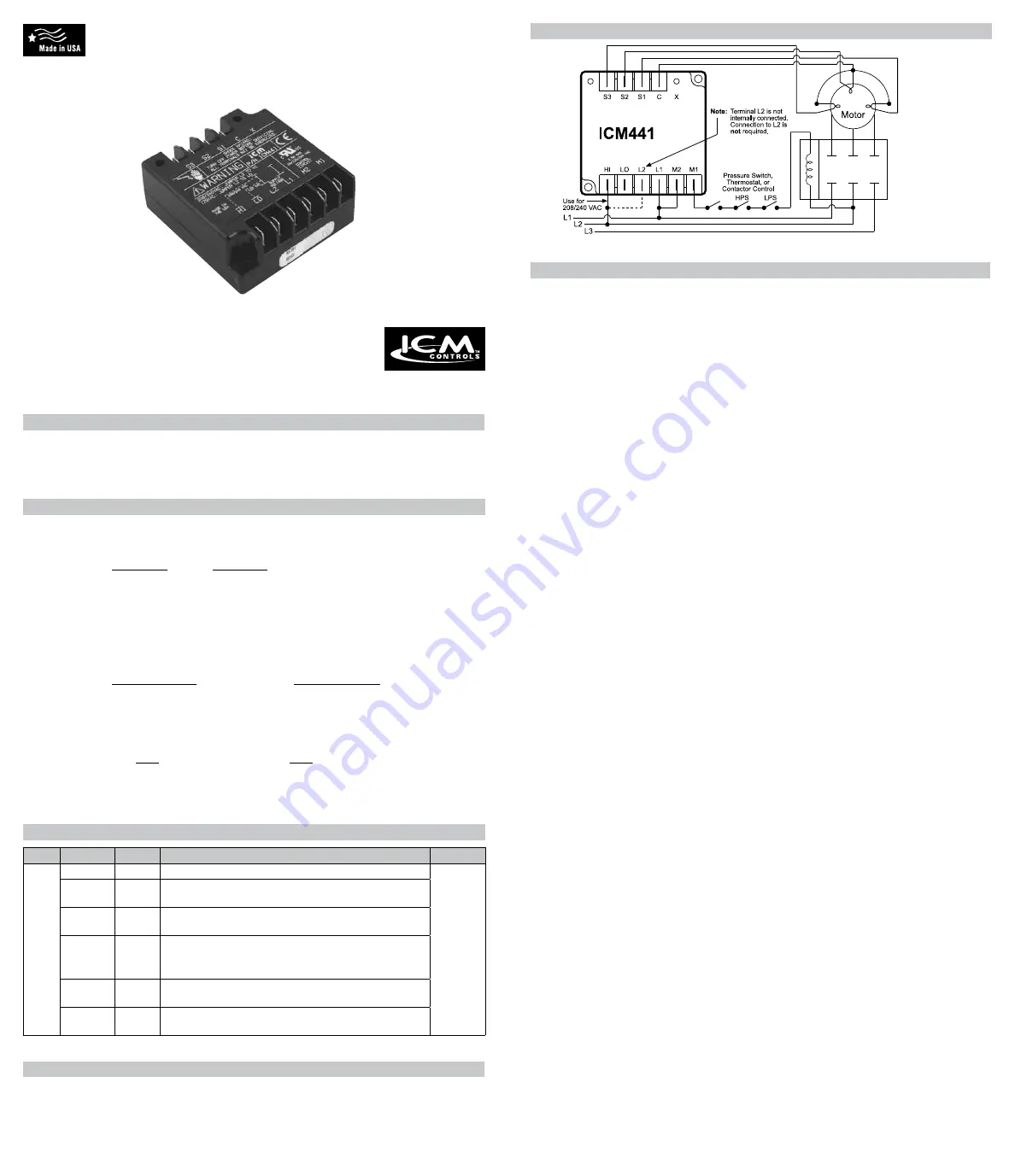
Mode of Operation
The
ICM441
is designed to individually monitor 3 PTC temperature sensors which are wound into
each phase winding of a motor. If any winding or incoming line power is beyond the safe operating
range of the motor, the
ICM441
will lock the motor out of operation until the inputs fall back into
the safe operating range. The
ICM441
can sense shorted or open sensors, in addition to providing
isolation to each sensor to prevent damage to the monitor in the event a sensor shorts to a winding or
case ground.
ICM441 System Wiring Diagram
Installation
This installation is only to be performed by a qualified electrician in accordance with NEC standards.
Ensure all power to both motor and control circuits is removed before starting installation. Verify there
is no voltage present with a voltmeter.
This control is typically installed on a three phase motor, where the power for this control comes
directly off one set of phases to the motor (see System Wiring Diagram). If you have an installation
where a step-down transformer drops the voltage supply for this control, please see the section titled
“Step-Down Transformer Installations.”
In applications where this control replaces an existing motor protector of the same voltage and
sensor ratings, label each wire connected to the defective unit before you remove it from that control.
Terminal designations should correspond to terminals on the
ICM441
.
Step 1: Verify sensor integrity
There should be four (4) small gage wires coming from the motor housing, which connect to
internally-wound sensors. There are three sensor wires, and one sensor common wire. At normal
temperature, a motor which has been de-energized for at least one hour will have sensors with a
normal operating resistance of approximately 1K
Ω
. A sensor must be in the range of 500
Ω
to 3K
Ω
when measured with a resistance meter between the sensor common wire and each sensor wire
(S1, S2, and S3). If a sensor is found outside of this range, you must deactivate that sensor from all
sensing, as described in the section labeled “Bypassing A Sensor.”
Step 2: Connect all sensor wires
There should be four (4) small gage wires coming from the motor housing, which connect to
internally-wound sensors. There are three sensor wires, and one sensor common wire. The sensor
common wire connects with female 1/4” quick-connects to the
ICM441
terminal “C” (common). All of
the individual sensor wires connect to the
ICM441
terminals “S1, S2, and S3” with female 1/4” quick-
connects.
Connect sensor wire S1 to terminal “S1,” connect sensor wire S2 to terminal “S2,” and connect
sensor wire S3 to terminal “S3.” The order of these sensors is not important, simply ensure that
each sensor wire is connected to a sensor input on the
ICM441
. Consult the System Wiring Diagram
should any other questions arise.
Step 3: Connect the control circuit
There is always a contactor that supplies operating current to the motor this device protects. This
contactor has an internally wound coil with a specific operating voltage rating. Ensure the operating
voltage rating of this coil is in the range of 24 VAC to 277 VAC, since the
ICM441
has a maximum
rating of 277 VAC on its internal control contacts.
Usually, one side of the contactor coil is connected to power common. Whether a transformer is used
to step-down the control voltage (see the section titled “Step-Down Transformer Installations”) or if it
is powered by line voltage, one side of the coil is typically connected directly to this common. Leave
this connection to the contactor coil as is.
The other side of the contactor coil typically is energized by “hot” through a series of switches, usually
by some type of thermostat, pressure switch, or safety switch. Remove this “switched side” coil wire
from the contactor coil and connect to the
ICM441
terminal “M2” using a 1/4” female quick-connect.
Fashion another wire with female 1/4” quick-connects on both ends to connect between the
ICM441
terminal “M1” and the “switched side” of the coil you just removed the wire from. Consult the System
Wiring Diagram should any other questions arise.
Step 4: Supply operating voltage to the ICM441
The operating voltage required for this unit is 120/240 VAC, 50/60 Hz. Determine what voltage range
will be supplied to the
ICM441
and connect voltage as follows:
• 85-135 VAC: Connect Neutral (or “common” on step-down transformer applications) to the terminal
labeled “L1” on the
ICM441
, via a 1/4” female quick-connect. Connect L1 (or “hot” on step-down
transformer applications) to the terminal labeled “LO” on the
ICM441
, via a 1/4” female quick-
connect. You may connect an additional wire between terminals “LO” and “L2” on the
ICM441
, but
this option is not required. Terminal “L2” has no internal connection, it is provided for backward
compatibility to other models of motor protector.
• 185-277 VAC: Connect L1 (or “common” on step-down transformer applications) to the terminal
labeled “L1” on the
ICM441
, via a 1/4” female quick-connect. Connect L2 (or “hot” on step-down
transformer applications) to the terminal labeled “HI” on the
ICM441
, via a 1/4” female quick-
connect. You may connect an additional wire between terminals “HI” and “L2” on the
ICM441
, but
this option is not required. Terminal “L2” has no internal connection, it is provided for backward
compatibility to other models of motor protector.
Consult the System Wiring Diagram should any other questions arise. Your
ICM441
is now ready for
application of power to the motor and control circuits.
Specification
ENVIRONMENTAL
Epoxy Encapsulated:
For use in extreme environmental conditions
Connection Terminals:
0.25” male spade terminals
Temperature Range:
-40ºC to 85ºC
(storage)
-40ºC to 70ºC
(operating)
Maximum Operating/Storage Relative Humidity:
95% non-condensing
Sensor Shorted, Open, Over Temperature Detection:
0.1 second maximum
Power Loss Detection:
0.1 second maximum
Nominal anti-short cycle Time:
4 minutes (+/- 60 seconds)
Case Dimensions:
3”L x 3.25”W x 1.5”H
ELECTRICAL
User Selectable Operating Voltage:
90-140 VAC RMS and 185-270 VAC RMS (based on field wiring)
Low Voltage Cutout:
85 (+/-5.5) VAC RMS (using 120 VAC input) 170 (+/-10) VAC RMS (using 208 VAC input)
Over Temperature Trip:
Any one sensor input in excess of 11K
Ω
(+/- 1K
Ω
)
Over Temperature Reset:
All three sensor inputs must be less than 3K
Ω
(+/- 500
Ω
)
Shorted Sensor Trip:
Any one sensor input less than 250
Ω
(+/- 50
Ω
)
Shorted Sensor Reset:
All three sensor inputs must be greater than 500
Ω
(+/- 100
Ω
)
N.O. Relay Contact Rating (M1, M2):
2.5 amps resistive @ 277 VAC RMS 2.5 amps inductive @ 277 VAC RMS
Low Power Consumption:
23mA
(nominal) @ 120 VAC @ 25ºC
21mA
(nominal) @ 240 VAC @ 25ºC
Terminal “L2” is Not Internally Connected:
Provided for backward compatibility to competitor models. Not
required for new installations
Temperature Sensors:
Monitors industry standard (3BA and 10BA sensors)
ICM441 Cross Reference Guide
ICM #
T.I. #
Mars #
Copeland #
Bristol #
441
31AA1606 E
241680
15AA1603 B
37304
Replaces:
071-9800-01
Used On:
Copeland: GR, SE
15AA1603 C
37306
Replaces:
071-9800-00
Used On:
Copeland: GR, SE
31AA1600 E
37322
Replaces:
071-0376-01
071-0397-00
071-0424-00
071-0376-02
071-0397-01
071-0424-01
Used On:
Copeland: 4R, 6R, BR, M, 2D, 3D, 4, 6, 8, both Reed & Discus
models
15AA1600 B
37300
Replaces:
071-0376-02
071-0397-01
071-0424-01
Used On:
Copeland: 4R, 6R, BR
15AA1600 C
37302
Replaces:
071-0376-01
071-0397-00
Used On:
Copeland: 4R, 6R, BR
Installation of the ICM441 shall be performed by trained technicians only. Adhere to all local
and national electric codes.
Disconnect all power to the system before making any connections.
Caution
ICM441
Motor Protector
Installation, Operation & Application Guide
For more information on our complete range of American-made products – plus
wiring diagrams, troubleshooting tips and more, visit us at
www.icmcontrols.com