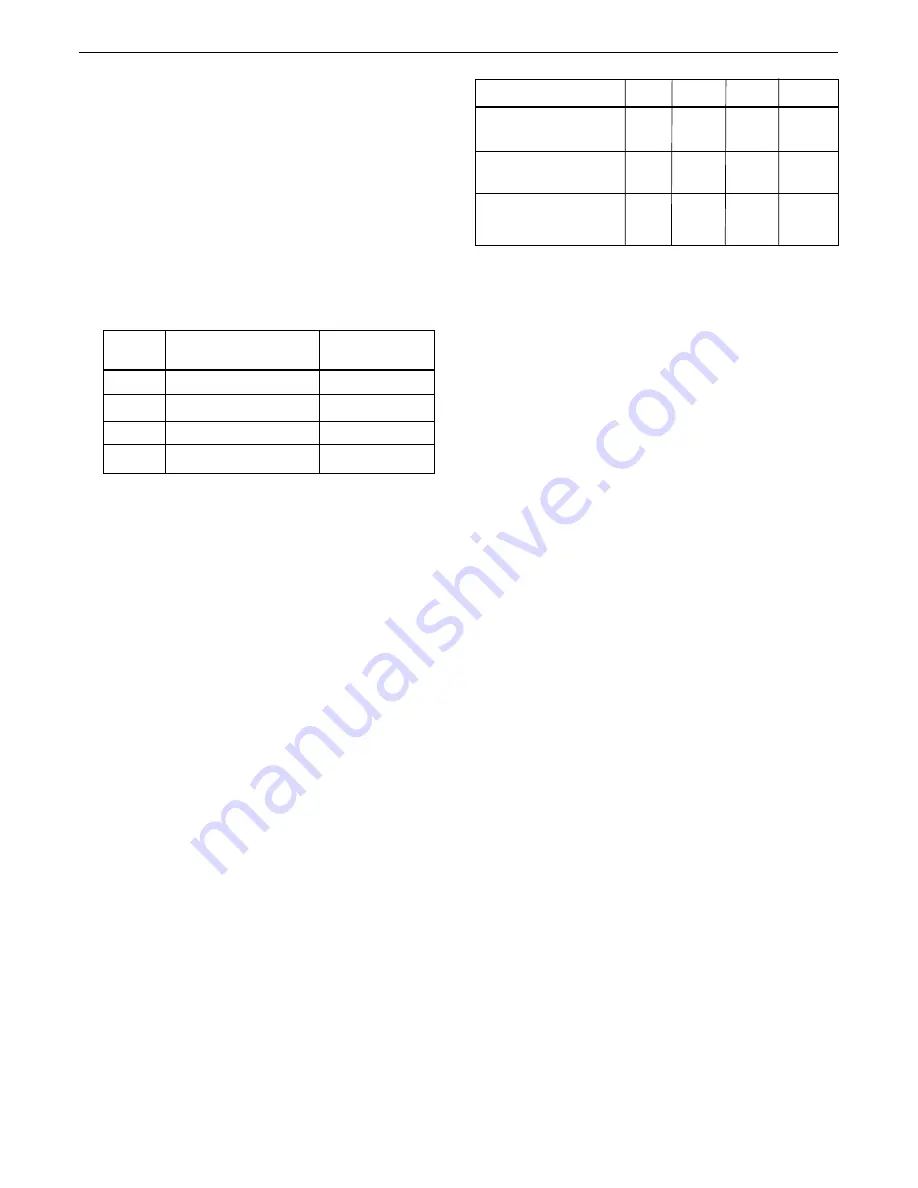
7
GENERAL
Classic
Slimline FF
-
Installation & Servicing
Boiler Size
FF
230
240
250
260
Boiler
kW
8.8
11.7
14.6
17.6
Output
Btu/h x 1000
30
40
50
60
Water Flow
l/min
11.4
15.2
19.0
22.8
Rate
gal/h
150
200
250
300
Pressure
mbar
22.0
20.4
31.5
41.7
Loss
in wg
8.9
8.3
12.6
16.7
THERMOSTATIC RADIATOR VALVES
Caradon Plumbing Limited
recommend that heating systems
utilising full thermostatic radiator valve control of temperature in
individual rooms should also be fitted with a room thermostat
controlling the temperature in a space served by radiators not fitted
with such a valve as stated in BS. 5449.
When thermostatic radiator valves are used, the space heating
temperature control over a living / dining area or hallway having a
heating requirement of at least 10% of the boiler heat output should
be achieved using a room thermostat, whilst other rooms are
individually controlled by thermostatic radiator valves. However, if
the system employs thermostatic radiator valves on all radiators, or
two port valves without end switches, then a bypass must be fitted
to ensure a flow of water should all valves be in the closed position.
ELECTRICAL SUPPLY
This appliance must be efficiently earthed.
Wiring external to the appliance MUST be in accordance with the
current I.E.E. (BS.7671) Wiring Regulations and any local
regulations which apply.
The point of connection to the mains should be readily accessible
and adjacent to the boiler, except that for bathroom installations;
the point of connection to the mains MUST be situated outside of
the bathroom.
Note.
Where a room sealed appliance is installed in a room
containing a bath or shower then the appliance and any electrical
switch or appliance control utilising mains electricity should be so
situated that it cannot be touched by a person using the bath or
shower. See Frame 38 for details.
1.
It is NOT necessary to have a purpose provided air vent in the
room or internal space in which the boiler is installed.
2.
If the boiler is to be installed in a cupboard or compartment,
permanent air vents are required (for cooling purposes) in the
cupboard/compartment, at both high and low levels. The air
vents must either communicate with room/internal space, or
be direct to outside air. The minimum effective areas of the
permanent air vents, required in the cupboard/compartment,
are specified as follows and are related to maximum rated
heat input.
3.
Both air vents MUST communicate with the same room or
internal space or MUST be on the same wall to outside air.
4.
In siting the air vents care must be taken to avoid the freezing
of pipework.
WATER CIRCULATION SYSTEM
The boiler must NOT be used for direct hot water supply. For the
types of system and correct piping procedure refer to 'Introduction'
and Frame 1.
The central heating system should be in accordance with BS.6798
and, in addition, for Smallbore and Microbore systems, BS. 5449.
The domestic hot water system, if applicable, should be in
accordance with the relevant recommendations of BS. 5546. Copper
tubing to BS. 2871:1 is recommended for water carrying pipework.
The hot water storage cylinder MUST be of the indirect type and
should preferably be manufactured of copper.
Single feed, indirect cylinders are not recommended and MUST
NOT be used on sealed systems.
The appliances are NOT suitable for gravity central heating, nor
are they suitable for the provision of gravity domestic hot water.
The hot water cylinder and ancillary pipework, not forming part of
the useful heating surface, should be lagged to prevent heat loss
and any possible freezing - particularly where pipes run through
roof spaces and ventilated under floor spaces.
Boilers not fitted to a sealed system must be vented.
IMPORTANT
Draining taps MUST be located in accessible positions, which permit
the draining of the whole system - including the boiler and hot water
storage vessel. They should be at least
1/2" BSP
nominal size and
be in accordance with BS. 2879.
The boiler is fitted with a special drain plug, which is provided, to
drain the BOILER ONLY, in the event of the system drain plug being
unable to do so. The hydraulic resistance of the boilers, at MAXIMUM
OUTPUT with an 11
O
C (20
O
F) temperature differential, are shown in
Table 5.
Maximum boiler operating temperature should be 82
O
C (180
O
F).
WATER TREATMENT
These boilers incorporate a cast iron heat exchanger. As part of
the installation the central heating system should be thoroughly
flushed with appropriate water treatment in order to comply with
BS7593:1992.
Caradon Plumbing Limited
recommend the use of Fernox or Betz
Dearborn water treatment products which must be used in
accordance with the manufacturers instructions. For further
information contact :-
Fernox Manufacturing. Co. Ltd
, Tandem House, Marlowe Way,
Croydon, Surrey CRO 4XS, tel. 0870 5601 5000 or
Betz Dearborn Ltd
, Widnes, Cheshire, tel. 0151 424 5351
IMPORTANT.
Any other treatment for this product will render the
guarantee of Caradon Plumbing Ltd INVALID.
Notes.
1.
If an inhibitor is used, and in hard water areas where treatment
to prevent lime deposits is necessary, it is most important that
the water treatment MUST be maintained at the correct
concentrations recommended by the treatment manufacturer.
2.
Artificially softened water must not be used in the system, under
any circumstances
.
Table 5 - Water flow rate and pressure loss
Table 4 - High and low vent areas
Boiler
Air from room/internal
Air direct from
space, cm (in
2
)
outside, cm (in
2
)
FF 230
102
(16)
51
(8)
FF 240
135
(21)
68
(11)
FF 250
170
(26)
83
(13)
FF 260
198
(31)
102
(16)