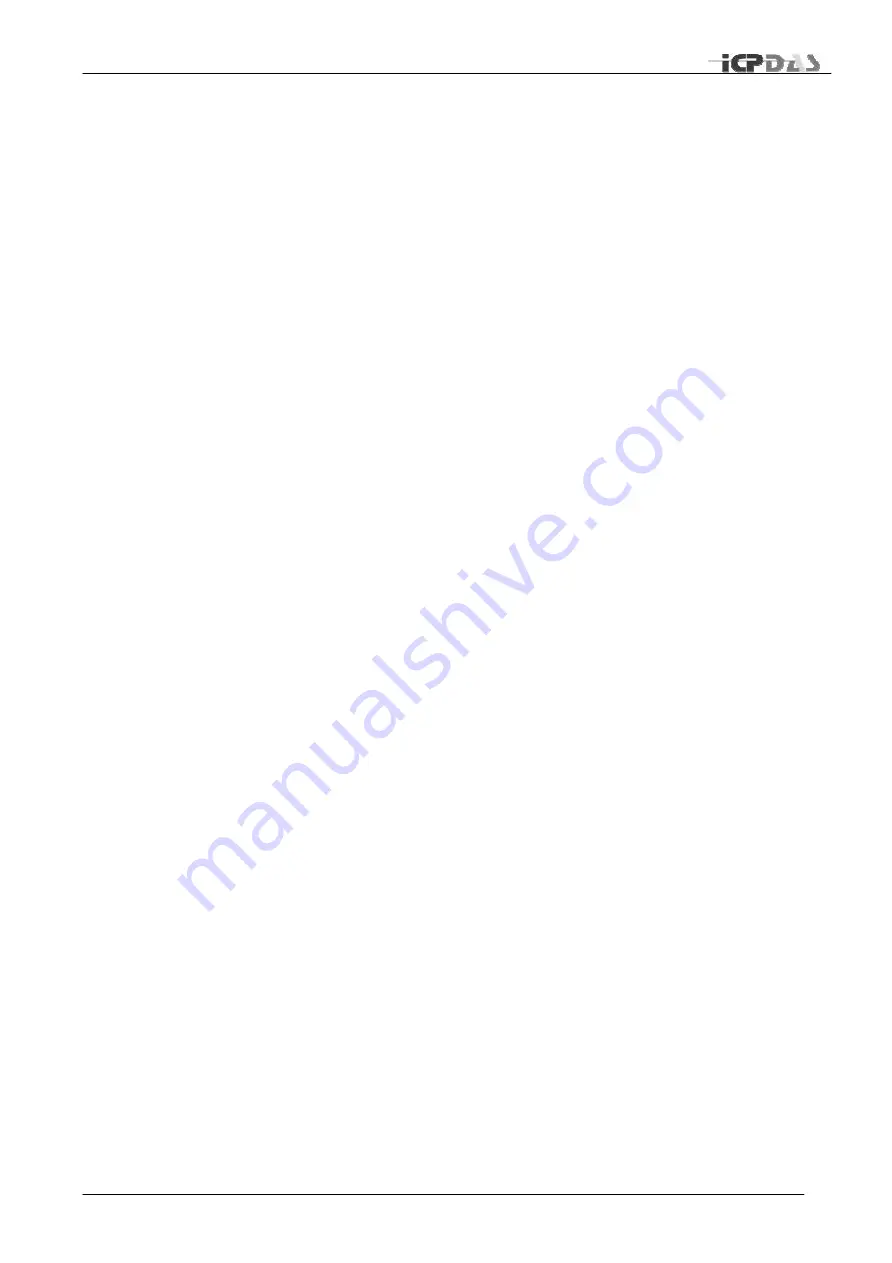
Industrial Redundant Ring Switch
– RS Series User Manual
It is likely that these people will not be fully trained on Ethernet and the protocols that are
in operation, nor will they fully understand the principles of SNMP etc. However, with a
fault conta
ct, fault LED‟s and graphical interface implemented they have a multi-level
approach to fault finding:
The fault contact is hard-wired to an alarm on a control panel or as an input to a DCS. If a
link failure occurs (between two switches or an Ethernet Device) or a network failure
occurs the fault contact on the Switches will be energized. The Maintenance Engineer
can easily locate the fault.
With the increased use of Ethernet in the field to pass critical data the greater the
reliability in network infrastructure. Where multiple rings are configured in a system it is
also critical that the links between the rings are also duplicated to provide enhanced
redundancy. This can be achieved using Multi-ring Redundancy
Industrial Fiber Optic
Why Fiber Optics?
The utilization of fiber optic data transmission for industrial automation and process
control has become increasingly popular over the past decade.
A basic fiber optic system, using an optical transceiver circuit and fiber optic media, offers
a wide array of benefits that are not available with traditional copper conductors.
Advantages of Fiber Optic Data Transmission Technology
High data rate and wide bandwidth
Immunity to EMI/RFI and lightning damage
No ground loops
Low attenuation (data loss)
Longer distance
– up to 1.8 miles (3 km) with Muliti Mode fiber and over 15 miles
(25 km) with Single Mode fiber
Small cable diameter fits almost anywhere - requires less duct space
Light weight
No sparks if cut
– ideal for Hazardous Area applications
No electric shock hazard
Secure communications
Flexible networking topologies
Corrosion resistant
Longer life expectancy than copper or coaxial cable
Economical total system cost
Disadvantages of Electronic Cabling (Twisted Pair (TP), Coax, Twinax)
In selecting the signal/data transmission technology for your Industrial Automation and
Process Control networking, the following limitations of electronic cabling should be
considered:
Cabling hassles: weight, routing, size, attenuation and cross-talk
Distance between terminals and hosts is severely limited
Large diameter cable fills plenums and conduits
Needs to be routed away from power cabling
Poor security
Limited topologies
7
TDRS4050601