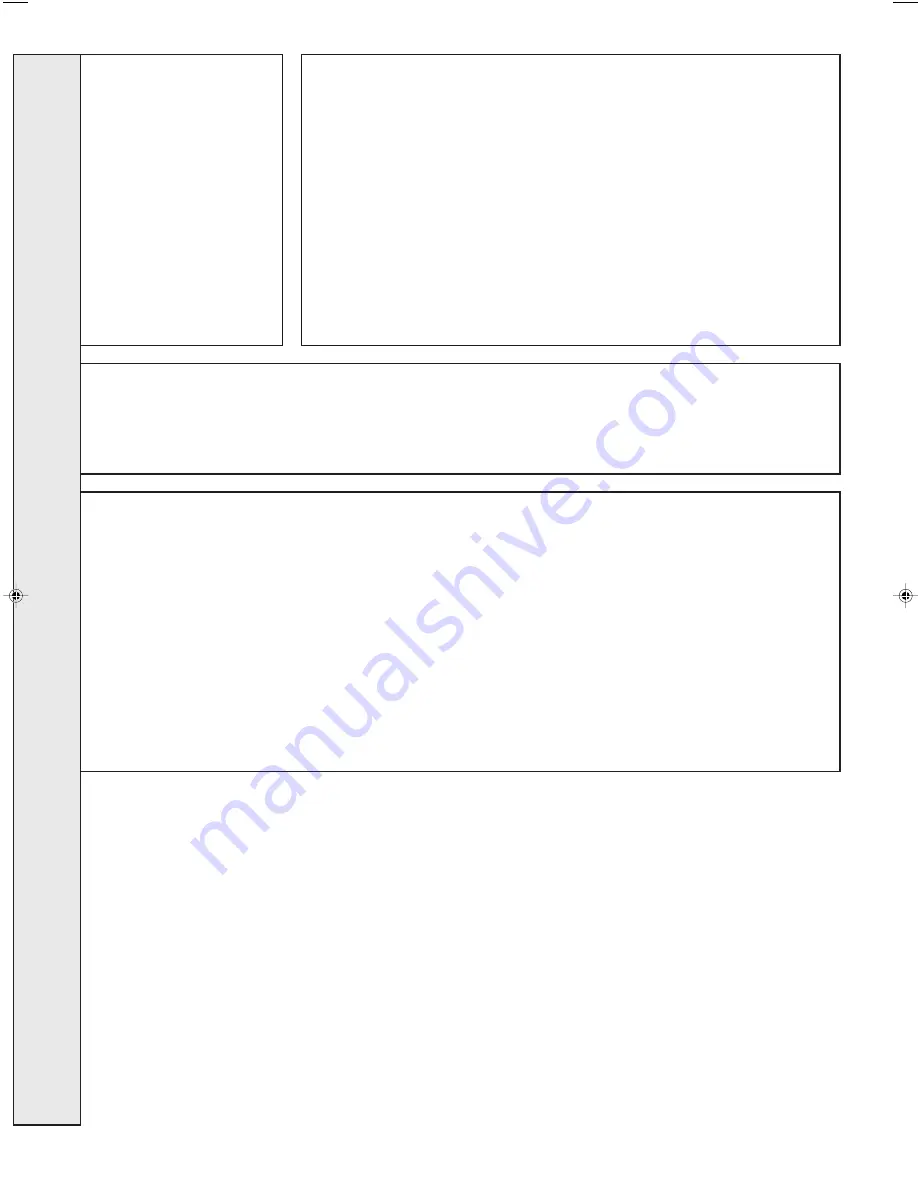
SERVICING
24
Concord CXSi/H -
Installation & Servicing
25 ADJUSTMENT OF WATER FLOW RATE THROUGH THE BOILER
When commissioning the heating/domestic hot water system the shunt pump must be
adjusted to give the minimum flow rate given in Table 4, when that part of the system
intended to be used for dissipation of residual heat only is in operation.
ROUTINE OPERATION
Full instructions covering routine lighting and operation of
the boiler are given on the Lighting and Operation
Instruction Label located on the inside of the casing door.
Draw the attention of the boiler owner or their
representative to the Lighting and Operating Instruction
Label on the inside of the front panel. Give a practical
demonstration of the lighting and shutting down of the
boiler.
Describe the function of the boiler and system controls and
show how they are adjusted and used.
26 HANDING OVER
Hand over these, the User’s Instructions and the Commissioning &
Servicing Log Book to the customer and request him to keep them in
a safe place for ready reference.
IMPORTANT.
Point out to the owner that the boiler must have
regular maintenance and cleaning, at least annually, in order to
ensure reliable and efficient operation. Regular attention will also
prolong the life of the boiler and should preferably be performed at
the end of the heating season.
After servicing, complete the service section of the log book and
return it to the owner or their representative.
Recommend that a contract for this work should be made with a
CORGI registered installer.
24 TESTING
23 SPILLAGE CHECK
Check that there is no spillage
of combustion products from
the boiler draught diverter by
carrying out a spillage test, as
detailed in BS. 5440:1.
Check the main burner responds correctly to manual on/off operations of any controls fitted in
the gas control circuit.
Check the operation of the flame failure safety system by lighting the boiler and then turning
the gas inlet cock off.
The Burner On light will go out and the controls will try to relight the boiler. After a period of
about 5 seconds, the Lockout light will be illuminated.
Turn on the gas cock again and press in and release the Lockout button. The boiler will
relight.
Complete the Commissioning section of the boiler log book.
Important Commissioning / Operating Instructions:
Do not operate this appliance for long periods or take any combustion readings with the
casing or any part of the casing removed.
INST
ALLA
TION
157294-3.pmd
11/8/2005, 9:59 AM
24