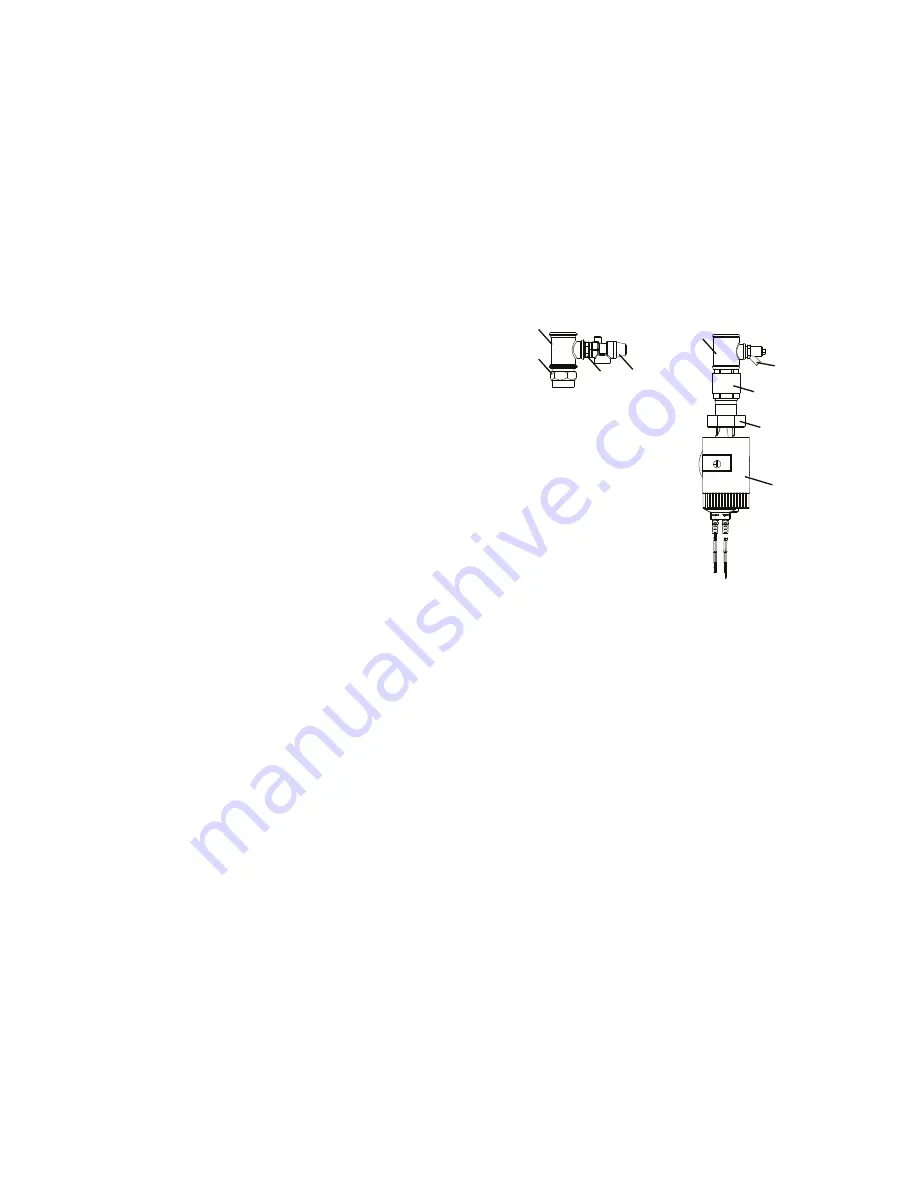
6
EVOMAX - Low Height Frame & Header Kits
3.1 GENERAL
•
Frames: These are provided in a single frame format and are
designed to be bolted side by side up to a maximum of three
frames and must be bolted together using the bolts provide.
•
Water header with built in gas header cradles and mounting
brackets that allow its connection to the frames can be
obtained in DN50 single boiler format, DN 65 two boiler
format or a DN 80 three boiler format.
•
2” gas header with inlet test points
•
All the pumps, associated safety controls, pipes and
fittings required to connect the water and gas header to the
appliances are supplied.
3.2 MAIN WATER HEADERS
The main water header consists of un-insulated water flow and
return pipes incorporating location and frame mounting brackets
sized to cater for the Evomax range of products available for use
with these kits.
The Single unit water header is a DN 50 pipe system with
threaded connections. (Threaded flanges are provided with DN50
Evomax low height Low loss header kit).
The twin water header is a DN 65 pipe system with flanged
connections and is available with the DN65 Evomax low height
Low loss header kit.
The three unit system uses a DN 80 pipe system with flanged
connections and is available with the DN 80 Evomax low height
Low loss header kit.
3.3 GAS HEADER
The gas header consists of a 2” manifold tailored to fit the two
or three unit versions available and is located in the cradle
incorporated in the water header bracket structure.
All the pipe work and connections are provided to connect the
header to the required appliance.
Test points are provided at each end of the 2” gas header. The test
point nearest to the gas inlet is intended to be used as the appliance
inlet pressure point.
3.4 LOW LOSS HEADERS (MIXING HEADERS)
All variants of these kits must be fitted to suitably sized low loss header.
The Evomax low height low loss headers have been designed to
match the lower positioned water headers used in these kits. This has
required the drain point to be moved the lowest side point available.
Note; Bespoke low loss headers may not be able to connect directly
to these headers due to the change in pitch and position of the
header pipe work used in these kits. (See frame fit low loss header)
Ideal recommend:- DN 50 – 209394, DN 65 – 209395,
DN 80 - 252437.
3.5 BOILER SHUNT PUMP
The pumps supplied with these kits are design to provide the
optimum flow around the appliance water circuit ensuring the
maximum flow rates are contain within the design constrains of
the appliance.
It is not recommended to fit additional pumps directly to the
appliance circuit unless they have been designed to ensure the
maximum permissible appliance flow rate is not exceeded.
It is recommended that the appliance circuit pumps are set to
Constant Pressure setting.
Pumps supplied with these rigs are designed to be connected to
the relevant appliance electrical connections to ensure pump over
run capability is available to manage the appliances operation.
3.6 BOILER CONNECTION KITS
These boiler connections are un-insulated and contain the
following:
LEGEND
1. Tee 1
1
/
4
" X
3
/
4
" X 1
1
/
4
"
2. Brass union
3
/
4
" X
3
/
4
"
3. Safety relief valve 3 bar
4. 1
1
/
4
" X
1
/
2
" X 1
1
/
4
" Tee
5. Drain plug
6. Pump fitting
7. Non return valve
8. Pump inc. gaskets
9. 1
1
/
4
" taper male to 1
1
/
4
" parallel hex adapter
Note. For boiler connection assembly, refer to Frame 5.3
3.7 FREE-STANDING FRAMES
The low height frames are designed to provide a compact floor
mounted structure capable of having any of the Evomax range of
appliances fitted to them. Incorporating all the required mountings
and assembly systems to bolt up to three frames together in a
side by side format and mount the relevant water and gas heater
kits.
Provision is also provided to allow the frames to be bolted to the floor.
Note: Floor mounting bolts are NOT provided.
3.8 INSTALLATION AREA AND DIMENSIONS
Care must be taken to ensure adequate access for boiler /
cascade system installation and servicing.
A minimum of 450mm must be provided from the front of the
installed boilers to facilitate boiler servicing.
Consideration to connecting heating flow and return pipework,
gas supply and condensate drainage must be given. Routing
of the condensate drain must be made to allow a minimum fall
of 1 in 20 away from the installed boilers, throughout its length.
Adequate room above the boilers must be provided to install and
service the boiler flue system. Further information with respect
to flue and condensate drain connection is provided in the
installation and servicing instructions provided within the boilers
packaging carton.
3 SYSTEM COMPONENTS
3
2
1
9
FLOW
RETURN
4
5
6
7
8
Note
.
Isolating Valves
are fitted to water
header along with
flexible connecting
pipes.