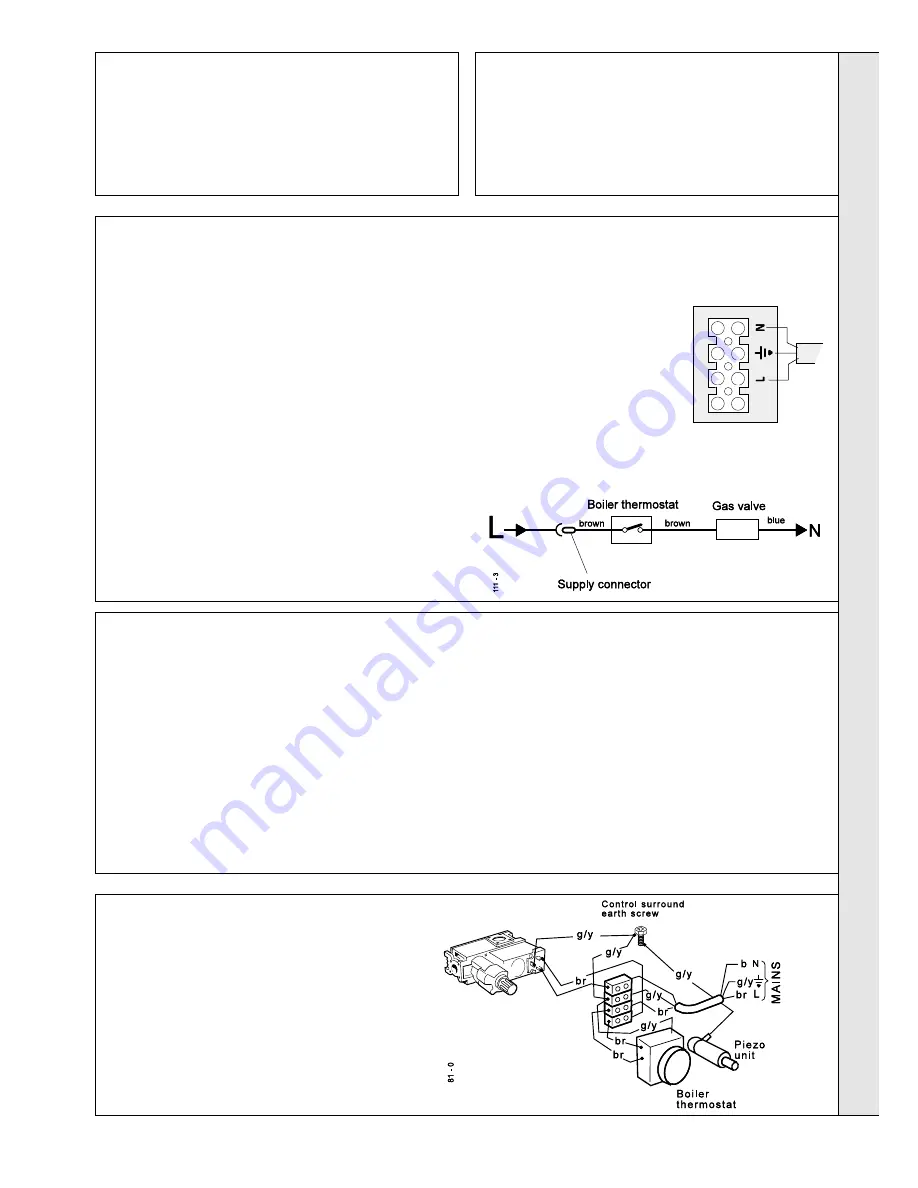
Classic
LXRS, RS
-
Propane Installation
13
15 GAS CONNECTION
A MINIMUM gas pressure of 37 mbar (14.8 in.w.g.) MUST be
available at the boiler inlet with the boiler operating.
The main gas cock is on the left hand side of the gas control valve,
as shown (Frame 25).
To facilitate connection the gas cock may be removed from the gas
control valve.
16 WATER CONNECTIONS
1.
Remove the plastic plugs from the flow and return
pipes.
2.
Make all water connections and check for water
soundness.
INSTALLATION
INST
ALLA
TION
17 ELECTRICAL CONNECTIONS
WARNING
.
The appliance MUST be efficiently earthed.
A mains supply of 230 V ~ 50 Hz is required.
All external controls and wiring MUST be suitable for mains
voltage. Wiring should be in 3-core PVC insulating cable NOT
LESS than 0.75 mm
2
(24 x 0.2 mm) to BS.6500, Table 16.
Wiring external to the boiler MUST be in accordance with current
l.E.E. (BS7671) Wiring Regulations and local regulations.
Connection must be made in a way that allows complete isolation
of the electrical supply - such as a double pole switch, having a
3mm (1/8") contact separation in both poles or a plug and socket,
serving only the boiler and system controls. The means of
isolation must be accessible to the user after installation.
Note.
If the optional Programmer Kit is to be fitted, refer to the
instructions provided with the kit, ignore this frame and go to
Frame 18.
The internal wiring of the control box is shown in Frame 19.
DETAIL OF CONTROL BOX TERMINALS
Note.
In order to connect the incoming mains wires, first
remove the control box fixing screw then pull the box forward
and downward to disengage.
Ensure that the earth lead is longer
than the live and neutral so that if the
cable slips in its anchorage the
current carrying conductors become
taut before the earth conductor and
that the cable is routed through the
strain relief clamp. Ensure all cables
are secure and that no basic
insulation is accessible outside of
the control box.
3.
Controls that switch the circulation pump only ON and OFF, e.g. a room
thermostat, MUST be wired in series with the pump in the live pump lead.
4.
If a proprietary system is used, follow the instructions supplied by the
manufacturer.
5.
SYSTEM DESIGNS FEATURING CONTROLS OR WIRING
ARRANGEMENTS WHICH ALLOW THE BOILER TO FIRE WHEN
THERE IS NO PUMPED OR GRAVITY CIRCULATION TAKING PLACE
SHOULD NOT BE FITTED.
Advice on required modifications to the wiring may be obtained from the
component manufacturers.
Notes
1.
Connections between a frost thermostat and the time
control should be made without disturbing other wiring.
2.
A frost thermostat should be sited in a cool place in the
house, but where it can sense heat from the system.
LEGEND
b
blue
br
brown
g/y
green/yellow
18 EXTERNAL CONTROLS
The wiring diagrams illustrated in Frames 20-23 cover the systems
most likely to be fitted to this appliance.
For wiring external controls to the
Classic RS
boiler, reference
should be made to the system wiring diagrams supplied by the
relevant manufacturer, in conjunction with the wiring diagrams
shown in Frames 19-23.
Difficulty in wiring should not arise, providing the following directions
are observed:
1.
Controls that switch the system ON and OFF, e.g. a time
switch, MUST be wired, in series, in the live mains lead to the
boiler.
2.
Controls that override an ON/OFF control, e.g. a frost
thermostat, MUST be wired into the mains lead, in parallel,
with the control(s) to be overridden - refer to Frame 23.
19 PICTORIAL WIRING
FLOW WIRING DIAGRAM