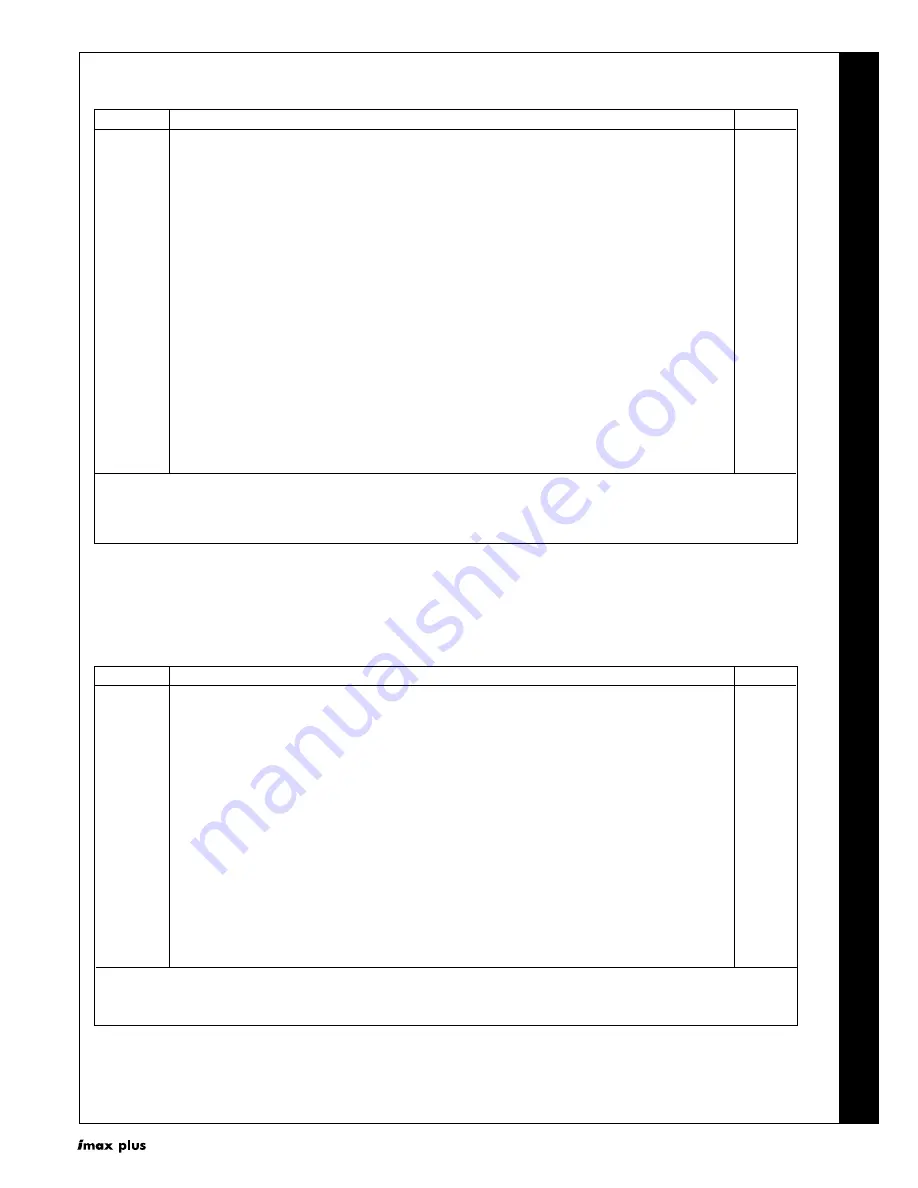
37
-
Installation & Servicing
FAULT FINDING
FAUL
T FINDING FAUL
T FINDING FAUL
T FINDING FAUL
T FINDING FAUL
T FINDING FAUL
T FINDING
46 FAULT FINDING CONTD
Error Code Description
Alarm
L1 4
Local Temperature NTC 1 short circuit
No
L2 4
Local Temperature NTC 2 short circuit
No
L3 4
Local Temperature NTC 3 short circuit
No
L4 4
Local Temperature NTC 4 short circuit
No
L5 4
Local Temperature NTC 5 short circuit
No
L6 4
Local Temperature NTC 6 short circuit
No
L7 4
Local Temperature NTC 7 short circuit
No
L8 4
Local Temperature NTC 8 short circuit
No
L1 3
Local Temperature NTC 1 open circuit
No
L2 3
Local Temperature NTC 2 open circuit
No
L3 3
Local Temperature NTC 3 open circuit
No
L4 3
Local Temperature NTC 4 open circuit
No
L5 3
Local Temperature NTC 5 open circuit
No
L6 3
Local Temperature NTC 6 open circuit
No
L7 3
Local Temperature NTC 7 open circuit
No
L8 3
Local Temperature NTC 8 open circuit
No
E31
Global Flow NTC short circuit
No
E36
Global Flow NTC open circuit
No
E32
Global Return NTC short circuit
No
E37
Global Return NTC open circuit
No
Possible Causes and Solutions
-
The Local Flow Temperature NTC of the aluminium section is defective.
-
The Global Return Temperature NTC is defective.
-
The water circulation through the aluminium section involved is insufficient
ERROR CODES RELATED TO LOCAL OPERATING TEMPERATURE SENSORS
Note.
In the case of more than one NTC failure at the same time, the most important one prevails.
E.g. "E" failures prevail on "L" failures; if "L" codes are equivalent, the code with the lowest first digit prevails; in the case that
the first digits are equivalent, the code with the highest second digit prevails.
Error Code Description
Alarm
L1 2
Local Flow Temperature of Aluminium section 1 > 98ºC
No
L2 2
Local Flow Temperature of Aluminium section 2 > 98ºC
No
L3 2
Local Flow Temperature of Aluminium section 3 > 98ºC
No
L4 2
Local Flow Temperature of Aluminium section 4 > 98ºC
No
L5 2
Local Flow Temperature of Aluminium section 5 > 98ºC
No
L6 2
Local Flow Temperature of Aluminium section 6 > 98ºC
No
L7 2
Local Flow Temperature of Aluminium section 7 > 98ºC
No
L8 2
Local Flow Temperature of Aluminium section 8 > 98ºC
No
L1 1
The difference between the Global Return Temp. and the Local Flow Temp. of Aluminium section 1 is too high
No
L2 1
The difference between the Global Return Temp. and the Local Flow Temp. of Aluminium section 2 is too high
No
L3 1
The difference between the Global Return Temp. and the Local Flow Temp. of Aluminium section 3 is too high
No
L4 1
The difference between the Global Return Temp. and the Local Flow Temp. of Aluminium section 4 is too high
No
L5 1
The difference between the Global Return Temp. and the Local Flow Temp. of Aluminium section 5 is too high
No
L6 1
The difference between the Global Return Temp. and the Local Flow Temp. of Aluminium section 6 is too high
No
L7 1
The difference between the Global Return Temp. and the Local Flow Temp. of Aluminium section 7 is too high
No
L8 1
The difference between the Global Return Temp. and the Local Flow Temp. of Aluminium section 8 is too high
No
Possible Causes and Solutions
As for the above mentioned conditions, they can be due to wiring break, short circuit or failure of the NTC involved, or over
heating of the aluminium section.
ERROR CODES RELATED TO LOCAL OVERHEAT TEMPERATURES