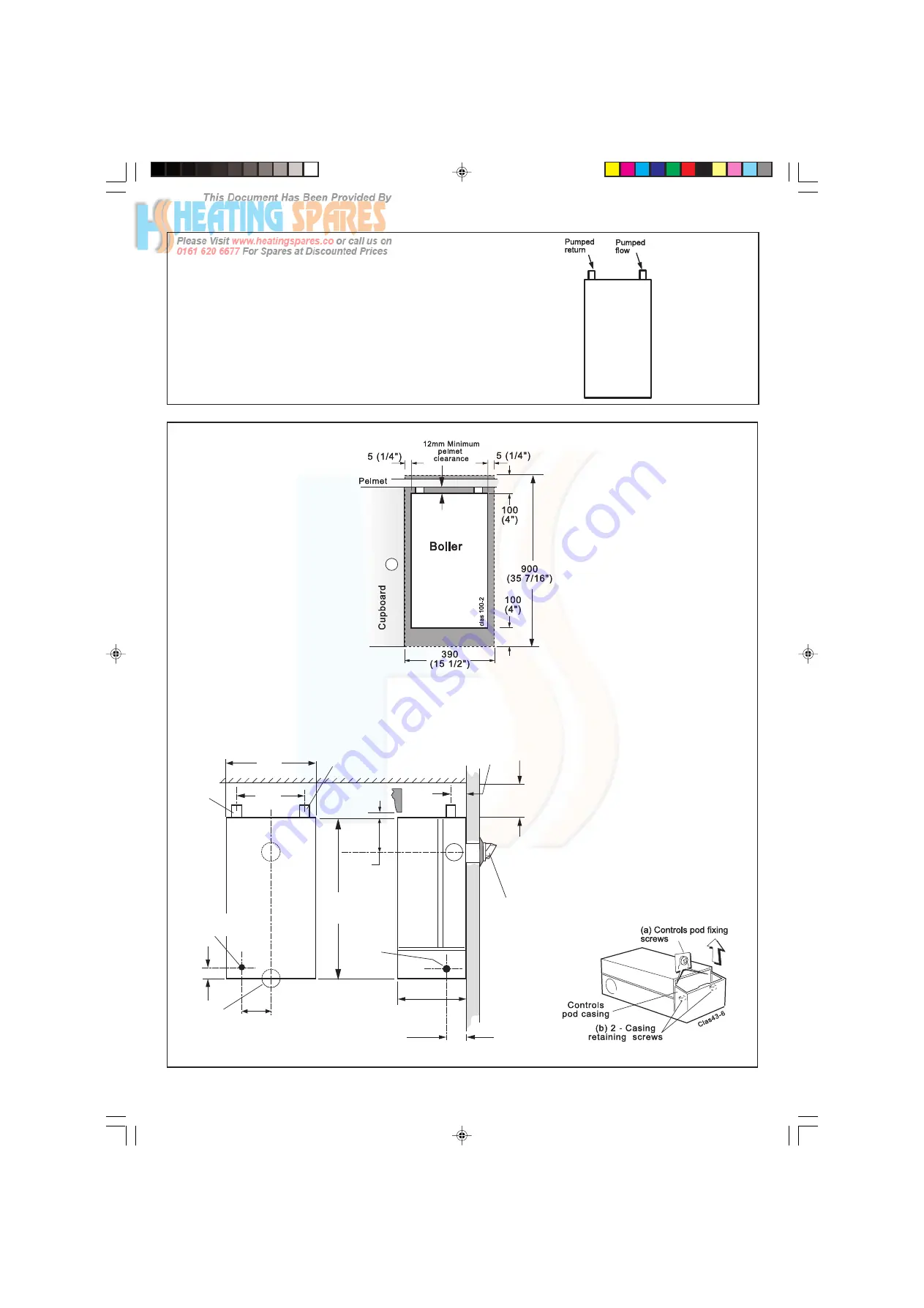
Supplied By www.heating spares.co Tel. 0161 620 6677
Optia FF
-
Installation & Servicing
7
GENERAL
This appliance in NOT suitable for use in a direct
hot water system or for gravity circulation.
FF 70, FF 80 & FF 100 ONLY
must be fitted with the 22mm x 28mm copper sockets,
provided in the Hardware Pack, (or equivalent 22mm x
28mm compression fittings ) and the pumped flow and
return pipes run in 28mm pipe.
1
BOILER WATER CONNECTIONS
The following minimum clearances
must be maintained for operation and
servicing.
Additional space will be required for
installation, depending upon site
conditions.
Side and Rear Flue
a.
Provided that the flue hole is cut
accurately, e.g. with a core drill, the
flue can be installed from inside the
building.
Installation from inside ONLY
b.
If a core boring tool is to be used
inside the building; the space in
which the boiler is to be installed
must be at least wide enough to
accommodate the tool.
c.
If using the Complete Sealed
System Unit then refer to the
instructions packed with the unit for
the necessary clearances.
Pelmet restrictions.
If the ability to fit or remove the
casing during installation and
subsequent servicing is impaired
by pelmets etc. this operation can
be made easier by first removing
the controls pod casing in line
with the following instructions:
a.
Release the controls pod
casing fixing screws (a) 3 full
turns only. Remove the pod by
pulling it forward to disengage
from the keyhole slots.
b.
Undo the 2 screws (b)
retaining casing to the back
panel.
c.
The casing can now be
removed in the direction of the
arrow, first lifting the casing
slightly to disengage the
casing top return from the
back panel. (For this purpose
a minimum clearance of
12mm is required between
the top of the boiler and
pelmet or other similar
obstruction.
Front clearance: 533mm (21")
from the front of the boiler
casing.
Minimum front clearance when
built in to cupboard is 75 mm
(3").
380
(15")
300
(12")
Pumped
return
pipe
Pumped
flow pipe
12 (1/2")
100
(4")
44
(1 3/4")
Flue
terminal
300 (12")
Jacking
screw
Gas
connection
700
(27 1/2")
141
(5 9/16")
Clas 1783
Front View
Side View
133 (5 1/4")
44 (1 3/4")
20 (3/4")
Gas
connection
2 BOILER CLEARANCES
200776-4.pmd
6/23/2005, 10:12 AM
7