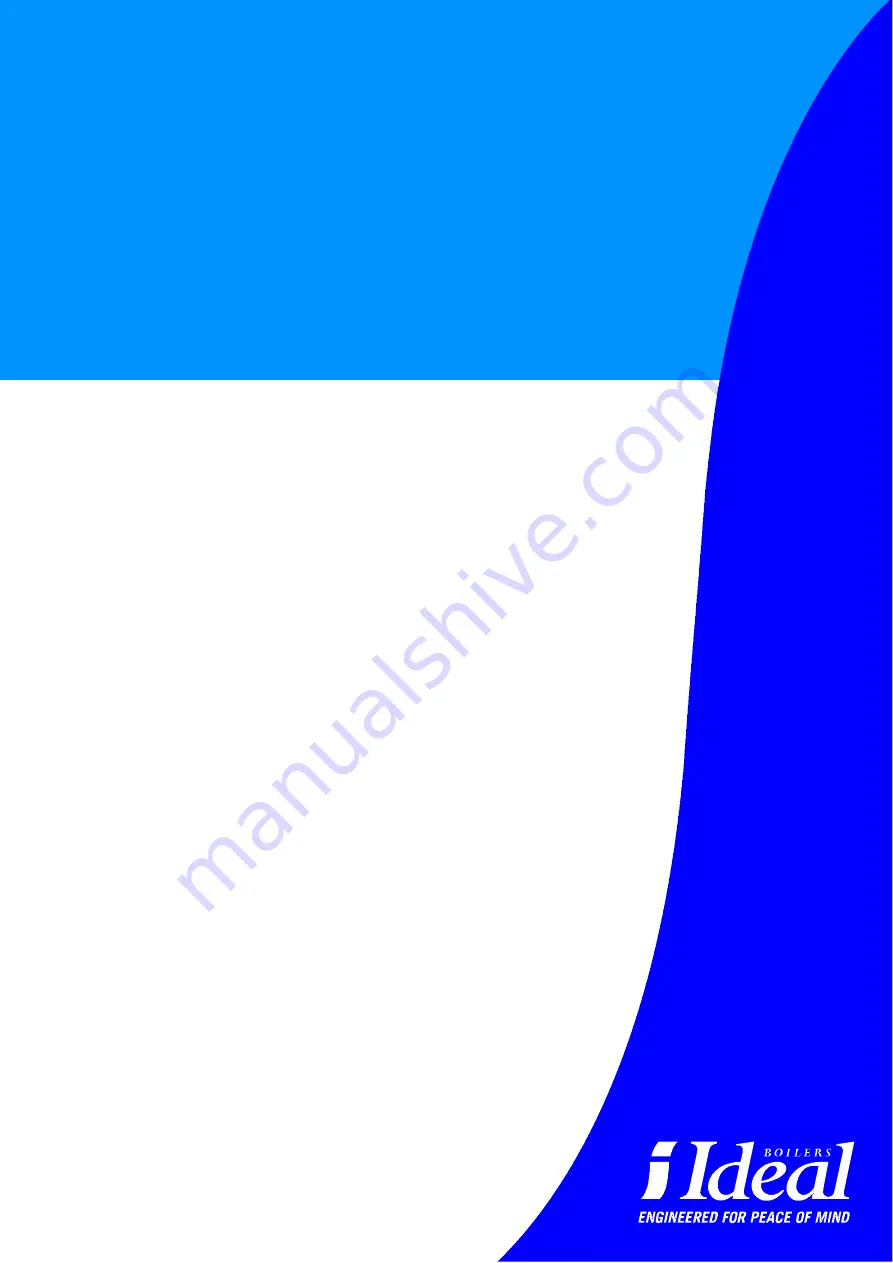
installation and
servicing
mini
Your Ideal installation and servicing guide
C24/C28/C32
S24/S28
When replacing any part of this appliance, use only spare parts that you can be
assured conform to safety and performance specification that we require. Do not use
reconditioned or copy parts that have not been clearly authorised by Ideal Boilers