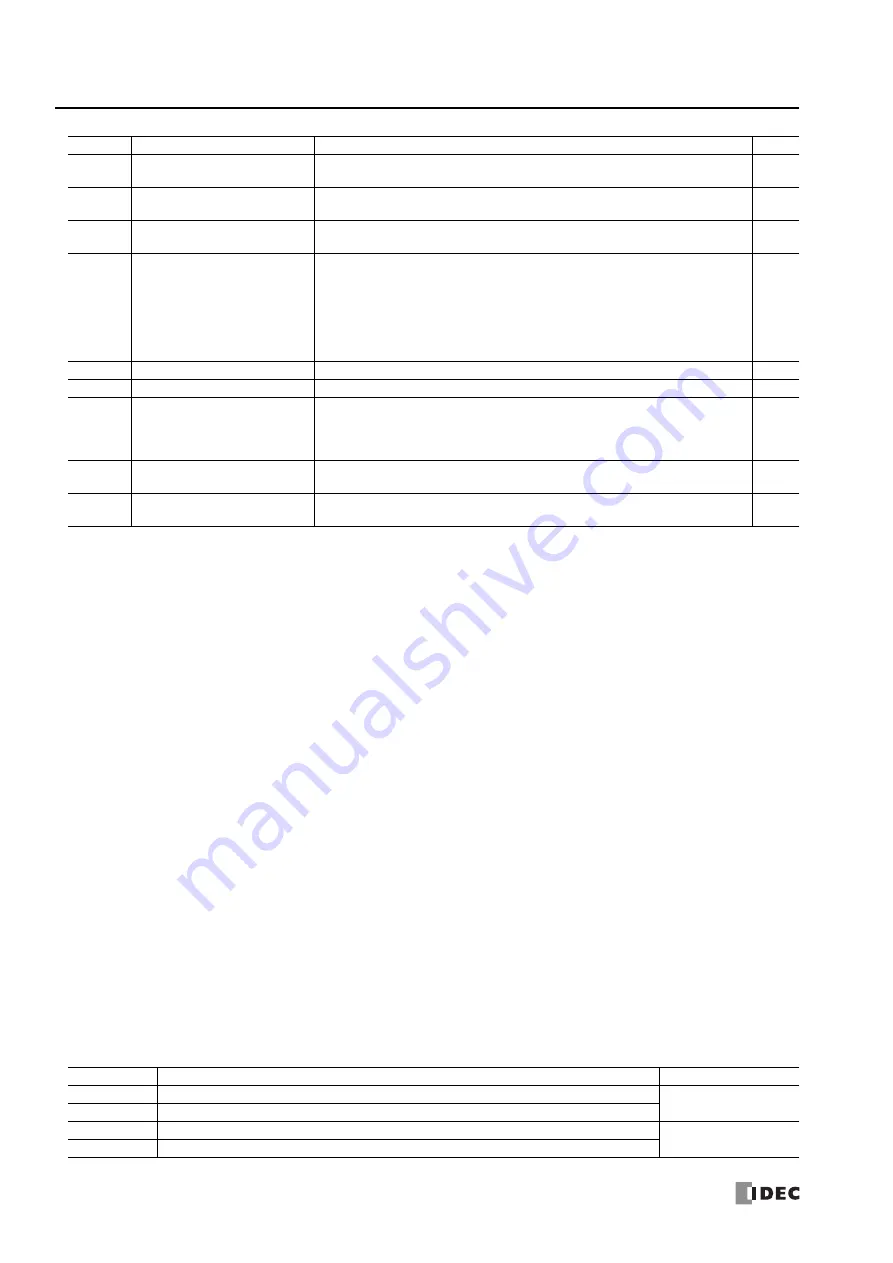
14:
PID
I
NSTRUCTION
14
‐
4
FC5A
M
ICRO
S
MART
U
SER
’
S
M
ANUAL
FC9Y
‐
B1273
Note:
The
value
stored
in
the
data
register
designated
by
S1+3
(operation
mode)
is
checked
only
when
the
start
input
for
the
PID
instruction
is
turned
on.
Values
in
all
other
control
registers
are
refreshed
in
every
scan.
S1+0 Process
Variable
(after
conversion)
When
the
linear
conversion
is
enabled
(S1+4
set
to
1
or
3),
the
data
register
designated
by
S1+0
stores
the
linear
conver
‐
sion
result
of
the
process
variable
(S4).
The
process
variable
(S1+0)
takes
a
value
between
the
linear
conversion
minimum
value
(S1+6)
and
the
linear
conversion
maximum
value
(S1+5).
When
the
linear
conversion
is
disabled
(S1+4
is
set
to
0
or
2),
the
data
register
designated
by
S1+0
stores
the
same
value
as
the
process
variable
(S4).
S1+1 Output
Manipulated
Variable
While
the
PID
action
is
in
progress,
the
data
register
designated
by
S1+1
holds
0
through
100
read
from
the
manipulated
variable,
–32768
through
32767,
stored
in
the
data
register
designated
by
D1,
omitting
values
less
than
0
and
greater
than
100.
The
percent
value
in
S1+1
determines
the
ON
duration
of
the
control
output
(S2+6)
in
proportion
to
the
control
period
(S1+13).
While
manual
mode
is
enabled
with
the
auto/manual
mode
control
relay
(S2+1)
set
to
on,
S1+1
stores
0
through
100
read
from
the
manual
mode
output
manipulated
variable
(S1+18).
While
auto
tuning
(AT)
is
in
progress,
S1+1
stores
0
through
100
read
from
the
AT
output
manipulated
variable
(S1+22).
S1+2 Operating
Status
The
data
register
designated
by
S1+2
stores
the
operating
or
error
status
of
the
PID
instruction.
Status
codes
1X
through
6X
contain
the
time
elapsed
after
starting
auto
tuning
or
PID
action.
X
changes
from
0
through
9
in
10
‐
minute
increments
to
represent
0
through
90
minutes.
The
time
code
remains
9
after
90
minutes
has
elapsed.
When
the
operation
mode
(S1+3)
is
set
to
1
(AT+PID),
the
time
code
is
reset
to
0
at
the
transition
from
AT
to
PID.
Status
codes
100
and
above
indicate
an
error,
stopping
the
auto
tuning
or
PID
action.
When
these
errors
occur,
a
user
program
execution
error
will
result,
turning
on
the
ERR
LED
and
special
internal
relay
M8004
(user
program
execution
error).
To
continue
operation,
enter
correct
parameters
and
turn
on
the
start
input
for
the
PID
instruction.
S1+18
Manual
mode
output
manipulated
variable
0
to
100
(
101
designates
100)
R/W
S1+19
AT
sampling
period
1
to
10000
(0.01
sec
to
100.00
sec)
0
designates
0.01
sec,
10001
designates
100.00
sec
R/W
S1+20
AT
control
period
1
to
500
(0.1
sec
to
50.0
sec)
0
designates
0.1
sec,
501
designates
50.0
sec
R/W
S1+21
AT
set
point
When
S1+4
(control
mode)
=
0
or
2:
0
to
4095
(
4096
designates
4095)
0
to
50000
(
50001
designates
50000)
When
S1+4
(control
mode)
=
1
or
3:
Linear
conversion
min.
AT
set
point
Linear
conversion
max.
When
S1+21
<
S1+6
(linear
conversion
min.),
S1+6
becomes
AT
set
point.
When
S1+21
>
S1+5
(linear
conversion
max.),
S1+5
becomes
AT
set
point.
R/W
S1+22
AT
output
manipulated
variable
0
to
100
(
101
designates
100)
R/W
S1+23
Output
manipulated
variable %
–32768
to
32767
(–327.68%
to
327.67%)
R
S1+24
Output
manipulated
variable
for
analog
output
module
Converted
from
output
manipulated
variable
(S1+1)
depending
on
analog
output
mod
‐
ule
type
0
to
4095
(0%
to
100%)
0
to
50000
(0%
to
100%)
R
S1+25
Proportional
band
offset
value
–100
to
100
(–100%
to
100%)
–101
designates
–100%,
101
designates
100%
R/W
S1+26
Derivative
gain
0
to
100
(0%
to
100%)
101
designates
100%
R/W
Status
Code
Description
Operation
1X
AT
in
progress
AT
is
normal.
2X
AT
completed
5X
PID
action
in
progress
PID
action
is
normal.
6X
PID
set
point
(S3)
is
reached.
Status
code
changes
from
5X
to
6X
once
the
PID
set
point
is
reached.
Device
Function
Description
R/W
Summary of Contents for MICROSmart FC5A Series
Page 1: ...FC5A SERIES FC9Y B1273 1 User s Manual Advanced Volume ...
Page 2: ......
Page 8: ...Preface 6 FC5A MicroSmart User s Manual FC9Y B1273 ...
Page 14: ...TABLE OF CONTENTS vi FC5A MICROSMART USER S MANUAL FC9Y B1273 ...
Page 52: ...4 DATA COMPARISON INSTRUCTIONS 4 10 FC5A MICROSMART USER S MANUAL FC9Y B1273 ...
Page 72: ...5 Binary Arithmetic Instructions 5 20 FC5A MicroSmart User s Manual FC9Y B1273 ...
Page 88: ...7 SHIFT ROTATE INSTRUCTIONS 7 12 FC5A MicroSmart User s Manual FC9Y B1273 ...
Page 112: ...8 DATA CONVERSION INSTRUCTIONS 8 24 FC5A MicroSmart User s Manual FC9Y B1273 ...
Page 138: ...11 PROGRAM BRANCHING INSTRUCTIONS 11 14 FC5A MICROSMART USER S MANUAL FC9Y B1273 ...
Page 178: ...13 PULSE INSTRUCTIONS 13 32 FC5A MICROSMART USER S MANUAL FC9Y B1273 ...
Page 202: ...14 PID INSTRUCTION 14 24 FC5A MICROSMART USER S MANUAL FC9Y B1273 ...
Page 206: ...15 DUAL TEACHING TIMER INSTRUCTIONS 15 4 FC5A MICROSMART USER S MANUAL FC9Y B1273 ...
Page 214: ...16 INTELLIGENT MODULE ACCESS INSTRUCTIONS 16 8 FC5A MICROSMART USER S MANUAL FC9Y B1273 ...
Page 248: ...21 COMPUTER LINK COMMUNICATION 21 4 FC5A MICROSMART USER S MANUAL FC9Y B1273 ...
Page 272: ...23 MODBUS TCP COMMUNICATION 23 10 FC5A MICROSMART USER S MANUAL FC9Y B1273 ...
Page 332: ...25 EXPANSION RS232C RS485 COMMUNICATION 25 16 FC5A MICROSMART USER S MANUAL FC9Y B1273 ...
Page 341: ...NOTE FC5A MICROSMART USER S MANUAL FC9Y B1273 1 ...
Page 342: ...NOTE 2 FC5A MICROSMART USER S MANUAL FC9Y B1273 ...